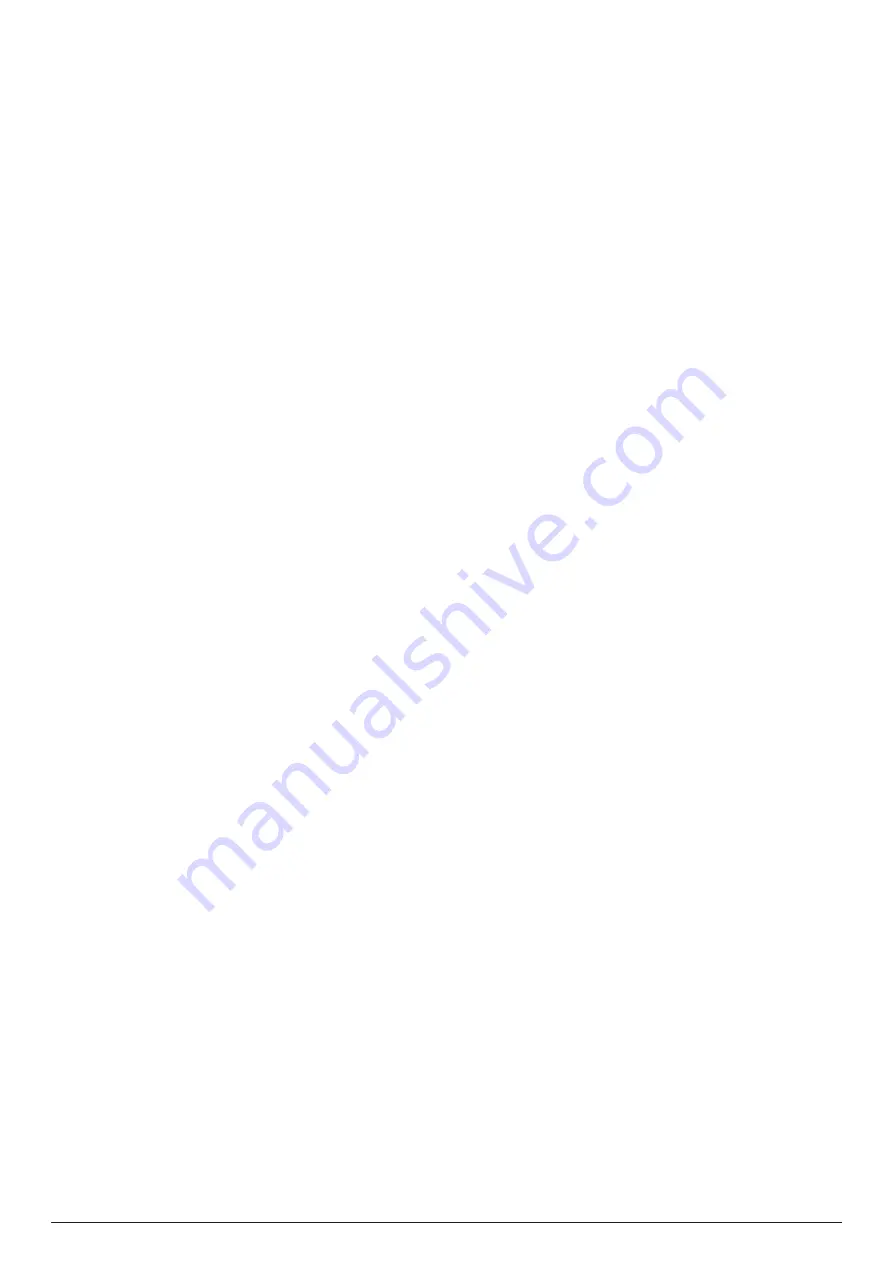
20
20.05 – 4138421_03
PREVENTION AGAINST RESIDUAL RISKS DUE TO PRESSURE OR
HIGH/LOW TEMPERATURE
- The unit contains under pressure gas: no operation must be per-
formed on under pressure equipment except during maintenance
that must be carried out by competent and authorised personnel;
- Perform brazing or welding only on empty pipes and clear of any
lubricating oil residues; do not near flames or other heat sources to
the pipes containing under pressure fluids;
- Do not work with naked flames near the unit;
- Do not bend or hit pipes containing under pressure fluids;
- The unit is equipped with overpressure release devices (safety valve):
if these devices intervene, the refrigerant gas is released at high
temperature and speed;
- The machine and the pipes have very hot or very cold surfaces that
lead to risk of burns by contact;
- Do not use your hands to control any refrigerant leaks;
- Before removing elements along the under pressure hydronic cir-
cuits, shut-off the pipe section involved and gradually drain the fluid
until its pressure and that of the atmosphere are balanced.
PREVENTION AGAINST RESIDUAL ELECTRICAL RISKS
- Before opening the electrical panel, disconnect the unit from the
mains by means of the external isolator;
- If the unit has power factor correction condensers, wait the time
indicated on the machine plate from when the power supply was dis-
connected from the unit before accessing inside the electrical panel;
- If the unit is equipped with integrated inverter type compressors,
disconnect the power supply and wait at least 15 minutes before
accessing for maintenance: the internal components remain live for
this time, generating the risk of electrocution.
- If the power supply cable is damaged, it must be replaced by the
manufacturer, After Sales Service or by another similarly qualified
person, to avoid dangerous situations.
CLEANING THE MACHINE
The machine must be turned off and electrically disconnected when
being cleaned.
INSPECTION AND CONTROL
The machine must be turned off and electrically disconnected during its
inspection and leak check.
ROUTINE AND EXTRAORDINARY MAINTENANCE
The machine must be turned off and electrically disconnected during its
maintenance (with possible replacement of components). In particular:
- Before any intervention, isolate the unit from the mains by means of
the external isolator provided for the insertion of padlocks (up to 3)
for blocking in ‘’open’’ position;
- Place a sign reading ‘’Do not turn on – maintenance in progress’’ on
the open isolator;
- Equip yourself with tools in good condition and make sure to have
fully understood the instructions before using them;
- Equip yourself with the appropriate personal protective equipment
as indicated in paragraph 1 of this report;
- For outdoor units, do not perform interventions in dangerous weath-
er conditions such as rain, snow, fog, thunderstorms, etc;
- The cooling circuit components must be replaced after draining the
refrigerant gas contained in the circuit;
- During venting protect yourself against any leakage of fluids at dan-
gerous temperatures and/or pressures;
- Always use appropriate equipment (extractor, antistatic bracelet etc)
when replacing electronic boards;
- If replacing a motor, compressor, evaporator, condensing coil or any
other heavy element, make sure that the lifting devices are compati-
ble with the weight to be handled;
- In air units with independent compressor compartment, do not
access the fan compartment without having first disconnected the
machine through the isolator on the board and having placed a sign
reading ‘’Do not turn on – maintenance in progress’’;
- Always and only use original spare parts purchased directly from Aer-
mec or from official dealers. Contact Aermec should it be necessary
to move the unit one year after its positioning on-site or it must be
dismantled;
- It is not permitted to change the refrigerant, hydraulic or electric
layout of the unit, or its control logic unless expressly authorised by
Aermec;
- The machine must be loaded with the refrigerant in the feature label
and in the required quantity;
- Make sure to have removed all tools, electrical cables or other loose
object and having perfectly connected the machine to the system
before closing it and starting it;
- The inspections and measurements necessary to establish the correct
functioning of the machine to be run with the machine in operation,
must be performed with the machine closed (framework fixed on
the machine), reading the measurements collected by the control
board and viewable in the control panel of the same. In the case of
machines with cooling circuit compartment open, stand in front of
the control panel of the electrical panel remaining distant and not
exposed to the under pressure parts of the cooling circuit
- If replacing a fuse or a circuit breaker, details relating the type and
ratings of fuses or circuit breakers are visible in the mark inside the
electrical panel.
ATTENTION
When having to take measurements with the machine on and the
electrical panel and cooling circuit open, be careful since the machine is
live, the cooling circuit contains high pressure gas, the pipes may be hot
or cold, some parts may be in motion.
Any absorption measurements of the compressors, compressor casings,
pumps and fans as well as the power supply measurements, must be taken
as follows:
- With machine off, access its panel;
- Connect the measuring instruments such as current clamps (to meas-
ure the current) and multimeters (to measure the voltage). These
instruments must be fitted with appropriate terminals/clamps that
allow to remotely control the measurement;
- Access the machine and read the measurements made by the instru-
ments, keeping AWAY from live electrical parts;
- As soon as the measurements are taken, turn off the machine, re-
move the instruments and close the electrical panel.
The measurements of the compressor inlet and outlet temperature and
pressure to determine the overheating and subcooling of the machine,
must be carried out as follows: