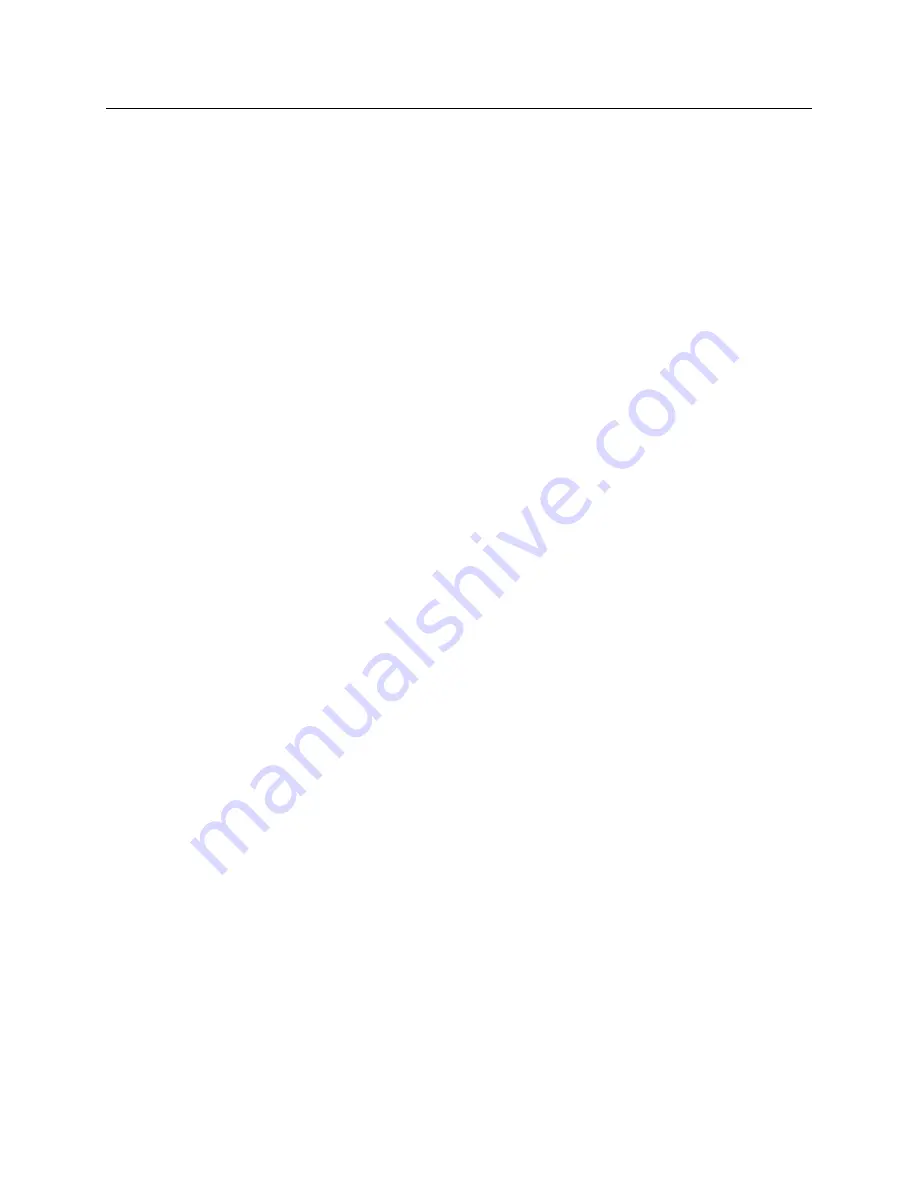
6
Table of Contents
Warranty Information
2
Safety Summary
3
Notice
4
Printing History
5
Instrument Identification
5
Table of Contents
6
INTRODUCTION
9
Organization
9
Safety Considerations
9
Related Documents
9
Revisions
10
Manual Revisions
10
Firmware Revisions
10
Electrostatic Discharge
10
VERIFICATION AND PERFORMANCE TESTS
11
Introduction
11
Test Equipment Required
11
Measurement Techniques
12
Setup for Most Tests
12
Electronic Load
13
Current-Monitoring Resistor
14
Operation Verification Tests
14
Performance Tests
14
Programming
14
Constant Voltage (CV) Tests
15
CV Setup
15
Voltage Programming and Readback Accuracy
15
CV Load Effect
15
CV Source Effect
16
CV Noise (PARD)
16
Transient Recovery Time
16
Constant Current (CC) Tests
17
CC Setup
17
Current Programming and Readback Accuracy
17
Current Sink (CC-) Operation
18
CC Load and Line Regulation
18
CC Load Effect
19
CC Source Effect
20
CC Noise (PARD)
20
Performance Test Equipment Form
21
Performance Test Record Form
22
TROUBLESHOOTING
27
Introduction
27
Test Equipment Required
28
Overall Troubleshooting
28
Flow Charts
28
Specific Troubleshooting Procedures
33
Power-on Self-test Failures
33
Содержание 6611C
Страница 8: ......
Страница 26: ......
Страница 48: ......
Страница 51: ...Replaceable Parts List 5 51 Figure 5 1 Mechanical Parts Identification ...
Страница 54: ...6 Diagrams 54 Figure 6 2 A1 Board Block Diagram ...
Страница 55: ...Diagrams 6 55 Figure 6 3 A2 A3 Boards Block Diagram ...