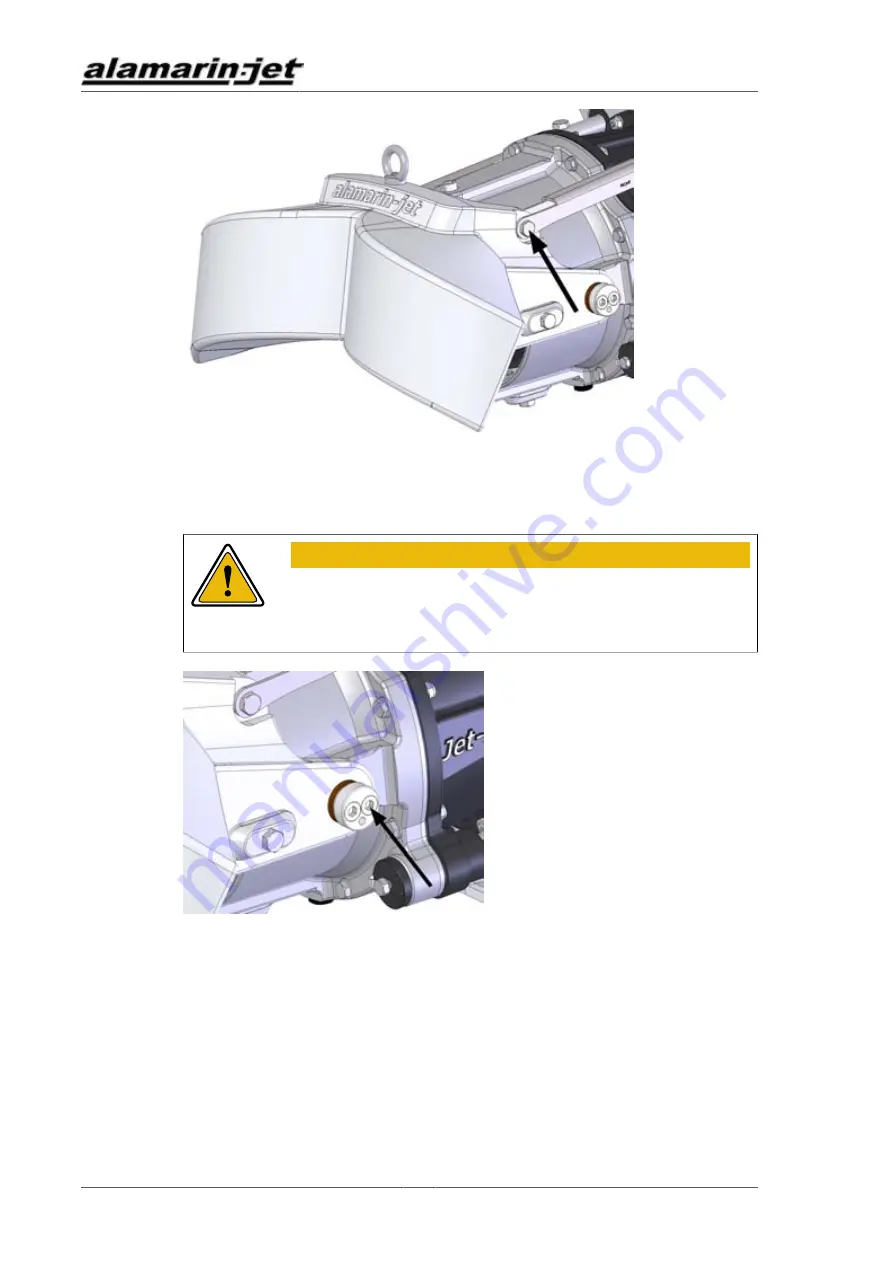
Reversing deflector and operating hydraulics
Repair manual
40
KM/285/EN/1.1.0
Figure 52. Removing the reversing deflector
2. Open the joint pin screws (2 pcs, figure 53).
WARNING!
Be careful not to drop the deflector.
The deflector weighs approximately 16 kg.
Figure 53. Joint pin screws
3. If you need to replace the plastic bearings on the joint pins, they can be
removed with a suitable mandrel.
The plastic bearings are pushed to their place and can be removed by
Содержание AJ 285
Страница 1: ...Repair manual ...
Страница 2: ......
Страница 30: ...Main shaft and bearing Repair manual 26 KM 285 EN 1 1 0 ...
Страница 42: ...Impeller Repair manual 38 KM 285 EN 1 1 0 ...
Страница 78: ...Tightening torques Repair manual 74 KM 285 EN 1 1 0 ...