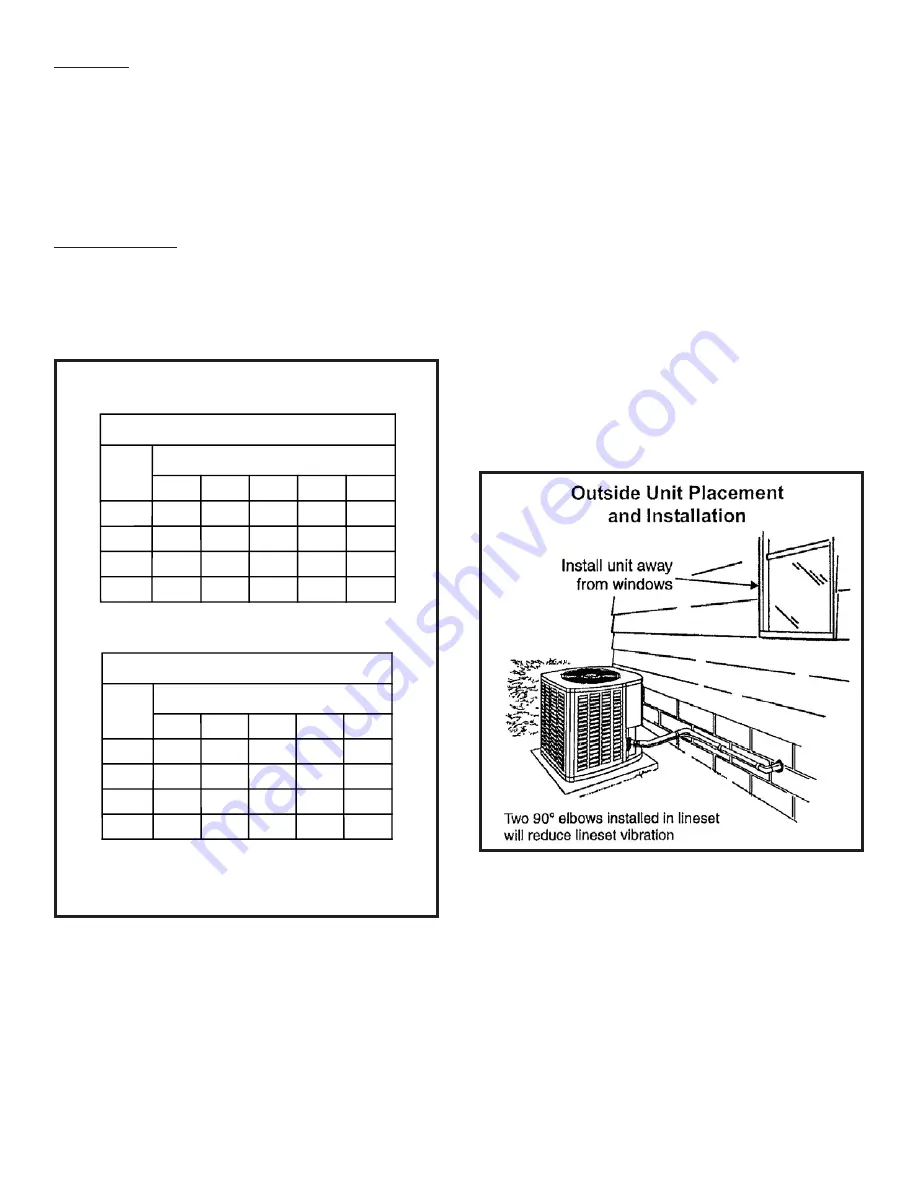
Placement
Be aware that some localities are adopting sound ordinances
based on how noisy the unit is at the neighbor’s home, not
at the original installation. Install the unit as far as possible
from the property line. When possible, do not install the unit
directly outside a bedroom window. Glass has a verry high
level of sound transmission. Figure 5 on page 5 shows how
to place the outdoor unit and line set to reduce line set
vibration.
Line Set Isolation
Illustrations on the pages 6 and 7 demonstrate procedures
which ensure proper refrigerant line set isolation. Figure 6
shows how to install line sets on horizontal runs. Figure 7
shows how to make a transition from horizontal to vertical.
Figure 9 shows how to install line sets on vertical runs.
Brazing Connection Procedure
1. Cut ends of refrigerant lines square (free from nicks or
dents). Debur the ends. The pipe must remain round; do
not pinch end of line.
2. Before making line set connections, use dry nitrogen to
purge the refrigerant piping. This will help to prevent
oxidation and the introduction of moisture into the system.
3. Use silver alloy brazing rods (5% or 6% silver alloy for
copper-to-copper brazing or 45% silver alloy for copper-to-
brass or copper-to-steel brazing) which are rated for use
with R410A refrigerant.
4. Remove the Schrader core assemblies before brazing to
protect them from damage due to extreme heat. Replace
the cores when brazing is complete.
5. Remove light maroon washers from service valves and
shield light maroon stickers to protect them during brazing.
Wrap a wet cloth around the valve body and copper tube
stub to protect it from heat damage.
Figure 5
506254-01
Page 5 of 25
Issue 0912
Table 2
Refrigerant Line Set Diameters (in.)
For installations exceeding 50’, contact
Technical Services.
Liquid Line
BTUH
Line Set Length and Size
12 ft.
25 ft.
50 ft.
75 ft. 10 0 ft.
3/8
3/8
3/8
3/8
3/8
24,000
3/8
3/8
3/8
3/8
3/8
3/8
3/8
1/2
36,000
3/8
3/8
3/8
1/2
48,000
60,000
1/2
1/2
1/2
Suction Line
BTUH
Line Set Length and Size
12 ft.
25 ft.
50 ft.
75 ft. 100 ft.
3/4
3/4
24,000
7/8
36,000
7/8
7/8
7/8
1-1/8
7/8
7/8
1-1/8
48,000
7/8
7/8
7/8
1-1/8
1-1/8
60,000
1/8
1/8
1-1/8
1-1/8
7/8
Содержание 4SCU18LT Series
Страница 7: ...Figure 7 Figure 8 506254 01 Page 7 of 25 Issue 0912 ...
Страница 18: ...Table 9 Flash Codes 506254 01 Page 18 of 25 Issue 0912 ...
Страница 19: ...Table 10 Flash Codes cont 506254 01 Page 19 of 25 Issue 0912 ...
Страница 20: ...Table 11 Miswired Module Troubleshooting 506254 01 Page 20 of 25 Issue 0912 ...
Страница 23: ...506254 01 Page 23 of 25 Issue 0912 WIRE DIAGRAM ...