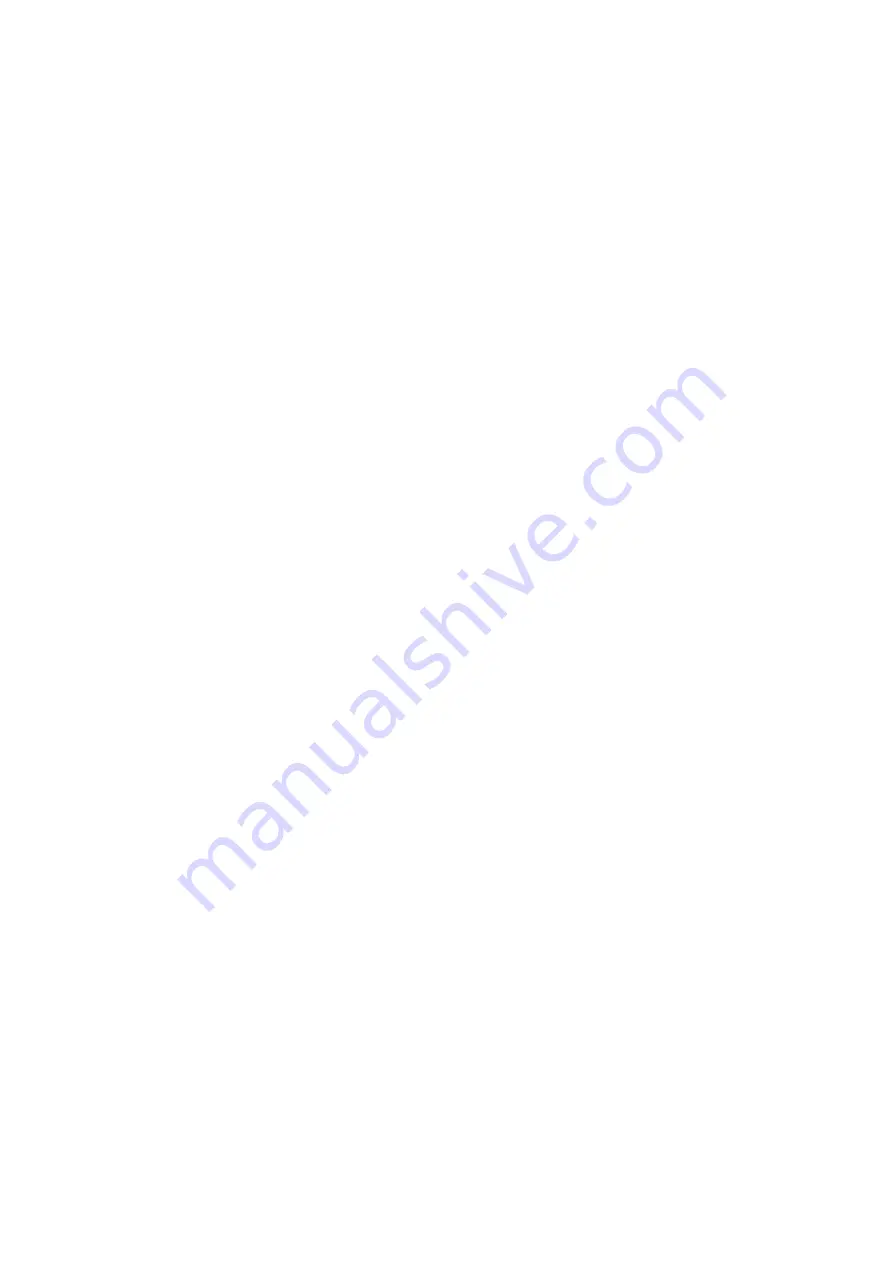
22
If you crash, look for signs of damage, and have them checked out. Remember that damage may not be visible to the
untrained eye. Do not fly until you're sure the component is safe. Even if you never crash, you should frequently
inspect the carbon parts and components of your glider for any gouges, deep scratches, cracks, loose fibers or other
surface cracks and stop flying until you fix the problem.
Do not use any kind of paint stripper to clean the carbon, because it may damage the epoxy resin matrix holding your
carbon together.
It's fine to wash carbon components using warm soapy water. After cleaning, rinse and dry them carefully.
Also, it may seem obvious but we would like to emphasize that you should never drill holes in carbon for any reason,
no matter how logical it may seem at the time. If you're planning on doing so please contact us first.
Crashed or damaged carbon components that show signs of damage, such as cracks, chips, loose fibers or fatigue
marks, or those that you even suspect were damaged, should be taken out of use immediately and inspected by
Aeros or another qualified expert to ensure they're still safe. If evidence of damage is found, the components should
be replaced or repaired.
Avoid over torquing as it is is another cause of cracks in carbon products.
Another important step is to check parts during installation and assembly to ensure that there are no burs, rough
spots, dirt or metal shards that could cut into and harm the carbon when the components are assembled and
tightened. The surfaces must be smooth and clean.
When transporting your glider use caution to protect the transverse rails of the roof rack with pipe insulation or
something that keeps the frame of the glider well protected against the rails and decrease the bearing pressures.
When transporting a few gliders be extremely cautious and protect your glider against other gliders. Do not pile up
the gliders against each other, this may cause serious damage to the carbon components of the glider.
PROCEDURE FOR CHECKING CARBON FIBER CROSSBEAMS APPLIED IN AEROS HANG
GLIDERS
The present procedure is applicable for composite crossbeams (hereinafter -crossbeams") used in the frame of the
hang gliders Combat and consists of visual inspection.
1. General inspection. The crossbeam should be free of visible defects/damage of the bearing structure of its walls
and bands. Delaminating of decorative coating is possible and it doesn't influence strength of the crossbeam.
2. Root junction of the crossbeam attachment. Bushings should not be biased; this is determined using glue marks
around their flange. The slack of the bushings in relation to the crossbeam is not allowed.
3. Tip attachment junction. The tip of the crossbeam should have no disintegration and visible damage.
CAUTION
In any case when damage is discovered, the repairiability of the crossbeam should be determined by a
representative of Aeros Ltd or by the manufacture of the crossbeam.
Conclusion about further possibility to use the crossbeam can be made only after loading the crossbeam
and can be done by a representative of Aeros Ltd or by the manufacture of the crossbeam only.
A NOTE ABOUT CABLES AND CABLE MAINTENANCE
The cables which support the glider’s airframe are critical components of the glider’s structure, and must be
maintained in an air worthy condition. It is a general practice in the design of aircraft structures to design to an
ultimate strength of 1.5 times the highest expected load in normal service.
Hang glider cables, like other structural components on the glider, are typically designed with a structural safety factor
of only about 50% above the expected maximum load. No significant loss in cable strength can be tolerated.
A cable with even a single broken strand must be replaced before the glider is flown again. A cable which has been
bent sharply enough to have taken a permanent set must also be replaced immediately.
Some degree of fatigue due to repeated bending of cables is almost unavoidable in an aircraft that is assembled and
disassembled with every flight. Side wires are subject to the highest loads in flight, and are therefore the most
critical. This is why we recommend that these wires be replaced annually, even if there is no known damage.
Содержание Combat-12.4-GT
Страница 2: ...2 ...
Страница 29: ...Combat GT 12 4 12 7 13 5 ...
Страница 30: ......
Страница 31: ......
Страница 32: ......
Страница 33: ......
Страница 34: ...CBT10 12 023 000 AD CBT10 12 023 000 AD ...
Страница 35: ......
Страница 37: ......
Страница 38: ......
Страница 39: ......
Страница 40: ......
Страница 41: ......
Страница 42: ......
Страница 44: ......
Страница 51: ......
Страница 52: ......
Страница 53: ......
Страница 54: ...CBT 200 000 AD ...
Страница 55: ...CBT 200 000 AD ...
Страница 56: ...CBT 200 000 AD ...
Страница 57: ...CBT2 220 000 AD ...
Страница 59: ...Combat GT 13 5 STL 263 000 ...