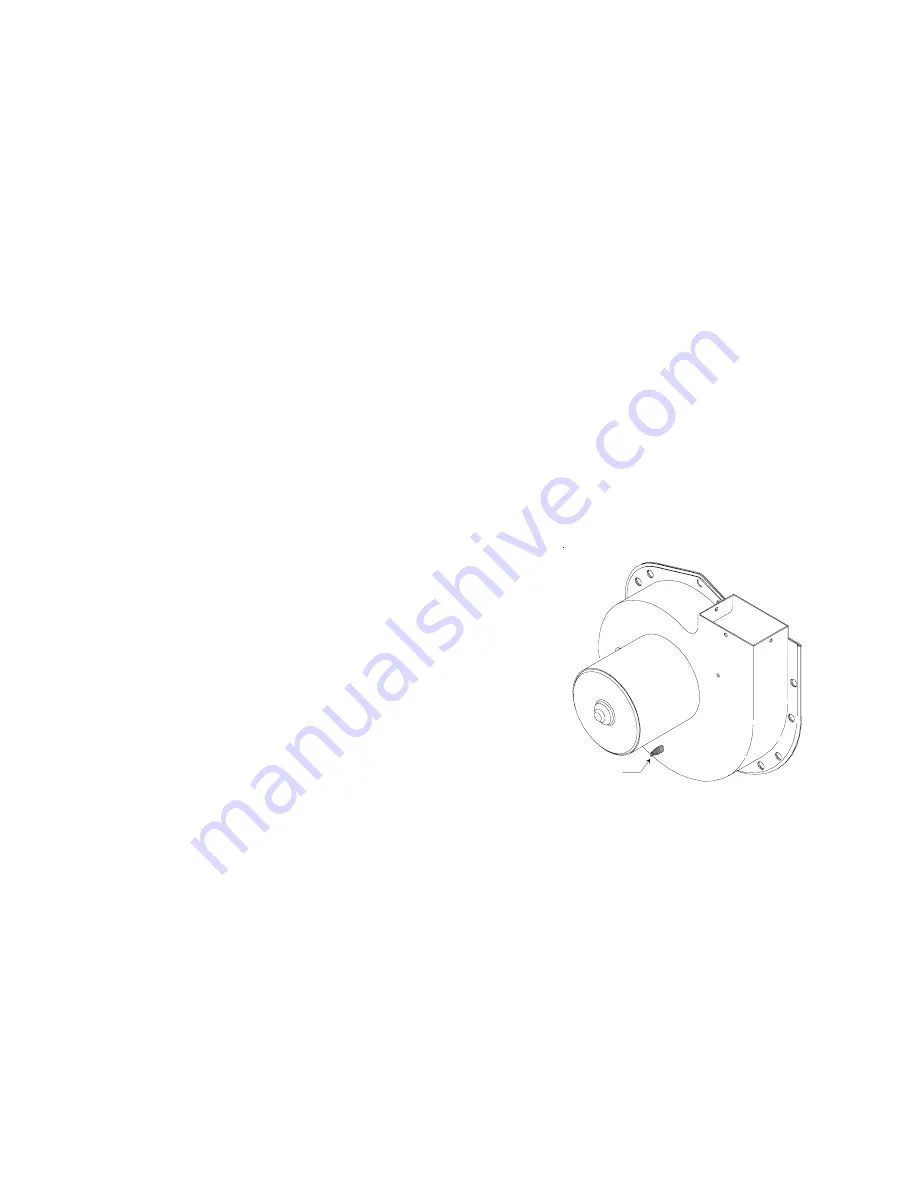
SYSTEM OPERATION
27
The timing interval can not begin until the outdoor coil tem-
perature reaches approximately 30°F. (initiation temperature)
at the defrost (30/60) control point of contact. As long as
this point of contact does not reach 60°F. (termination tem-
perature) the defrost timer board will count the number of
minutes that the compressor runs.
At the end of this (one of three) time interval, the defrost
board will call for defrost and enter the defrost mode. In this
mode the control board will energize the reversing relay, de-
energize the outdoor fan motor and energize the supplemen-
tal electric heat relay (if installed). When this occurs, the
outdoor fan motor stops and the reversing valve changes to
the cooling position sending hot refrigerant gas to the out-
door coil, which will melt any frost accumulation.
The defrost control board will stay in the defrost mode until
the outdoor coil temperature reaches approximately 60°F. at
the point of contact with the defrost (30/60 control or a maxi-
mum of 10 minutes compressor run time.
If the defrost cycle is terminated by temperature, then a new
time interval count can not begin until the defrost (30/60) control
again reaches approximately 30°F. at the point of contact. If
the defrost cycle was terminated by time, then a new time
interval could would begin immediately.
HEATING CYCLE
Package Gas Units
The heating cycle is accomplished by using a unique tubular
design heat exchanger which provides efficient gas heating
on either natural gas or propane gas fuels. The heat ex-
changers compact tubular construction provides excellent
heat transfer for maximum operating efficiency.
Inshot type gas burners with integral cross lighters are used
eliminating the need for adjustable air shutters. The same
burner is designed for use on either natural or propane gas
fuels.
The Induced Draft blower draws fuel and combustion air into
the burners and heat exchanger for proper combustion. A
pressure switch is used in conjunction with the I. D. blower
to detect a blocked flue condition.
Blower operation is controlled by the ignition control module.
The module provides for field adjustment of the blower delay
at the end of the heating cycle. The range of adjustment is for
60, 90, 120, or 180 seconds. The factory delay setting is 30
seconds delay on, 120 seconds delay off.
Honeywell Smart Valve Systems
Ignition is provided by an electronic ignition control and ce-
ramic glow bar or direct spark ignitor which heats to approxi-
mately 2500°F. A flame sensor then monitors for the pres-
ence of flame and closes the gas valve if flame is lost.
The system may be controlled by most good heating and
cooling thermostats with an adjustable heat anticipator. Some
night setback thermostats that do not have a common termi-
nal, use a power robbing circuit in the off cycle to maintain
the batteries. This type of thermostat may interfere with the
operation of the ignition control and should not be used.
Direct Spark Ignition (DSI) Systems
Amana
®
brand PGA__C, PGB__C and PGD__C units built
after July, 1999, are equipped with a direct spark ignition
system. Ignition is provided by 20,000 volt electronic spark.
A flame sensor then monitors for the presence of flame and
closes the gas valve if flame is lost.
The system may be controlled by most good heating and
cooling thermostats with an adjustable heat anticipator. Some
night setback thermostats that do not have a common termi-
nal, use a power robbing circuit in the off cycle to maintain
the batteries. This type of thermostat may interfere with the
operation of the ignition control module and should not be
used.
HEATING SEQUENCE (Smart Valve and DSI Systems)
In order to illustrate the heating sequence, the following has
been simplified to give a better understanding of the pressure
switch operation.
Pressure Tap
Figure 8
Figure 8 is a view of the induced draft blower showing the
location of the pressure tap. The induced draft blower is
mounted on the collector box, the Heat Exchanger termi-
nates into the collector box.
The pressure tap has a predetermined orifice size for reading
static pressures. The induced draft blower motor assembly
is mounted to the collector box. When the motor is in opera-
tion, a negative pressure will be created on the pressure tap,
collector box and heat exchanger flue passages.
A pressure control using a single pole, single throw electrical
switch is used as a safety device in case of a blocked flue.