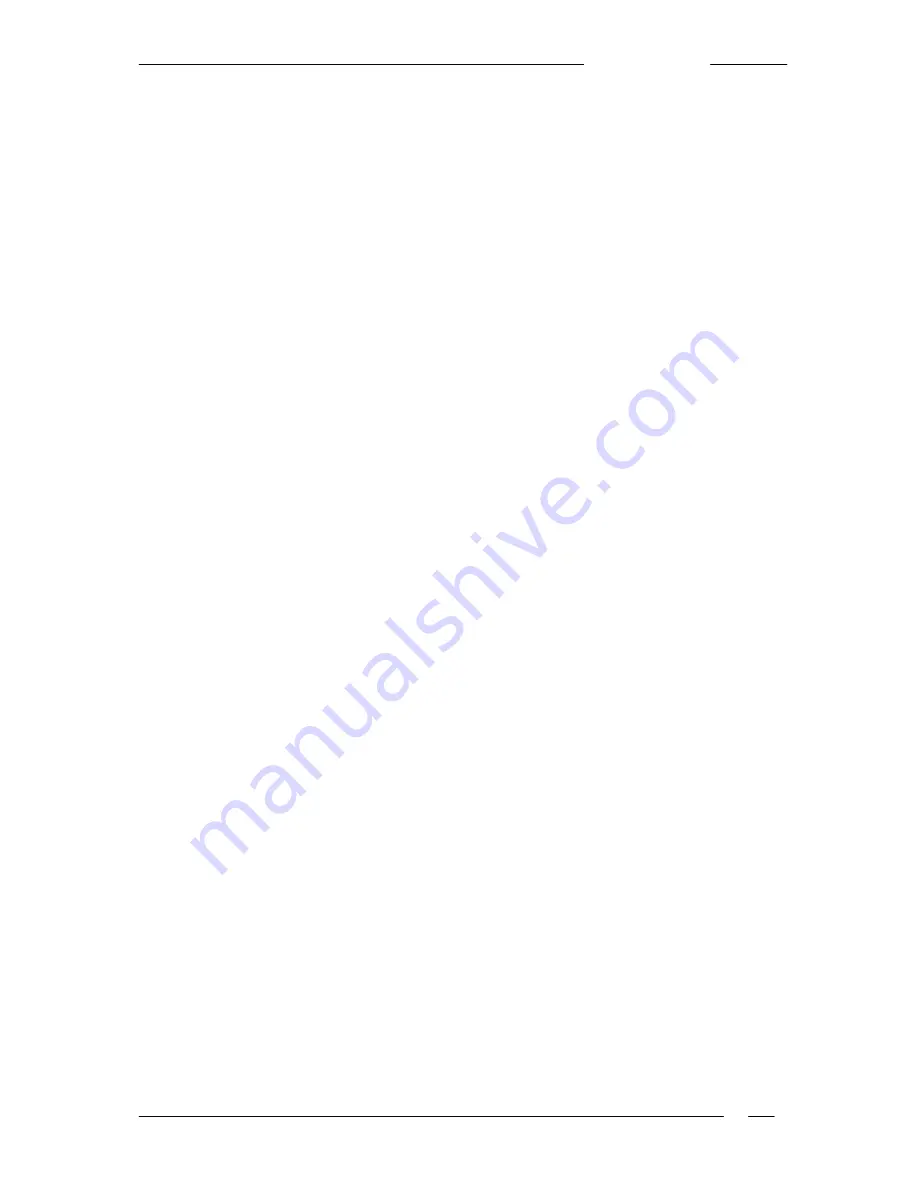
Pober Pixie
Pober Pixie building instructions
5
•
Slit and peel off a strip of film about 10 - 15 mm wide in the centre of the top surface in the same
manner (for attaching the fin and strake).
•
Cyano glue can also be applied directly to the film. In this case it is important to sand the joint line
carefully and to apply the glue very accurately, because cyano behaves differently to epoxy, and
the glued joint may fail after a shock.
•
Carefully replace the tailplane on the fuselage and epoxy the parts together.
Vertical stabiliser - fin and rudder
•
The fin and strake are made of balsa and sanded. They are prepared for installation, including
two slots for hinges. The strake consists of two parts.
•
Offer up the strake to the tailplane (attached to the fuselage) and sand it to fit accurately. Glue the
strake to the fin. Sand this assembly smooth, taking care to shape the leading edge as shown.
•
Check that the assembly fits neatly on the fuselage, then cover the fin and strake with film.
•
Be sure to leave a strip of bare wood about 5 mm wide at the bottom of the fin on both sides.
•
Glue the covered fin assembly in place, taking care to set it exactly vertical relative to the
tailplane, and in line with the fuselage centreline.
•
Cut the 8 x 8 mm triangular bracing strips to length (DET. 6) and trim them to fit. Cover the
outside surface of the strips, and glue them in the joints between the tailplane and the fin.
•
Attach the hinges to the fin and tailplane and prepare the recess for the steerable tailwheel
control rod.
Installing the servos and “snakes”
•
Cut out the openings in the servo plate (plywood part #6) to match the actual size of your servos.
•
Prepare the servo plate for installation in the fuselage as shown in the drawing (DET. 7).
•
Sand the servo plate and trim it to fit in the fuselage. Glue the spruce strips on the underside and
trim this assembly to fit in the fuselage. Apply epoxy to the hardwood strips and glue the servo
plate in the fuselage.
•
Preparing the linkages: these are based on the 8 x 8 mm balsa pushrods supplied. Attach an M2
metal clevis to one end - see drawing (DET. 8): bend the final 5 mm of the metal rod at 90°, push
the angled end into the balsa pushrod, wrap thread round it and secure the joint with cyano or
white glue. Cut the pushrod to the required length to suit the exact position of the servo and the
control surface hinge line, then attach a metal clevis to the other end.
•
Cut the pushrod exit slots in the tail end of the fuselage - to avoid unnecessary slop in the control
system, the run of the pushrod should be as straight as possible, and the metal rod should be
bent as little as possible. We recommend that you provide support for the pushrod across the
fuselage as shown in the drawing. This is necessary because the exit slots in the fuselage for the
elevator and rudder pushrods must be at different levels to avoid the pushrods fouling each other.
Tip:
this task is much easier if you cut an access opening in the tailplane support surface.
•
The pushrods must be installed in such a way that lost motion (play) in the control system is
minimised, that the fore-and-aft travel of the pushrod is unrestricted, that the pushrods cannot
touch each other, and that the end-pieces are well secured, e.g. using a locknut and cyano.
•
The aileron pushrods should be cut to correct length after they are installed. Each pushrod
consists of an M2-threaded steel rod.
•
Prepare the servos and control surface horns.
•
Screw a metal M2 clevis to one end; at the other end the clevis should be soldered to the rod.
Wings
The wings are supplied as bare, ready-made, built-up structures. The leading edge section is a strong
torsion box, and all reinforcing and joiner components are factory-fitted (see plan).
This construction has clear benefits when you are flying the model, but it also offers the advantage
that the panels are straightforward to cover. The wing consists of three panels: a permanently
mounted centre section and two removable outboard panels.
The centre section features pre-drilled and prepared mounting holes, plus holes for the retaining
screws.