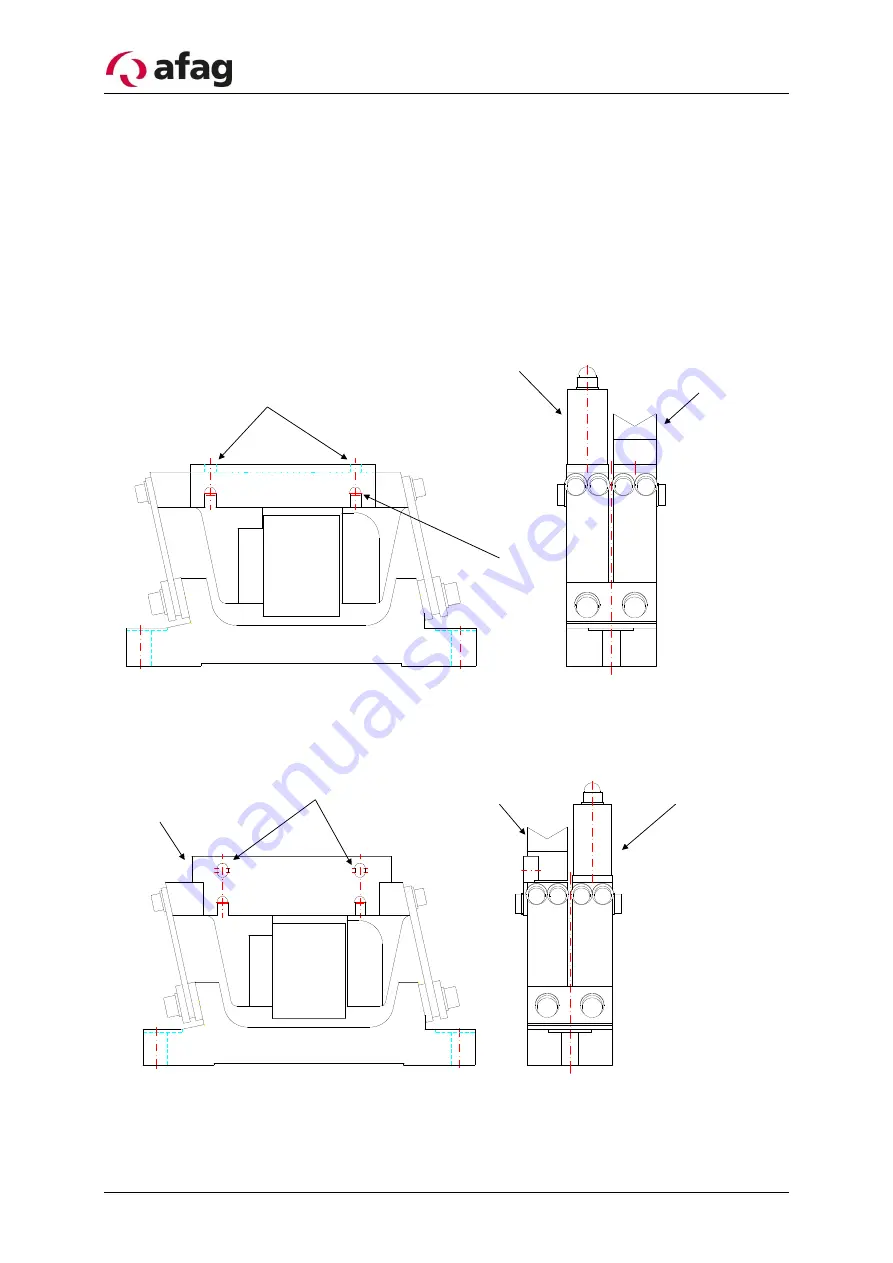
Page 12
20/01/2020
R06.1
3.3
Mounting of the linear track
3.3.1
Attaching one linear track
The linear track is attached to either vibrating section with the help of an angle bracket or
a lateral plate
. In the case of the KLF5, the linear track is attached
directly to the vibrating section
(see chapter 2.3 Figure 1)
. In any case, make sure to observe
the correct attachment position as per chapter 2.3 Figure 1 and
Fehler! Verweisquelle
konnte nicht gefunden werden.
. Any deviations may adversely affect floor vibration.
Figure 4:
Linear track mounted with angle bracket
Figure 5:
Linear track mounted with lateral plate
Fixing bores for
linear track
Trimming
weight
Left linear track
Lateral plate
Fixing bores for linear
track/trimming weight
Angle
bracket
Trimming weight
Right linear
rack