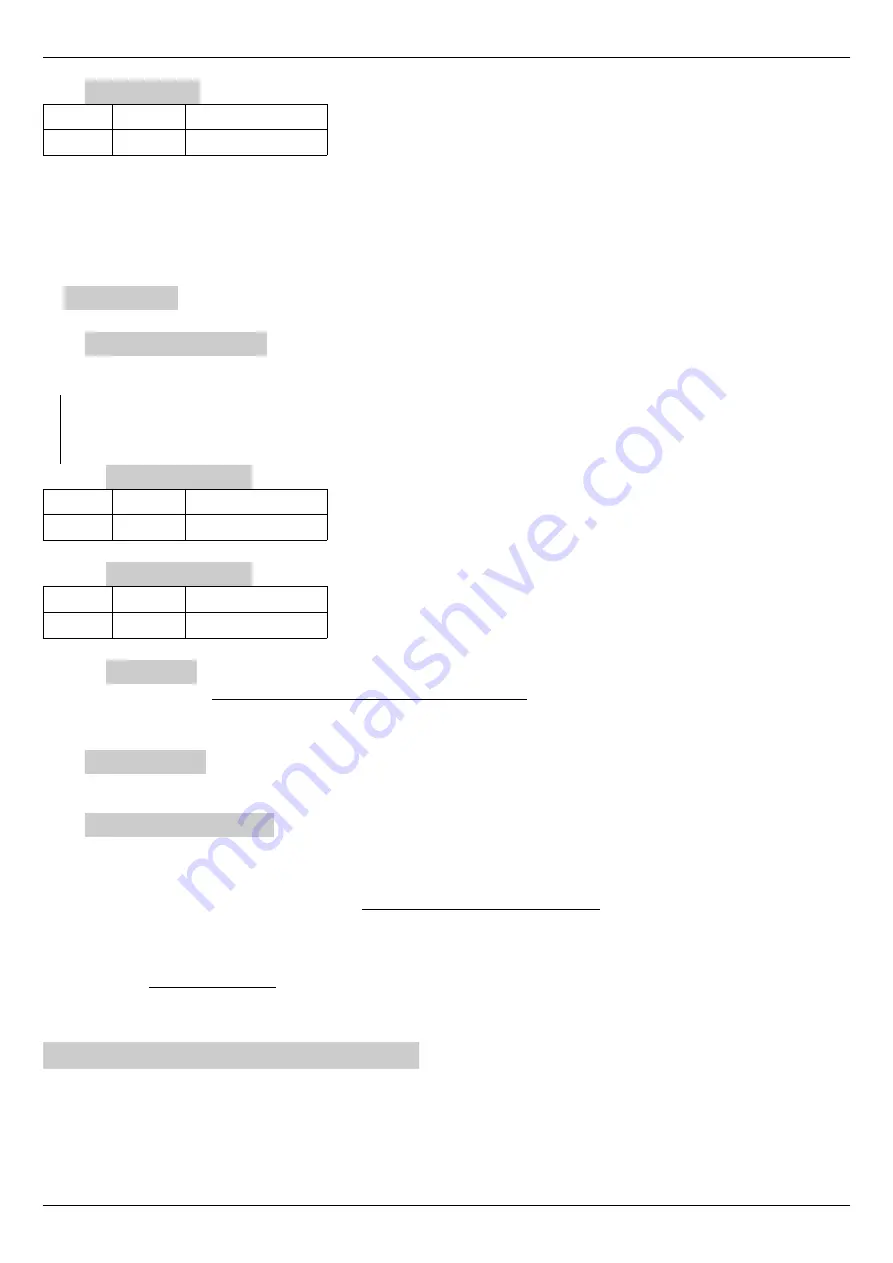
Instruction manual 91/121 V6.3
Commissioning
Integr. Gain
Minimum Maximum
Units of measure
0
99.00
-
This parameter modifies the Integrative time constant of the current loop (see drawing 21). The modification of this parameter is use-
ful in case of stop of the drive due to the “Overcurrent” alarm; in this case it means that the adjustment is too fast (or too slow) and the
current is not properly controlled by the above alarm. To enter the right parameter it is essential to use the PC connected to the serial
port of the drive and use the software to display the signals of the current loop while the motor is working and decide what to do.
It is recommended to change this parameter in small steps and test the motor reaction before further changes. When you have found
the right parameter that meets your needs, you can memorise the variations with the ”Memo Parameters“ menu (see page 40) and not
before; in this way it will always be possible to return to the previous situation.
Drive setup
Set of parameters to adjust or activate some particular functions in the drive that are rarely used.
Emulated encoder
Set of parameters to adjust the type of emulated encoder to be generated on the X4 and X5 connectors. The simulated encoder is only
available if you use a transducer connected to the X14 connector.
ATTENTION:
in case of use with a resolver connected to the X14 connector you will get the number of PPRs set for each “elec -
tric revolution” of the resolver and consequently a zero pulse (Z channel). This means that using a multipolar resolver (2 or more
polar pairs) you will get a zero pulse for each revolution of the motor equal to the number of polar pairs of the resolver. The same
situation is valid for the obtained PPRs that will be multiplied by the number of resolver pole pairs.
Encoder resol.
Minimum Maximum
Units of measure
8
8192
PPR
The selected number indicates the number of “pulse/turn” (ppr) of an encoder equivalent to tracks A, B and Z.
Position offset
Minimum Maximum
Units of measure
-180
+180
degrees
This parameter allows to offset the position of the simulated encoder with respect to the true position of the motor.
Direction
With this parameter you can reverse the count direction of the simulated encoder. The possible selections are as follows:
•
NORMAL: positive direction
•
REVERSE: negative direction.
Torque filter
In this menu you can activate or disable a special filter inserted after the speed loop that allows to reduce vibrations due to speed
transducers not perfectly calibrated and undulating in resolver transducers.
Power supply from
Menu to select the source of the power supply (
only for model PWM3D-001
). The selections available are:
•
DC+ DC-: The voltage is given directly on the DC+ and DC- terminals by an external power supply which must precharge
the capacitors on the DC Bus and check the voltage so as not to exceed the maximum accepted by the drive (750Vcc) using a
clamp circuit or an in-line recovery system. The internal clamp circuit is NOT used.
•
L1-L2-L3: The voltage is given on the terminals L1, L2, L3 and the internal rectifier bridge is used. The drive performs the
precharge of capacitors on the DC Bus when it receives the input voltage. When the voltage on the DC Bus exceeds a certain
threshold, the Clamp circuit enters into operation that inserts the braking resistance.
•
L1-L2: (Only for drive size 1). The single-phase voltage is given on the L1, L2 terminals and the internal rectifier bridge is
used. The drive performs the precharge of capacitors on the DC Bus when it receives the input voltage. When the voltage on
the DC Bus exceeds a certain threshold, the Clamp circuit enters into operation that inserts the braking resistance.
5.4 Calibration and adjustments
Operations to be carried out:
1. Give 230Vac service power supply on the X10 connector.
2. Check that the LCD display lights up and that the letters indicating the drive model and firmware revision appear, otherwise
check the correct service voltage.
3. Check that no red LEDs are on.
Alter Elettronica s.r.l.
53