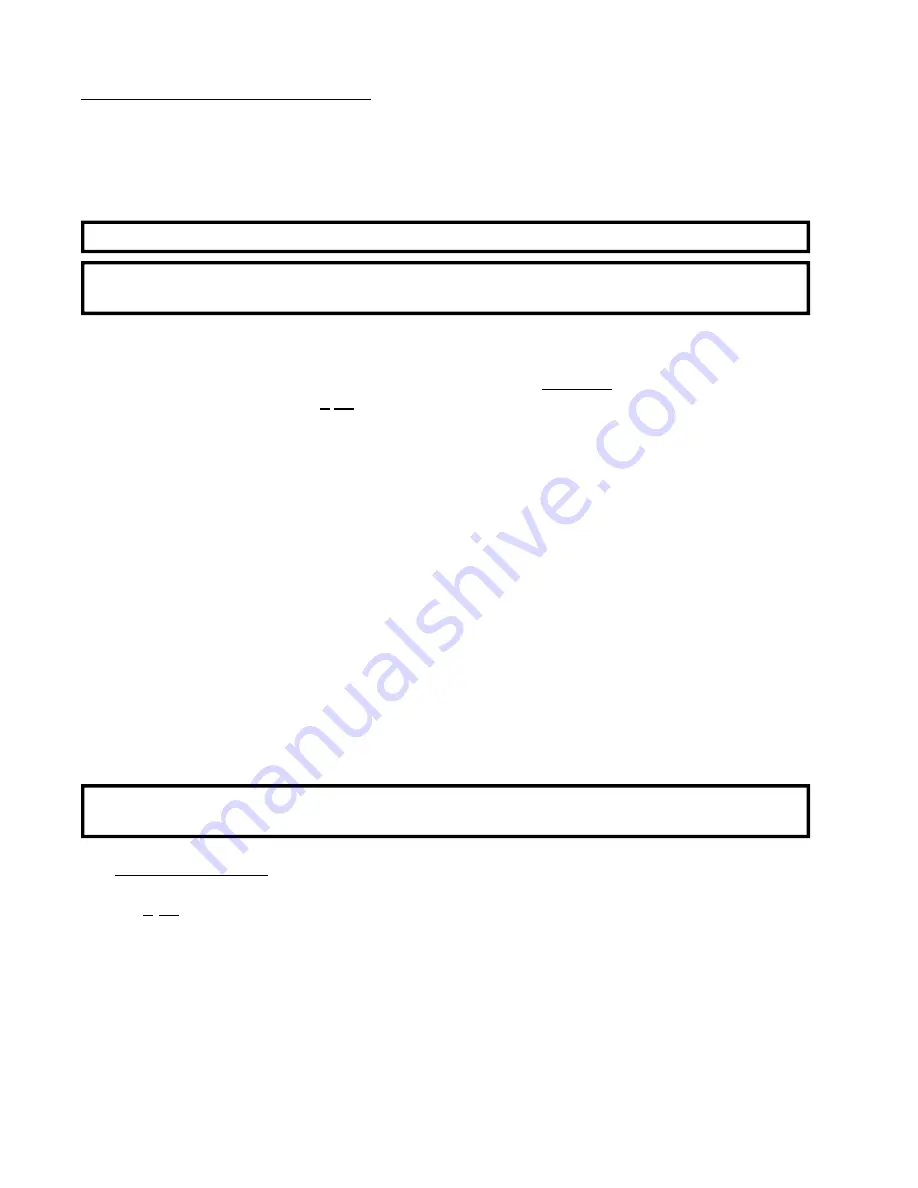
8
E. EXHAUST REQUIREMENTS
Exhaust ductwork
should be
designed and installed by a competent technician. Improperly sized ductwork will
create excessive back pressure which results in slow drying, increased use of energy, overheating of the dryer, and
shutdown of the burner by the airflow (sail) switches, burner hi-limits, or basket (tumbler) hi-heat protector
thermostats. The dryer
must be
installed with a proper exhaust duct connection to the outside.
CAUTION:
This dryer produces combustible lint and
must be
exhausted to the outdoors.
CAUTION: IMPROPERLY SIZED OR INSTALLED EXHAUST DUCTWORK CAN
CREATE A POTENTIAL FIRE HAZARD
.
Where possible, it is suggested to provide a separate exhaust duct for each dryer. The exhaust ductwork
should
be
laid out in such a way that the ductwork travels as directly as possible to the outdoors, with as few turns as
possible. It is suggested that the use of right angle turns in the ducting be avoided; use 30º or 45º angles instead.
The shape of the exhaust ductwork is not critical, so long as the minimum cross section area is provided.
If the exhaust ductwork is unusually long (over 20 feet [6.1 meters]) or has numerous elbows, the cross section
area of the ductwork
must be
increased in proportion to its length or the number of elbows in it. In calculating
duct size, the cross section area of a square rectangle duct
must be
increased 20 percent (20%) for each additional
20 feet (6.1 meters). The diameter of a round exhaust
should be
increased 10 percent (10%) for each additional
20 feet (6.1 meters). Each 90º elbow is equivalent to an additional 15 feet (4.57 meters), and each 45º elbow, an
additional 10 feet (3.05 meters).
The ductwork
should be
smooth inside with no projections from sheet metal screws or other obstructions, which
will collect lint. When adding ducts, the duct to be added should overlap the duct to which it is to be connected.
Also, inspection doors
should be
installed at strategic points in the exhaust ductwork for periodic inspection and
cleaning.
To protect the outside end of the horizontal ductwork from the weather, a 90º elbow bent downward
should be
installed where the exhaust exits the building. (Refer to the
illustration
on the following page.) If the exhaust
ductwork travels vertically up through the roof, it
should be
protected from the weather by using a 180º turn to
point the opening downward. (Refer to the
illustration
on the following page.) In either case, allow at least twice
the diameter of the duct between the duct opening and nearest obstruction.
IMPORTANT:
DO NOT
use screens, louvers, or caps on the outside opening of the exhaust
ductwork.
1. Multiple Dryer Venting
If it is not feasible to provide separate exhaust ducts for each dryer, ducts from individual dryers may be
channeled into a “common main duct.” (Refer to the
illustration
on the following page.) The individual
ducts should enter the bottom or side of the main duct at an angle not more than 45º in the direction of
airflow. The main duct
should be
tapered, with the diameter increasing before each individual duct is
added. The cross section area
should be
60 square inches (387.10 square centimeters) for each 8-inch
(20.32 cm) duct added.