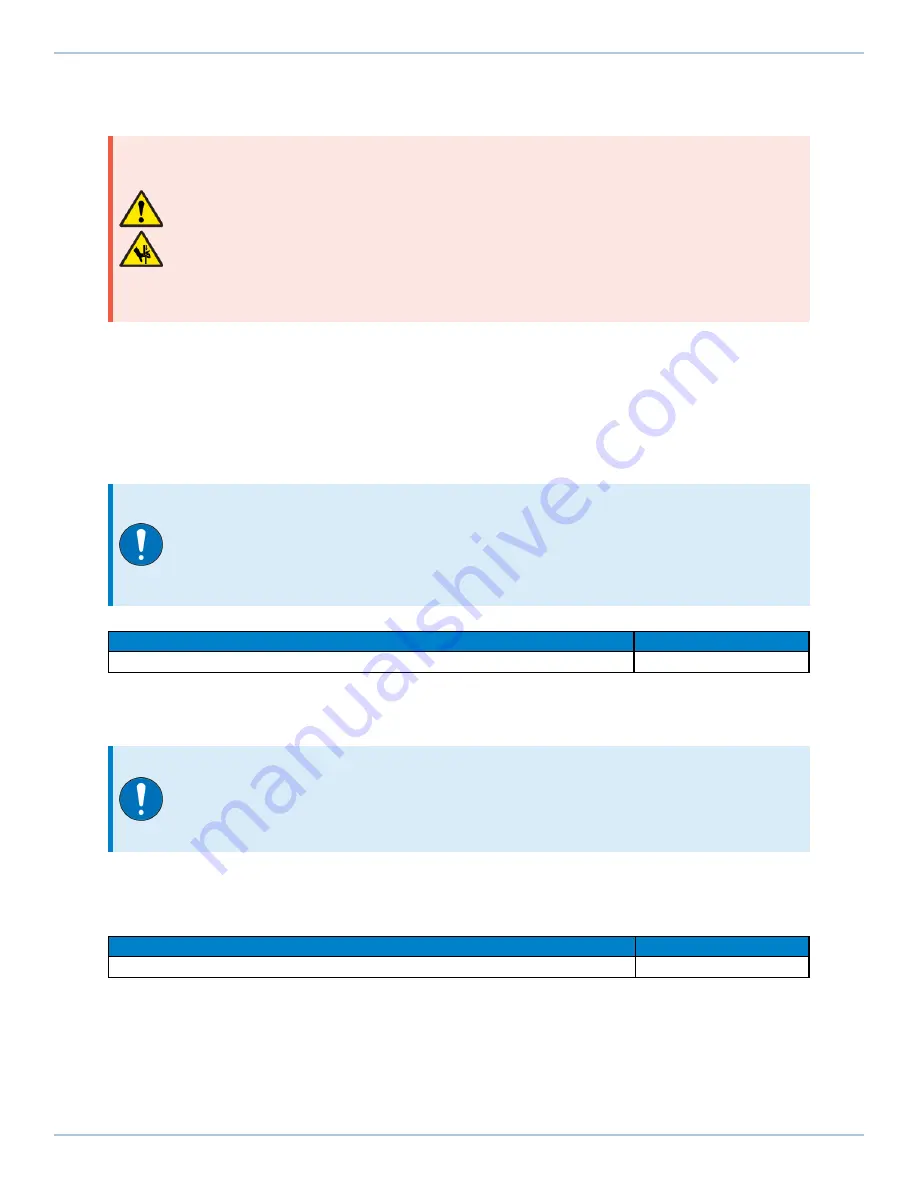
2.2. Securing the Stage to the Mounting Surface
DANGER: Mechanical Hazard!
Personnel must be made aware of the mechanical hazards during set up or when you
do service to the stage.
l
Do not manually move the stage if it is connected to a power source.
l
The stage must be mounted securely. Improper mounting can result in injury and
damage to the equipment.
l
When you move the tabletop manually to do maintenance, this could expose the
operator to pinch points. Refer to
on
The mounting surface must be flat and have adequate stiffness to achieve the maximum
performance from the stage. When it is mounted to a non-flat surface, the stage can be distorted
while the mounting screws are tightened. This distortion will decrease overall accuracy. Adjustments
to the mounting surface must be done before the stage is secured.
Inspect the mounting surface for dirt or unwanted residue and clean if necessary. Use precision
flatstones on the mounting surface to remove any burrs or high spots. Clean the mounting surface
with a lint-free cloth and acetone or isopropyl alcohol and allow the cleaning solvent to completely
dry. Gently place the stage on the mounting surface.
IMPORTANT
: The stage is precision machined and verified for flatness prior to product
assembly at the factory. If machining is required to achieve the desired flatness, it
should be performed on the mounting surface rather than the stage. Shimming should
be avoided if possible. If shimming is required, it should be minimized to retain
maximum rigidity of the system.
Table 2-1:
Stage Mounting Surface Flatness Requirement
Stage Travel
Flatness Requirement
All Travels
7.5 µm
If necessary, manually move the stage table to access the mounting holes along the edges of the
stage. This stage is designed to use socket head cap screws (SHCS) to secure the base to the
mounting surface.
IMPORTANT
: The stage table may offer a considerable amount of resistance when it is
moved manually.
l
Do not attempt to manually move the stage if it is connected to a power source or
includes an integrated brake.
Tightening torque values for the mounting hardware are dependent on the properties of the surface
to which the stage is being mounted. Values provided in
are typical values and may not be
accurate for your mounting surface. Refer to
for mounting locations and dimensions.
Table 2-2:
Stage to Mounting Surface Hardware
Mounting Hardware
Typical Screw Torque
M6 x 22 mm (or 1/4" x 7/8") SHCS with flat washers
7 N·m [5 ft·lb]
2.2. Securing the Stage to the Mounting Surface
ECO165SL Hardware Manual
24
www.aerotech.com
Содержание ECO165SL Series
Страница 1: ...Revision 2 01 ECO165SL Series Mechanical Bearing Ball Screw Stage HARDWARE MANUAL...
Страница 14: ...This page intentionally left blank Handling and Storage ECO165SL Hardware Manual 14 www aerotech com...
Страница 22: ...Figure 2 2 Tabletop Accessory Dimensions TT3 Option 2 1 Dimensions ECO165SL Hardware Manual 22 www aerotech com...
Страница 23: ...Figure 2 3 Z Axis Bracket Dimensions ECO165SL Hardware Manual 2 1 Dimensions www aerotech com 23...
Страница 46: ...Figure 4 1 Hardcover Screw Removal 4 2 Cleaning and Lubrication ECO165SL Hardware Manual 46 www aerotech com...
Страница 47: ...Figure 4 2 Hardcover Removal ECO165SL Hardware Manual 4 2 Cleaning and Lubrication www aerotech com 47...
Страница 58: ...This page intentionally left blank Appendix B Revision History ECO165SL Hardware Manual 58 www aerotech com...