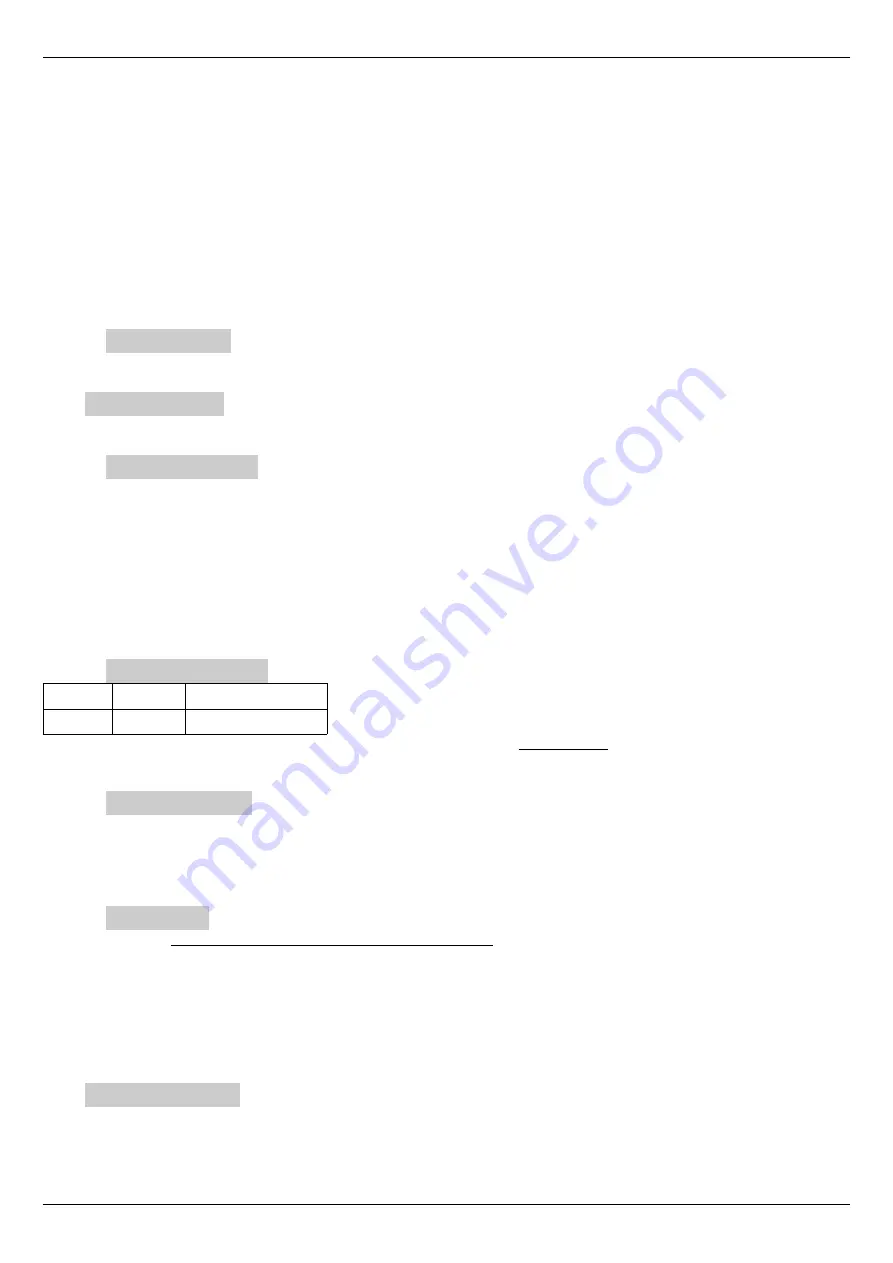
Commissioning
Instruction manual 91/121 V6.3
•
ANALOG INPUT 2
: The torque limit is taken from the analog input 2. The parameter “Value” for this analog input becomes
the source of the torque limiter block.
•
ASW1 Output
: The speed reference is taken from the exit of the Analog Switch 1 block (see section 5.6.11 on page 68).
•
ASW2 Output
: The speed reference is taken from the exit of the Analog Switch 2 block (see section 5.6.11 on page 68).
•
ASW3 Output
: The speed reference is taken from the exit of the Analog Switch 3 block (see section 5.6.11 on page 68).
•
ASW4 Output
: The speed reference is taken from the exit of the Analog Switch 4 block (see section 5.6.11 on page 68).
•
SumBlock Summ1
: The speed reference is taken from the “Summ1” output of the summing block (see paragraph 5.6.10 on
page 67).
•
SumBlock Summ2
: The speed reference is taken from the “Summ2” output of the summing block (see paragraph 5.6.10 on
page 67).
•
SumBlock Summ3
: The speed reference is taken from the “Summ3” output of the summing block (see paragraph 5.6.10 on
page 67).
Limit Output
This menu indicates the current torque limit value as a percentage of the motor maximum. When the maximum torque limitation func -
tion is deactivated, this parameter remains fixed at 100 %, otherwise it indicates the currently valid limit value.
Anti Backlash
Menu group with parameters to enable and adjust the anti backlash function with two drives (see section ”Anti-backlash system“ from
page 64).
AntiBack Mode
This menu is used to enable the “anti backlash” function and to select the drive mode: operation from “Master” motor or “Slave” mo -
tor. The possible selections are as follows:
•
DISABLED: The “anti-backlash” function is disabled and the drive normally works as a single motor.
•
MASTER 1: The “anti-backlash” function TYPE 1 is active and the drive works as a MASTER motor. All references and
commands coming from the CNC or PLC will be connected to this drive.
•
SLAVE: The “anti-backlash” function is active and the drive works as a SLAVE motor. Only signals from the motor trans-
ducer and the connection cable to the master drive must be connected to this drive.
•
MASTER 2: The “anti-backlash” function TYPE 2 is active and the drive works as a MASTER motor. All references and
commands coming from the CNC or PLC will be connected to this drive.
Contrast Torque
Minimum Maximum
Units of measure
0.0
+50.0
%
This menu appears only in the “Master” drive. The parameter is used to set the contrast
torque
in anti-backlash mode with a value pro-
portional to the maximum torque that can be delivered from the motor to the current speed. Normally a value between 5 and 30 % is
used.
Slave Running
This menu appears only in the “Master” drive. The parameter is used to enable or disable the operation of the motor “Slave” and you
can only change it when the master drive is disabled. Normally it is set to "Enabled" and automatically returns to this setting each time
you drop voltage to auxiliary services or when you switch the ”AntiBack Mode“ parameter (see page 48). The purpose of this para-
meter is to allow the master motor to run even when it is not mechanically connected to the slave motor, when you want to optimise
the adjustment loops.
Net Errors
This menu is used to disable the control of any short communication errors between master and slave. If the alarm “Anti backlash data
error” (see page 70) appears during operation the cause may be due to disturbances that are generated by unshielded cables or other
equipment nearby on the twisted double of the communication bus.
Disabling error control on the communication bus shall not affect the safety of operation: in fact, other controls are still active that
come into operation if the communication between master and slave is interrupted or that the data exchanged is not consistent within a
time of 1 ms.
If, despite the disabling of these controls, the alarm ”Anti backlash data error“ continues to appear, then it is necessary to make sure
that the disturbances are reduced.
Motor Overload
Menu group with parameters to enable and adjust the motor overload function. Refer to paragraph ”Motor Overload Function“ on
page 66 for more information.
48
Alter Elettronica s.r.l.