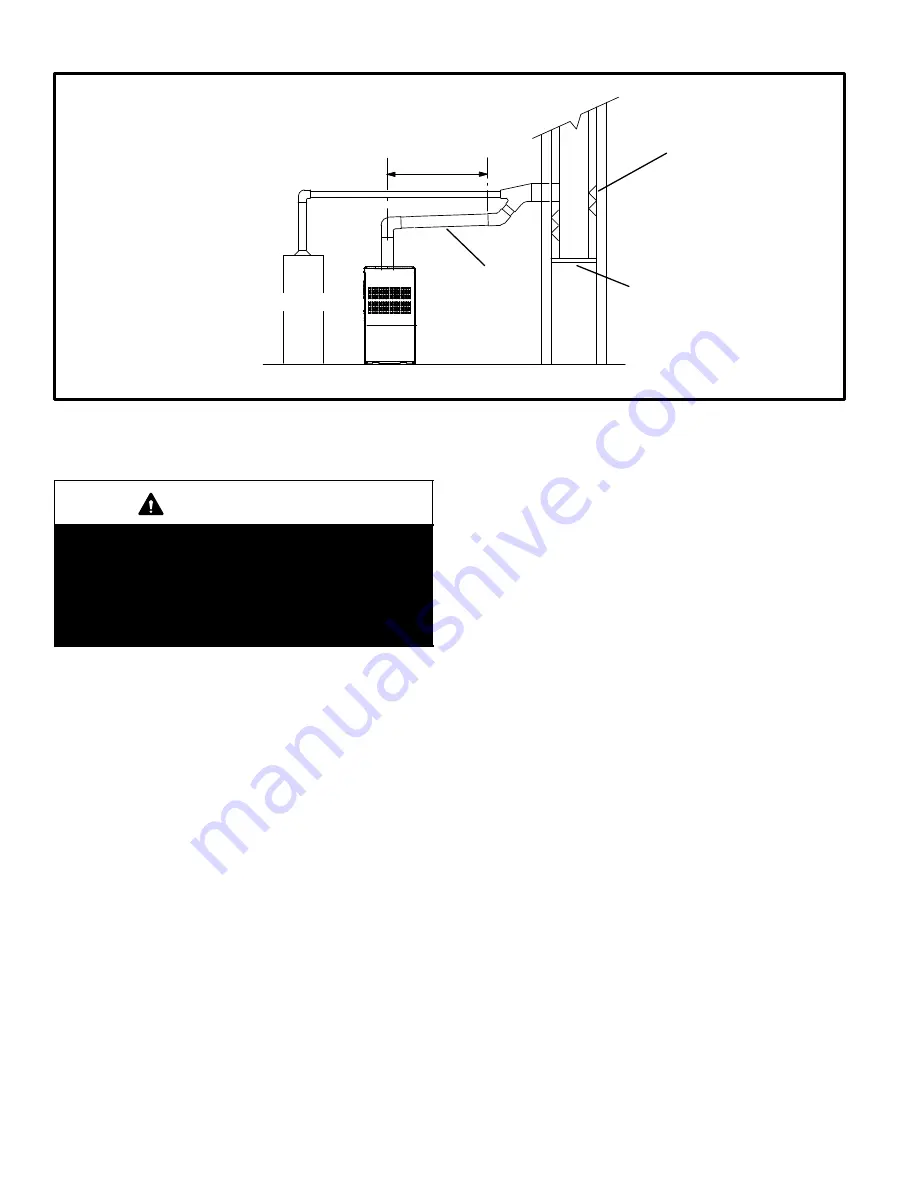
Page 14
FIGURE 17
Common Venting Using Tile−Lined Interior Masonry Chimney and Combined Vent Connector
MINIMUM LENGTH = AS SHORT AS PRACTICAL.
FOR MAXIMUM LENGTH SEE NOTE TO LEFT
INTERIOR TILE−LINED
MASONRY CHIMNEY
NOTE − the chimney must be properly
sized per provided venting tables or
lined with listed metal lining system.
PERMANENTLY
SEALED FIREPLACE
OPENING
VENT
CONNECTOR
NOTE− Refer to provided venting
tables for installations.
FURNACE
OTHER
APPLIANCE
DO NOT insulate the space between the liner and the
chimney wall with puffed mica or any other loose gran-
ular insulating material.
IMPORTANT
SINGLE appliance venting of a fan-assisted furnace
into a tile-lined masonry chimney (interior or outside
wall) is PROHIBITED. The chimney must first be lined
with either type B1 vent or an insulated single wall
flexible vent lining system which has been sized ac-
cording to the provided venting tables and the vent
pipe manufacturer’s instructions.
A fan−assisted furnace may be commonly vented into an
existing lined masonry chimney if the following conditions
are met:
S
The chimney is currently serving at least one drafthood−
equipped appliance;
S
The vent connectors and chimney are sized according
to the provided venting tables.
If type B1 double-wall vent is used inside a chimney, no oth-
er appliance can be vented into the chimney. The outer wall
of type B1 vent pipe must not be exposed to flue products.
A type B1 vent or masonry chimney liner shall terminate
above the roof surface with a listed cap or a listed roof as-
sembly according to the terms of their respective listings
and the vent manufacturer’s instructions.
When inspection reveals that an existing chimney is not
safe for the intended purpose, it shall be rebuilt to conform
to nationally recognized standards, lined or relined with
suitable materials, or replaced with a gas vent or chimney
suitable for venting 80AF1DF series units. The chimney
passageway must be checked periodically to ensure that it
is clear and free of obstructions.
Do not install a manual damper, barometric draft regulator,
or flue restrictor between the furnace and the chimney.
Never connect a Category I appliance to a chimney that is
servicing a solid−fuel appliance. If a fireplace chimney flue
is used to vent this appliance, the fireplace opening must
be permanently sealed.
A type B or listed chimney lining system that passes
through an unused masonry chimney flue is not considered
to be exposed to the outdoors.
General Venting Requirements
Vent all 80AF1DF furnaces according to these instructions:
1 − Vent diameter recommendations and maximum allow-
able piping runs are found in the provided venting
tables.
2 − In no case should the vent or vent connector diameter
be less than the diameter specified in the provided
venting tables.
3 − The minimum vent capacity determined by the sizing
tables must be less than the low fire input rating and the
maximum vent capacity must be greater than the high
fire input rating.
4 −
Single appliance vents −
If the vertical vent or tile-lined
chimney has a larger diameter or flow area than the
vent connector, use the
vertical vent diameter
to de-
termine the
minimum vent capacity
and the
vent
connector diameter
to determine the
maximum vent
capacity
. The flow area of the vertical vent, however,
shall not exceed 7 times the flow area of the listed ap-
pliance categorized vent area, drafthood outlet area or
flue collar area unless designed according to approved
engineering methods.
5 −
Multiple appliance vents −
The flow area of the largest
section of vertical vent or chimney shall not exceed 7
times the smallest listed appliance categorized vent
area, drafthood outlet area or flue collar area unless de-
signed according to approved engineering methods.