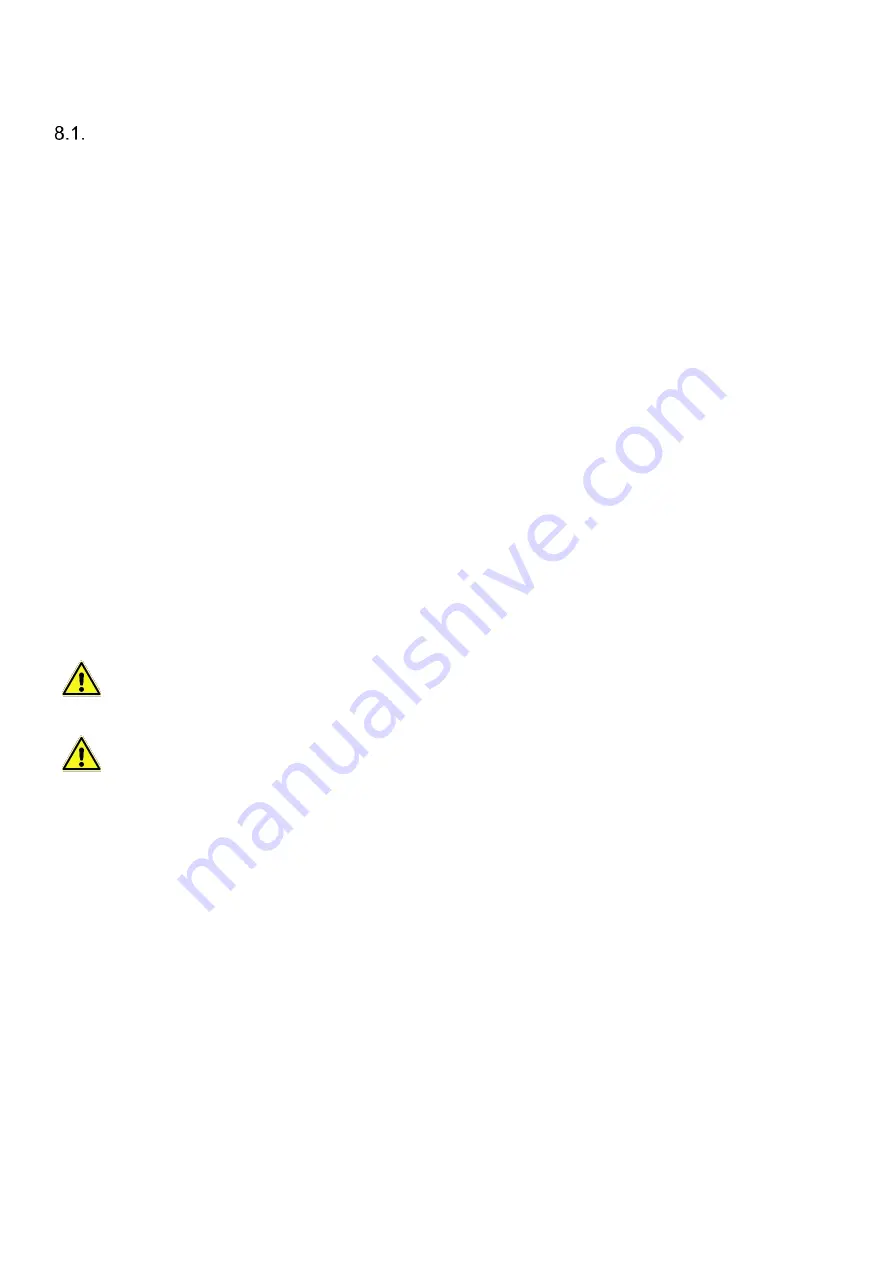
TF7039GB_A_NOT
Page 39 of 48
8.
MAINTENANCE
EXTRAORDINARY MAINTENANCE
The unit is factory filled with R410A gas and fully tested. As per standard conditions, technical service does
not need to intervene to check the cooling gas. This will cause the unit to malfunction. In these cases, the
refrigerant outlet points must be determined, repaired and the cooling circuit replenished.
The following procedure should be used for filling:
•
Empty and drain the entire cooling circuit. Use a vacuum pump connected to both the low- and high-
pressure ports until the negative-pressure gauge reads approximately 10 Pa. Wait a few minutes
and make sure that said value does not rise above 50 Pa again.
•
Connect the cooling gas cylinder or filling cylinder to the connection on the low-pressure line.
•
Add the quantity of cooling gas specified on the unit type plate.
•
After a few hours of operation, check that the liquid indicator indicates that the circuit is dry (dry
–
green). In the case of partial losses, the circuit must be completely emptied before being refilled.
•
The refrigerant R410A may only be added when liquid.
•
Operating conditions that deviate from the nominal values lead to deviating values.
•
A leak test or leak detection may only be carried out with refrigerant R410A and suitable leak detec-
tion devices.
•
The use of oxygen, acetylene or other flammable or toxic gases in the cooling circuit is prohibited,
as this can lead to explosions and poisoning.
Safety checks, maintenance work and any repairs may only be carried out by qualified personnel
who are legally qualified to do so and who have a certificate of competence for the corresponding
category.
Inadequate inspections/maintenance work can lead to damage to objects and persons.
All work on the device must be carried out after disconnecting the device from the mains (main
switch). Due to possible residual voltage at the frequency inverter (inverter module), wait at least
5 minutes after actuating the main switch (disconnect the unit) before starting work.