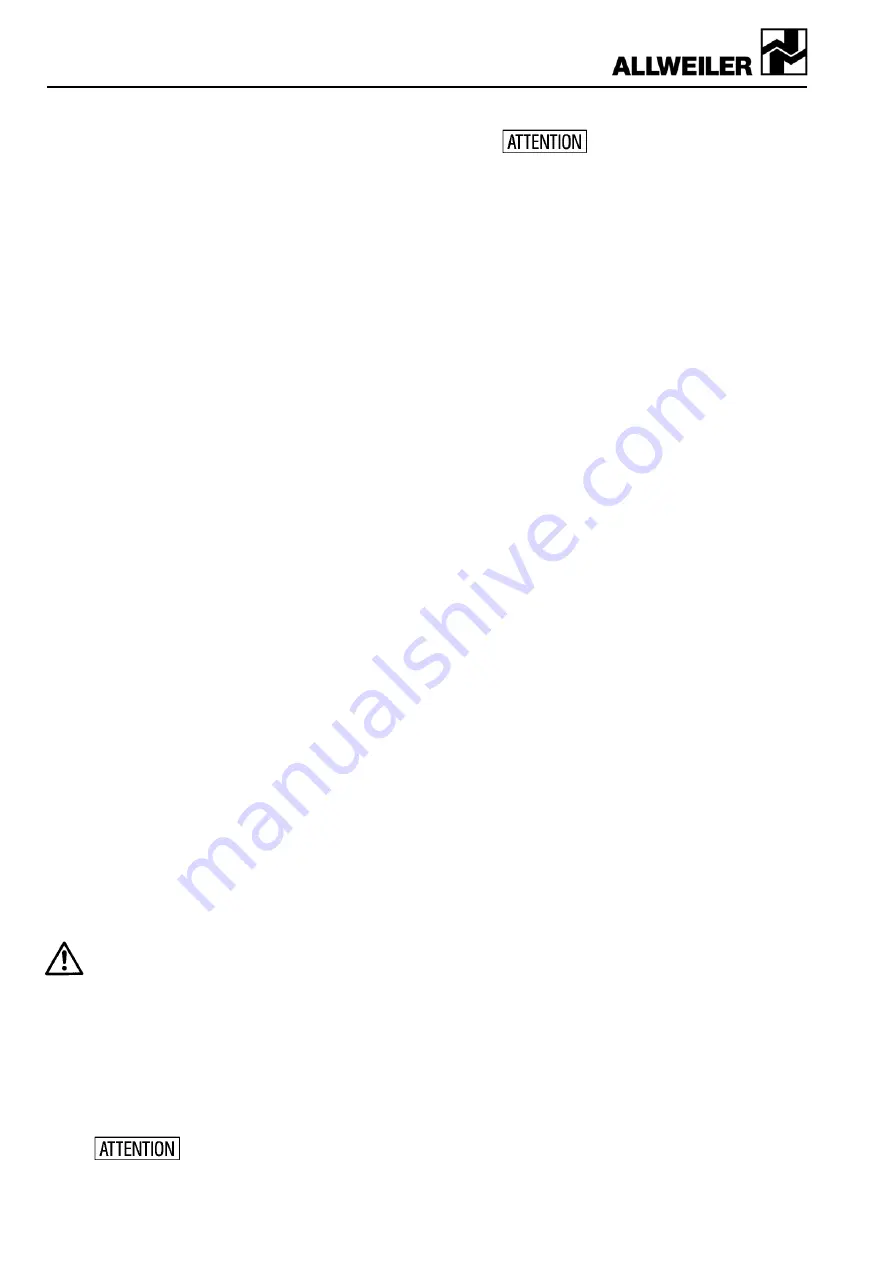
6
Series AE1L, AE.E, AE.N, AE.H, AE.V, AED1E, AED2N
Design ID, ZD
The set concrete foundations must be straight, even
and clean. Any traces of oil must be removed from
the foundations. The recessed anchor holes for the
foundation bolts must be cleaned and removed and
cleaned out with air. Prior to the installation of the
pump aggregate the surface of the concrete founda-
tions must be roughened and cleaned to ensure a
good bonding between the foundation block and the
mortar compound.
5.2.5
Pouring of base plate
After alignment on the concrete foundations , a low-
shrinkage mortar compound must be poured over the
entire length of the base plate, covering also the an-
chor holes with the connected foundation bolts.
Once the mortar compound has set on the base plate
and in the anchor holes, the foundation bolts must be
diagonally and evenly tightened.
Note:
When pouring or adding the mortar compound
it must be observed that the base plate makes full
contact. Tap the plate to ensure that no cavities have
formed underneath.
5.3
Base plate
The base plate must be fixed on the foundation, ten-
sion-free.
5.4
Coupling
A pump aggregate supplied complete was carefully
mounted at the factory. As the pump and the drive are
fixed on the base plate, re-alignment of the coupling is
not required.
5.5
Assembling of pump and drive
If the aggregate is first completed on site, you need to
assemble the clutch as follows:
1. Thinly coat the pump and drive shafts with molyb-
denum sulfite (e.g. Molykote) and insert the
feather keys.
2. Wind up the pump and the motor-side clutch half
with the aid of a windup device so far until the
shaft end is aligned with the clutch hub. If no
windup device is available, heating the clutch
halves to approx. 100°C (without rubber buffers)
eases sliding on.
3. Fixate the clutch halves axially with a grub screw
(DIN 916).
4. When assembling the pump and the motor, the
drive motor respectively variable speed gear,
make sure that the clutch halves are exactly
aligned and that the distance between the cou-
pling halves is observed (see our aggregate draw-
ings and the details by the clutch manufacturers).
5. Install a contact protection in acc. with DIN EN
809.
5.6
Drive by V-belt drive
In case of a V-belt reduction from drive to pump,
make sure that two V-belt pulleys are aligned in paral-
lel.
The V-belt pulleys must be pushed onto the shaft
ends as far as possible. It must be possible to regu-
late the tension of the V-belts by means of a motor
rocker or by means of tensioning rails. They must be
slightly retightened after a short running-in period.
Excessive tensioning will destroy
the rolling bearings of the pump.
Our separate instructions “V-belt drive” (VM 706.0001
GB, Ident No. 133586) must be complied with.
5.7
Space required for maintenance and servicing
The pump must be accessible from
all sides in order to be able to per-
form the required sight inspections.
There must be enough room for maintenance and
service work, especially for the exchange of the con-
veyor elements. The stator and rotor dismounting di-
mensions are listed in the pump respectively pump
aggregate dimension sheet. Also make sure that all
pipelines can be attached/detached without obsta-
cles.
5.8
Installing of pipelines
5.8.1 Nominal
widths
The nominal widths of the suction and pressure pipes
should be designed according to the nominal widths
of the pipe connections. Gross deviations, especially
on the suction side, require consultation with the fac-
tory.
5.8.2
Supports and flange connections
The pipelines must be connected tension-free to the
pump via the flange connectors. They have to be
supported near the pipe and should be easy to screw
on in order to avoid strains. After loosening the
screws, the flanges may neither be slanted nor
springy and also not rest on each other under pres-
sure. Possible thermal stress on the pipelines has to
be kept away from the pump by means of suitable
measures, e.g. the installation of compensators.
5.8.3 Cleaning
of
pipelines prior to attachment
The pipelines, sliders and valves on the suction side
must be rinsed respectively cleaned under all circum-
stances before installing the pump.
Leftover assembly parts like screws, nuts, welding
beads, pieces of steel, etc. destroy the inside parts of
the pump. Any warranty claim is void when damages
are caused by such leftover materials. Flange seals
may not protrude to the inside. Blind flanges, stoppers
protective foils and/or lacquers on flanges and sealing
strips have to be completely removed.
5.9
Installing of auxiliary pipelines for additional fa-
cilities
All auxiliary pipelines for supplying the shaft seal and
the possible double jacket casing for heating and
cooling the pump have to be connected tension-free
and sealing.
The pipes for the quenching liquid with single-acting
mechanical seals with quench (design: G0Q and
G1Q) and the sealing liquid with double-acting me-
chanical seal (design: G0D/G1D) should be installed
with a large flowtrough profile. The quenching respec-
tively sealing liquid discharge takes place at the high-
est connection of the mechanical seal housing.
The flow direction of the flushing, sealing and quench-
ing liquid is indicated with arrows in the section draw-
ings.
In order to ensure self-deairing, the pipes must be in-
stalled continuously rising, short and favorable for the
flow.
The formation of air pockets and gas bubbles has to
be prevented, install deairing connections if required.
The heating/cooling liquid discharge must be con-
nected to the highest connection of the possible dou-
ble-jacket casing.