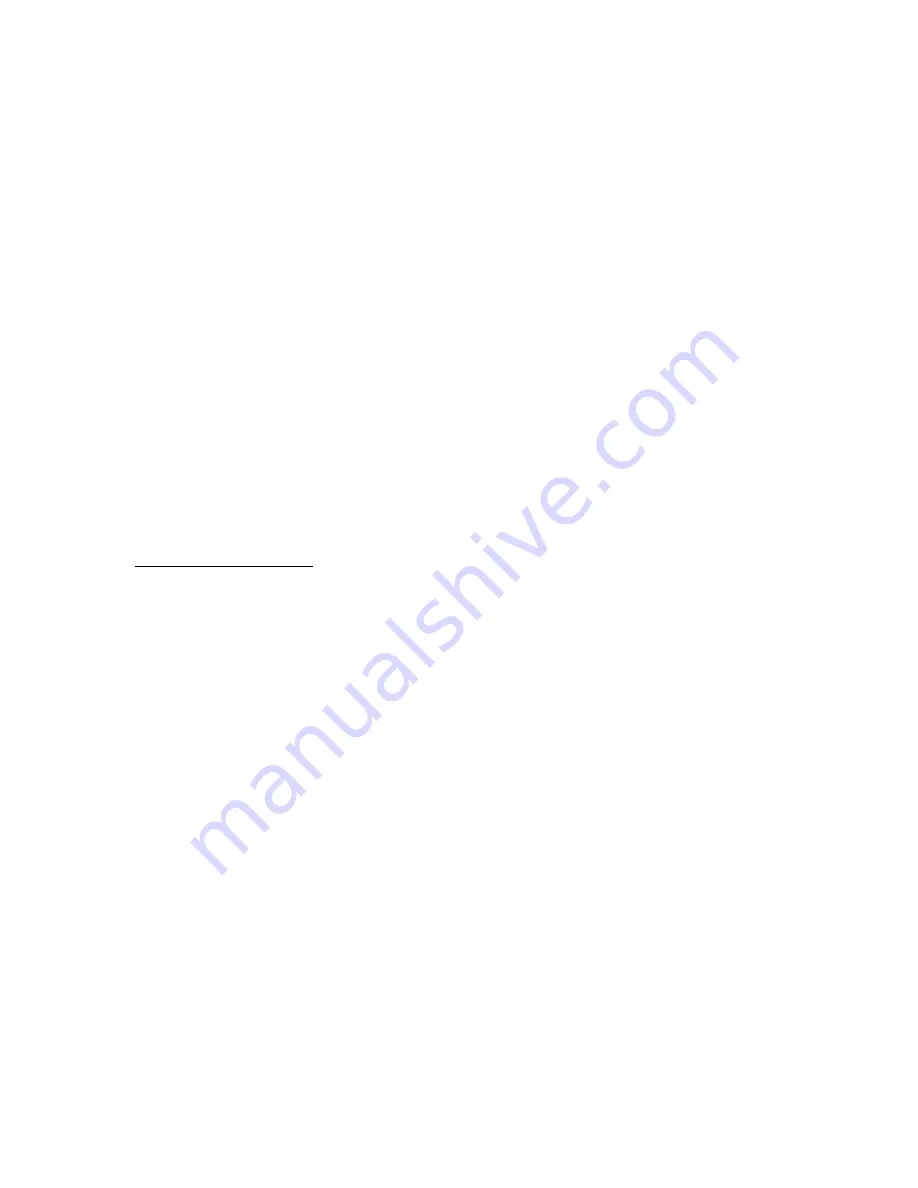
NOTE:
The Sensor must be more than one foot from the Electronics. The cable from the
sensor to the
electronics must not be altered in any way
.
6. Interconnect the units as shown in Fig. 3.7.
a. Connect the Sensor to the Compass Electronics using the cable exiting the lower
rear of the electronics housing.
CAUTION:
This cable may not be cut or extended
.
b. Connect the Compass Electronics to the Control Unit using AMS cable #CC30X0
(X0 denotes cable length in feet and are available in 10' increments to 90 feet). The
compass end is secured using two screws in the connector and must be fully seated for
reliable contact. The control unit end is connected as shown in Fig. 3.7.
CAUT ION:
This is 100% shielded cable and must not be extended.
7. Any auxiliary units may now be connected to the system according to the directions
supplied with them.
8.
Carefully check the installation and verify that all connections have been made
correctly.
SYSTEM TEST
1. Engage the Drive Link Latch using the Morse Control while rocking the wheel.
2. Set the Compass knob to agree with the ships heading.
3. Press POWER ON and rotate the Compass knob and verify that wheel follows the
Control with Helm corrections in the proper direction.
4. If the pilot Compass does not agree with the main ships Compass, rotate the Compass
Sensor in its bracket until correct or loosen the two set screws on the Compass knob
and rotate to agree.
5. If the pilot is equipped with a Remote Helm, select the Helm mode on the Remote
Helm and test its operation.
6. Set the compass calibration to MIN (refer to fig. 3.7) and sea-test the system with the
Yaw set to the mid-travel position. While sea testing, slowly turn the compass
calibration pot toward MAX. When the boat starts to "S", back the adjustment toward
MIN about 1/8 of a turn.
7. If required, install an optional Compass Compensator to reduce deviations per
standard practice.