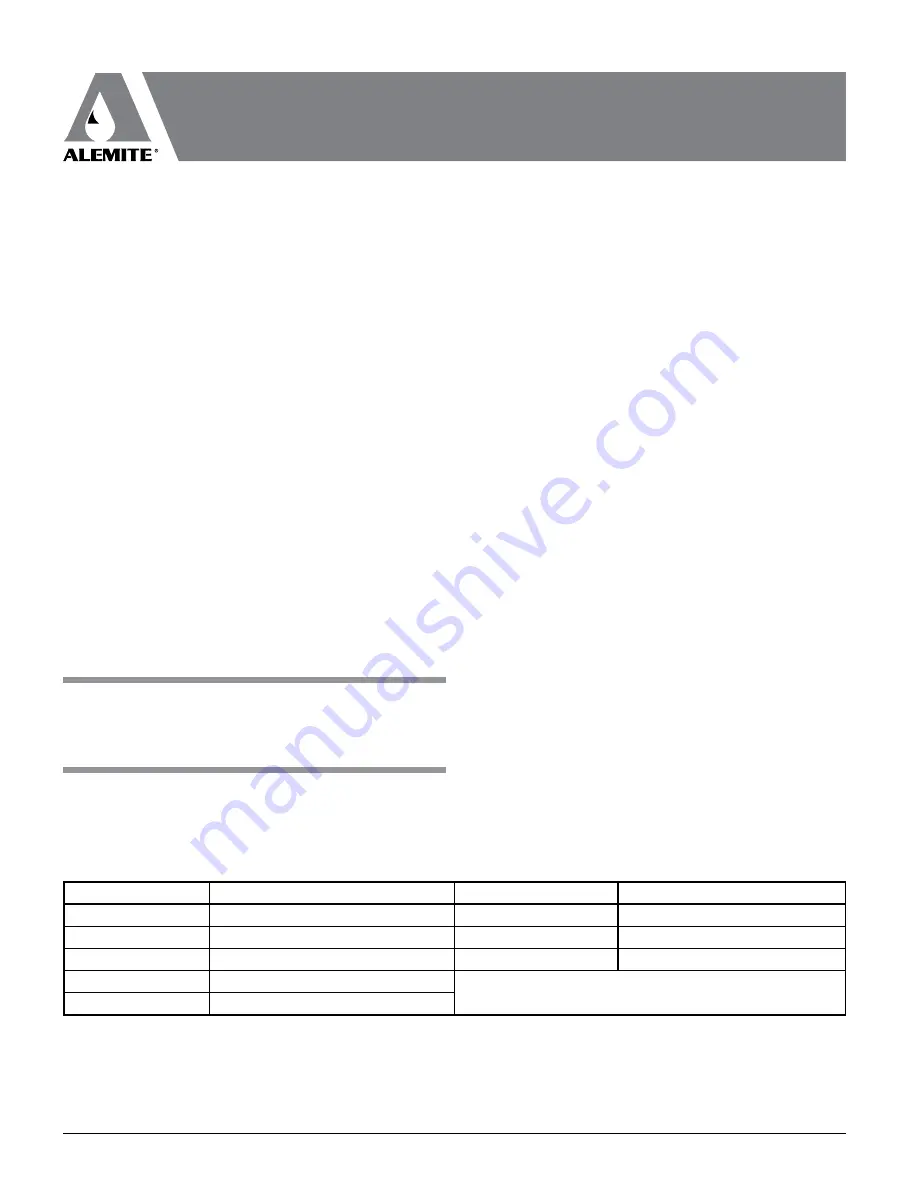
High pressure grease pump
SER 7795-A5
Revision (2-18)
8
Alemite, LLC
Important: should the pump contain the obsolete piston
(
see figure 5
), and stall properly, certain parts within the
major repair kit are discarded. If the new piston is required,
order barrel assembly (
28
) and piston (
33
) separately.
20. Remove lower spring clip
(24)
that secures piston
(33)
to lower
coupling
(23)
.
21. Unscrew the coupling from the piston.
22. Remove barrel assembly
(29)
from the piston.
23. Remove both aluminum gaskets
(27)
.
24. Remove brass bearing
(31)
, seal
(30)
, and nylon wear ring
(29)
from the barrel.
25. Unscrew primer body
(50)
from adapter
(41)
.
26. Remove the primer rod (with attached components) from the
bottom of the adapter.
27. Remove spacer
(32)
from top of adapter.
28. Remove stop nut
(49)
from primer rod
(40)
.
•
Support the primer rod through the hole as needed.
29. Remove plate
(48)
, gasket
(27)
, valve seat
(47)
, and additional
gasket
(27)
from the primer rod assembly.
CAUTION
Support the piston and primer rod assembly during roll pin
(39)
removal. Damage to components can occur.
30. Remove roll pin
(39)
that secures adapter and insert assembly
(38)
to primer rod
(40)
.
•
Use a punch and a small hammer.
31. Unscrew primer rod from adapter.
32. Remove valve body
(46)
[with attached components] and
guide washer
(42)
from the upper end of the primer rod as-
sembly.
33. Remove screw
(43)
, nylon washer
(44)
, seal
(45)
and additional
washer
(44)
from the valve body.
34. Unscrew the adapter from piston
(33)
.
35. Remove aluminum washer
(37)
, ball
(36)
, spring
(35)
, and
retainer
(34)
from the piston.
Clean and inspect*
Note: use the appropriate repair kit for replacement parts. Make
sure all the components are included in the kit before discarding
used parts.
1. Clean all metal parts in a modified petroleum-based solvent.
The solvent should be environmentally safe.
2. Inspect all parts for wear and/or damage.
•
Replace as necessary.
3. Inspect piston
(33)
and primer rod
(40)
closely. Use a magnify-
ing glass to detect any score marks.
•
Replace as necessary.
4. Closely inspect the mating surfaces of all check valve compo-
nents for any imperfections ensure a smooth and clean contact
is obtained when assembled.
Item no. on
Figure 2-A
Description
Item number on
Figure 2B
Description
9
O-Ring, 1-13/16 in ID x 2 in OD
29
Ring, Wear (Glass-Reinforced Nylon)
10
O-Ring, 1-15/16 in ID x 2-1/8 in OD
30
Seal, 1.00 in ID x 1.375 in OD
13
O-Ring, 1-3/16 in ID x 1-5/16 in OD
45
Seal, 0.50 in ID x 0.950 in OD
15
Seal, 0.812 in ID x 1.062 in OD
17
Seal, 0.812 in ID x 1.562 in OD
Table 4
Components Lubricated in Clean Oil
* Indicates change