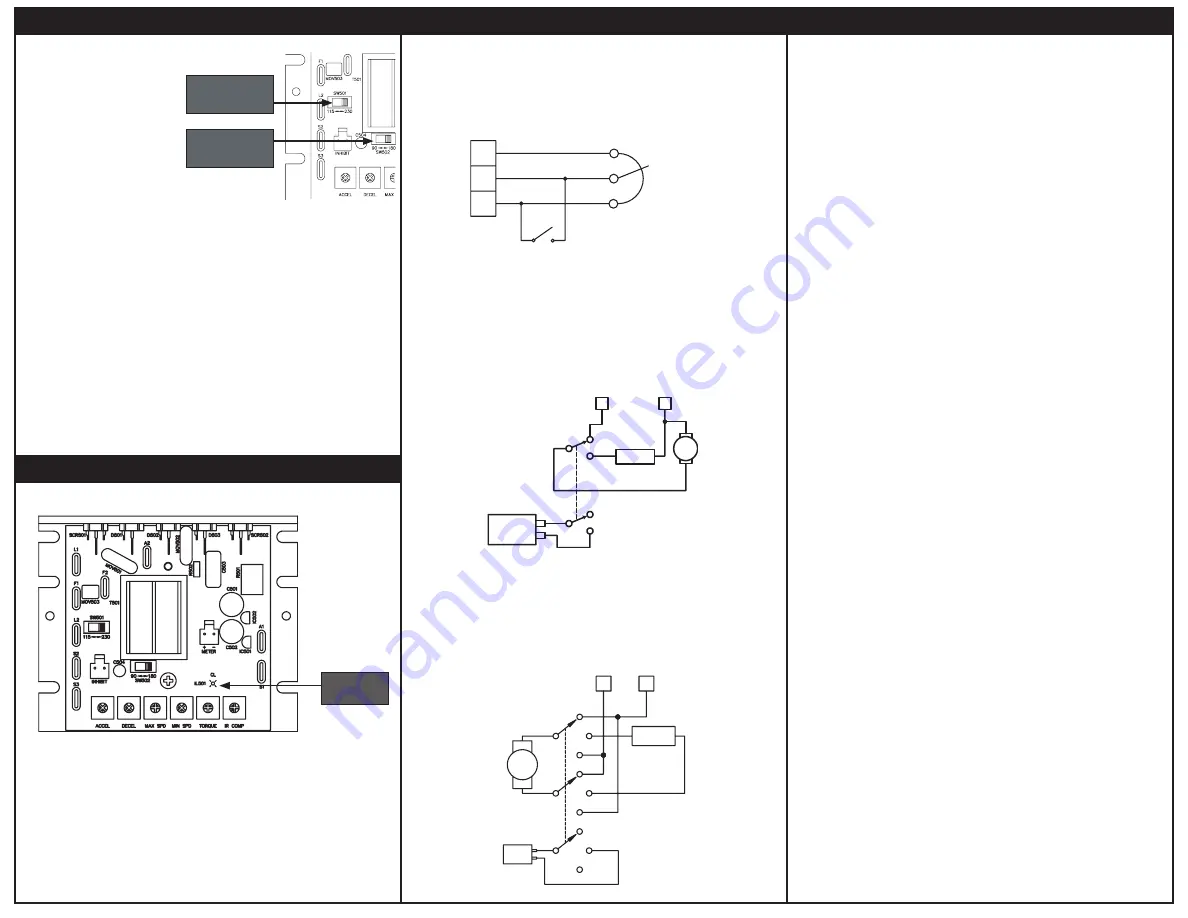
QSG-0001 rev 2
Calibration
Minimum Speed (MIN SPD):
The MIN SPD setting determines the minimum motor speed when the
speed adjust potentiometer is set for minimum speed. It is factory set for zero speed. To calibrate the
MIN SPD:
1. Set the MIN SPD trim pot full CCW.
2. Set the speed adjust potentiometer for minimum speed.
3. Adjust the MIN SPD trim pot until the desired minimum speed is reached or is just at the
3.
threshold of rotation.
Maximum Speed (MAX SPD):
The MAX SPD setting determines the maximum motor speed when the
speed adjust potentiometer is set for maximum speed. To calibrate the MAX SPD:
1. Set the MAX SPD trim pot full CCW.
2. Set the speed adjust potentiometer for maximum speed.
3. Adjust the MAX SPD trim pot until the desired maximum speed is reached.
Check the MIN SPD and MAX SPD adjustments after recalibrating to verify that the motor runs at the
desired minimum and maximum speed.
Torque (TORQUE):
The TORQUE setting determines the maximum torque for accelerating and driving
the motor. To calibrate the TORQUE:
1. With the power disconnected from the drive, connect a DC ammeter in series with the
1.
armature.
2. Set the TORQUE trim pot to minimum (full CCW).
3. Set the speed adjust potentiometer to maximum speed (full CW).
4. Carefully lock the motor armature. Be sure that the motor is firmly mounted.
5. Apply line power. The motor should be stopped.
6. Slowly adjust the TORQUE trim pot CW until the armature current is 150% of motor rated
6.
armature current.
Continuous operation beyond this rating may damage the motor.
7. Turn the speed adjust potentiometer CCW.
8. Remove line power.
9. Remove the stall from the motor.
10. Remove the ammeter in series with the motor armature if it is no longer needed.
IR Compensation (IR COMP):
The IR COMP setting determines the degree to which motor speed is
held constant as the motor load changes. To calibrate the IR COMP:
1. Set the IR COMP trim pot full CCW.
2. Increase the speed adjust potentiometer until the motor runs at midspeed without load. A
2.
handheld tachometer may be used to measure motor speed.
3. Load the motor armature to its full load armature current rating. The motor should slow down.
4. While keeping the load on the motor, rotate the IR COMP trim pot until the motor runs at the
4.
speed measured in step 2. If the motor oscillates (overcompensation), the IR COMP trim pot
4.
may be set too high (CW). Turn the IR COMP trim pot CCW to stabilize the motor.
5. Unload the motor.
Acceleration (ACCEL):
The ACCEL setting determines the time the motor takes to ramp to a higher
speed. ACCEL is factory set for the shortest acceleration time (full CCW). To calibrate the ACCEL:
1. Set the speed adjust potentiometer for minimum speed.
2. Set the speed adjust potentiometer for maximum speed. Measure the time is takes the motor
2.
to go from minimum speed to maximum speed.
3. If the time measured in step 2 is not the desired acceleration time, turn the ACCEL trim pot
3.
CW for a longer acceleration time, or CCW for a shorter acceleration time. Repeat steps 1
3.
through 3 until the acceleration time is correct.
Deceleration (DECEL):
The DECEL setting determines the time the motor takes to ramp to a lower
speed. DECEL is factory set for the shortest deceleration time (full CCW). To calibrate the DECEL:
1. Set the speed adjust potentiometer for maximum speed.
2. Set the speed adjust potentiometer for minimum speed. Measure the time is takes the motor
2.
to go from maximum speed to minimum speed.
3. If the time measured in step 2 is not the desired deceleration time, turn the DECEL trim pot
3.
CW for a longer deceleration time, or CCW for a shorter deceleration time. Repeat steps 1
3.
through 3 until the deceleration time is correct.
MOTOR
A1
A2
FWD
BRAKE
REV
DYNAMIC
BRAKE
RESISTOR
INHIBIT
Reversing with a Dynamic Brake
A dynamic brake may be used when reversing the motor direction. The MIN SPD trim pot must be set
for zero speed. Use a three pole, three position switch rated for at least the armature voltage rating and
150% of the armature current rating. For the dynamic brake resistor, use a 40 watt minimum, high
power, wirewound resistor. Sizing the dynamic brake resistor depends on load inertia, motor voltage,
and braking time. Use a lower-value, higher-wattage dynamic brake resistor to stop a motor more
rapidly. Recommended values are 15 ohms for a 90 VDC motor and 30 ohms for 180 VDC motor.
The motor must come to a complete stop before changing directions.
REVERSING
INHIBIT
MOTOR
A2
A1
RUN
BRAKE
DYNAMIC BRAKE
RESISTOR
S3
S2
S1
RUN
DECEL TO
MIN SPEED
10K OHM
SPEED ADJUST
POTENTIOMETER
CW
Decelerate to Minimum Speed
The switch shown below may be used to decelerate a motor to a minimum speed. Closing the switch
between S1 and S2 decelerates the motor from set speed to a minimum speed determined by the MIN
SPD trim pot setting. If the MIN SPD trim pot is set full CCW, the motor decelerates to zero speed when
the switch between S1 and S2 is closed. The DECEL trim pot setting determines the rate at which the
drive decelerates. By opening the switch, the motor accelerates to set speed at a rate determined by
the ACCEL trim pot setting.
Decelerate to Minimum Speed (Coast)
See INHIBIT in the CONNECTIONS section on page 1 for a description of wiring and connection
locations.
Decelerate to Zero Speed (Dynamic Brake)
Dynamic braking may be used to rapidly stop a motor. The MIN SPD trim pot must be set for zero speed.
For the RUN/BRAKE switch, use a two pole, two position switch rated for at least the armature voltage
rating and 150% of the armature current rating. For the dynamic brake resistor, use a 40 watt minimum,
high power, wirewound resistor. Sizing the dynamic brake resistor depends on load inertia, motor
voltage, and braking time. Use a lower-value, higher-wattage dynamic brake resistor to stop a motor
more rapidly. Recommended values are 15 ohms for a 90 VDC motor and 30 ohms for 180 VDC motor.
DECELERATING & STOPPING
Operation
Current Limit
LED
Current Limit (CL):
Red LED lights whenever the drive reaches current limit.
LEDs
Input Voltage
Select (SW501)
Armature Voltage
Select (SW502)
Input Voltage Select (SW501)
Set the voltage switch SW501 to either
115V or 230V to match the AC line voltage.
Armature Voltage Select (SW502)
Set the voltage switch SW502 to either
90V or 180V to match the maximum
armature voltage.
- Verify that no foreign conductive material is present on the printed circuit board.
- Ensure that all switches are properly set.
1. Turn the speed adjust potentiometer full counterclockwise (CCW).
2. Apply AC line voltage.
3. Slowly advance the speed adjust potentiometer clockwise (CW). The motor slowly accelerates as
the potentiometer is turned CW. Continue until the desired speed is reached.
4. Remove AC line voltage from the drive to coast the motor to a stop.
STARTUP
SELECT SWITCHES
Startup
No part of this document may be reproduced
or retransmitted in any form without written permission
from American Control Electronics
®
. The information and
technical data in this document are
subject to change without notice.
American Control Electronics
®
makes no warranty of any kind
with respect to this material, including, but not limited to, the
implied warranties of its
merchantability and fitness for a given purpose.
American Control Electronics
®
assumes no
responsibility for any errors that may appear in this document and makes no commitment to
update or to keep current the information in this document.