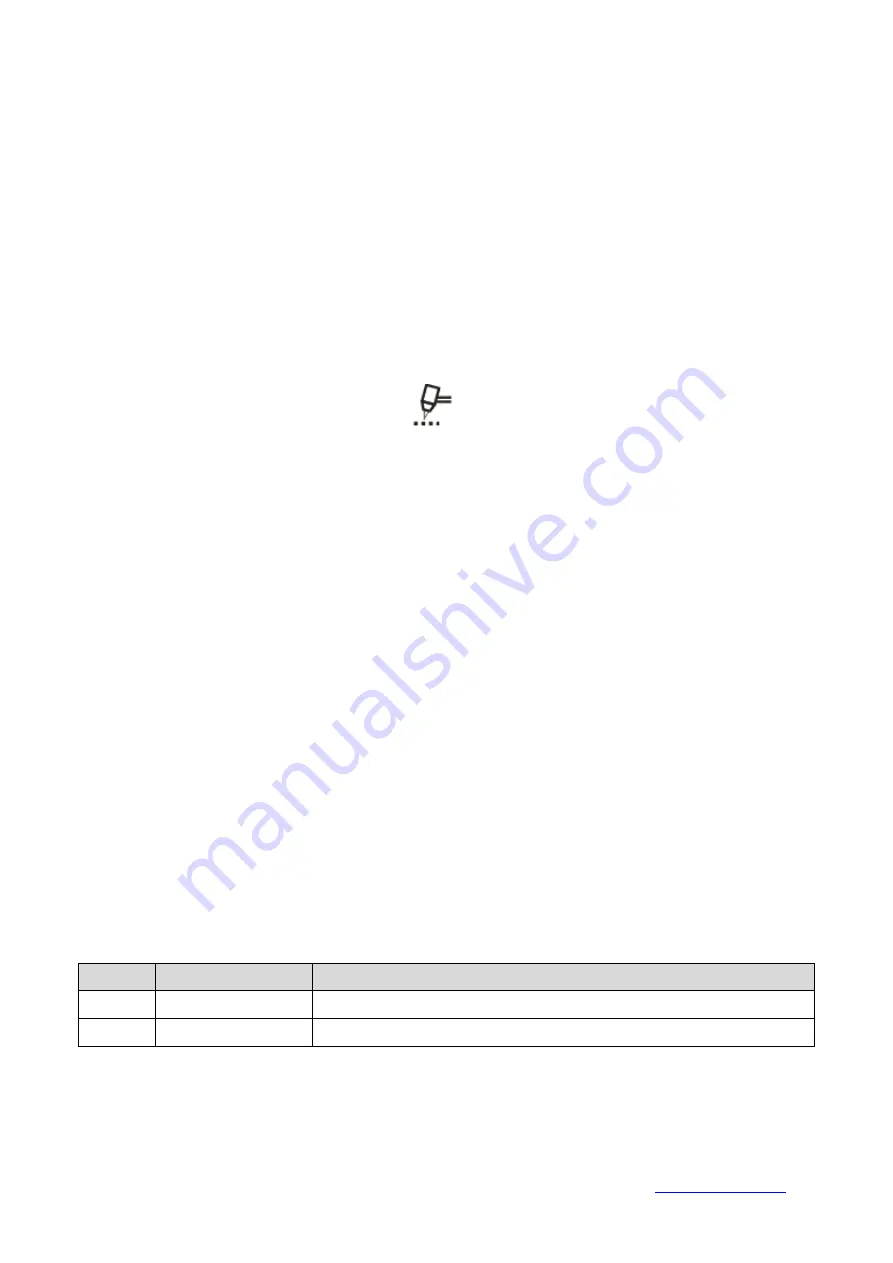
16/22
ALFA IN a.s ©
www.alfain.eu
3
connector
A1
.
10. Check up the input air pressure (min. 5,0 bar, max. 8,5 bar) and make a
regulation if necessary.
11. Set potentiometer
A4
to the cutting power you need.
12.
Fit the torch with appropriate type of cutting tip electrode and shield cup
according to the selected cutting current.
13.
Press the trigger on the cutting torch, the pre gas will flow for 1 s.
14.
The pilot arc will start.
15.
Shift the torch with the pilot arc close to the material, the pilot arc will
change to cutting arc automatically. If you do not start cutting within 2 s,
the arc will snuff off. If the torch delays during the cutting from the material,
the arc will snuff off. In case that the machine is in mode Cutting material
with gaps – switch
A11
position
, cutting arc will change to pilot arc and
if you
do not start cutting within 2 s, this arc will snuff off.
16.
To finish the cutting process, release the torch trigger.
REQUIREMENTS FOR SOURCE OF COMPRESSED AIR
1. Delivered air pressure must be max. 8,5 bar and min. 5,0 bar.
2. Work pressure must be during the cutting in range 5,0 – 6,0 bars. We
recommend to achieve of maximal cutting power one thing, the pressure
cannot fall under 5,5 bars.
3. Air consumption minimal 320 l/min.
4.
Compressed air for the plasma must be clean and dry.
5.
Pressure dew point +3 °C.
6.
Maximum oil content 0.1 mg/m
3
.
7.
Maximal size of solid particles 15 microns.
8.
The minimal size of an air tank is 100 l.
9.
No additional oiling if the pressure air is permitted. That could damage the
plasma machine and the cutting torch.
OPTIONAL AIR FILTERS
To achieve high quality cutting and to avoid serious disturbances to the torch it
is highly advised to include the air filter.
Pos. Item No
Description
24
5302
Air filter AT 1000
25
5304
Set for filter AT 1000 to PEGAS Plasma
NOTE
Max. allowable pressure of filter AT 1000 is 8,5 bar