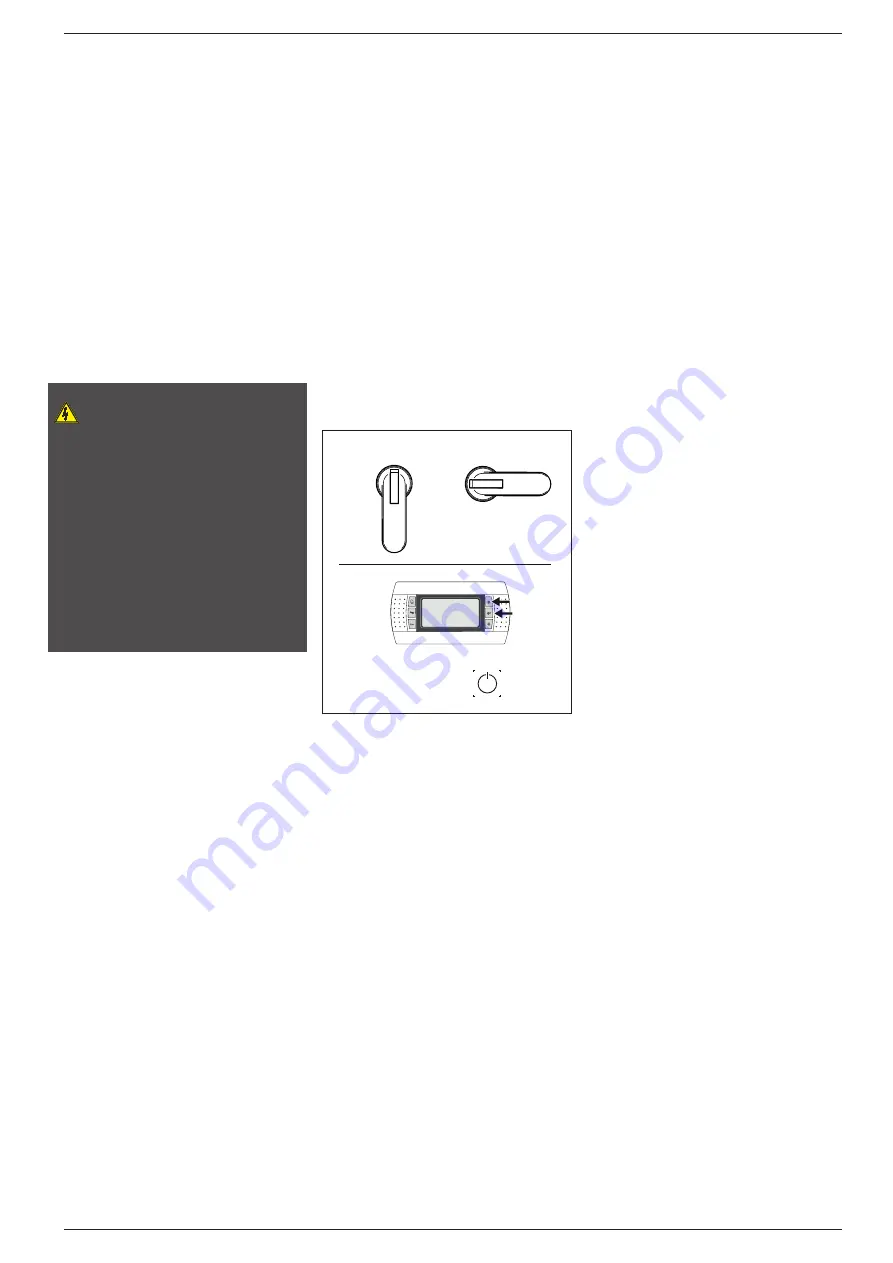
EN - 17
NLC_A COD: 1606.4037360_00
14.
CONTROL AND FIRST
START-UP
PREPARATION FOR COMMISSIONING
Bear in mind that a free start-up service is
offered by the Aermec Technical Service for
the unit of this series, at the request of Aermec
customers or legitimate owners and in ITALY
only. The start-up must be previously agreed on
the basis of the system implementation times.
Before the intervention all the operations
(electrical and hydraulic hook-ups, loading and
venting of the air from the system) must be
completed.
START-UP
PRELIMINARY OPERATIONS TO BE
CARRIED OUT WHEN THERE IS NO
VOLTAGE
Check:
All the safety conditions have been respected
The unit has been properly secured to the
support base
The minimum technical spaces have been
observed;
That the main power cables are of an
appropriate section, capable of supporting
the overall absorption of the unit. (see electric
data section), and that the unit has been duly
earthed.
That all the electrical connections are correctly
fixed and that all the terminals adequately
tightened.
THE FOLLOWING OPERATIONS MUST BE
CARRIED OUT WHEN THE UNIT IS LIVE.
Power up the unit by turning the main switch
to ON. The display will come on a few seconds
after the machine is powered up, check that the
operation status is at OFF (OFF BY KEYB at the
bottom of the display).
Use a tester to check that the value of the
supply voltage to the U.V.W. phases is equal to
400V ±10%, and also check that the unbalance
between the phases does not exceed 3%.
Check that the connections made by the installer
comply with the data in the documentation.
Check that the electric heater(s) of the
compressor casing are working, by measuring
the rise in the temperature in the oil sump. The
resistance(s) must operate for at least 12 hours
before the compressor start-up, and in any case
the temperature of the oil sump must be 10-
15°C higher than the room temperature.
Check and if necessary change the fan settings
in order get the correct useful static pressure
required by the system
(
Setting the fan's
number of rpm from the control panel)
.
HYDRAULIC CIRCUIT
Check that all the hydraulic connections have
been carried out correctly, that the information
on the plates have been complied with and
that a mechanical filter has been installed at
the evaporator inlet. (Mandatory component
subject to the invalidation of the warranty).
The flow switch must absolutely be installed,
and should be wired to the electrical panel,
calibrated and its intervention verified
(Obligatory component subject to the
invalidation of the warranty).
Check that the circulation pump(s) are working,
and that the water flow rate is sufficient to
close the flow switch contact.
Check the water flow rate, measuring the
difference of pressure between the evaporator
inlet and outlet, and then calculate the flow
rate with the evaporator pressure drop diagram
in the this documentation.
Make sure the flow switches are working
correctly (installation mandatory)
; closing the
cut-off valve at the heat exchanger outlet; the
block should be displayed on the unit's control
panel; finally open the valve again and rearm
the block.
FIRST COMMISSIONING OF THE
MACHINE
ON
ON
OFF
OFF
SELECT MENÙ
ON/OFF
WITH THE MACHINE ON CHECK THE
REFRIGERANT CIRCUIT
CHECK:
•
Check that the absorption current of the
compressor is less than the maximum
indicated in the technical data table.
•
Check that in models with three-phase
supply power the noise level of the
compressor is not abnormal, symptom
of reverse rotation and, if this is the case,
invert a phase.
•
Make sure that the voltage value is within
the pre-fixed limits and that the unbalance
between the three phases (three-phase
supply power) does not go above 3%.
•
Check for refrigerant gas leaks, especially
near the pressure points of pressure
gauges, pressure transducers and pressure
switches; (vibrations during transport may
have loosened the connections).
OVERHEATING
By comparing the temperature read with a
contact thermostat placed on the compressor
intake and the temperature shown on the
low pressure gauge (saturation temperature
corresponding to the evaporation pressure). The
difference between these two temperatures
gives the overheating value. Optimum values
are between 4 and 8°C.
DISCHARGE TEMPERATURE
If the sub-cooling and overheating values are
correct, the temperature measured in the
pressing line tube at the compressor outlet
must be 30/40°C above the condensation
temperature.
CONTROL AND SAFETY DEVICES
CHECK
:
THE MANUAL RESET HIGH PRESSURE
SWITCH
That stops the compressor and generates
the respective alarm when the flow pressure
exceeds the set value. To check it is operating
correctly, close the air intake to the heat
exchanger (cooling mode), and keeping an eye
on the high pressure gauge, check it intervenes
at the calibration setting. Warning: If the switch
does not trip at the calibration value, stop the
compressor immediately and check the causes.
The reset is manual and can only take place
when the pressure drops below the differential
value. (For the set and differential values, see
the technical manual).
ANTI-FREEZE CONTROL
The anti-freeze control, which is managed by
electronic regulation and by the temperature
probe at the evaporator outlet, has the function
of preventing the formation of ice when the
water flow rate is too low. Checking it is working
correctly can be carried out by progressively
increasing the anti-freeze set-point until it
exceeds the outlet water temperature and
keeping the water temperature under control
with a high precision thermometer. Check that
the unit switches off, setting off the respective
alarm. After this operation take the anti-freeze
set-point back to its original value.