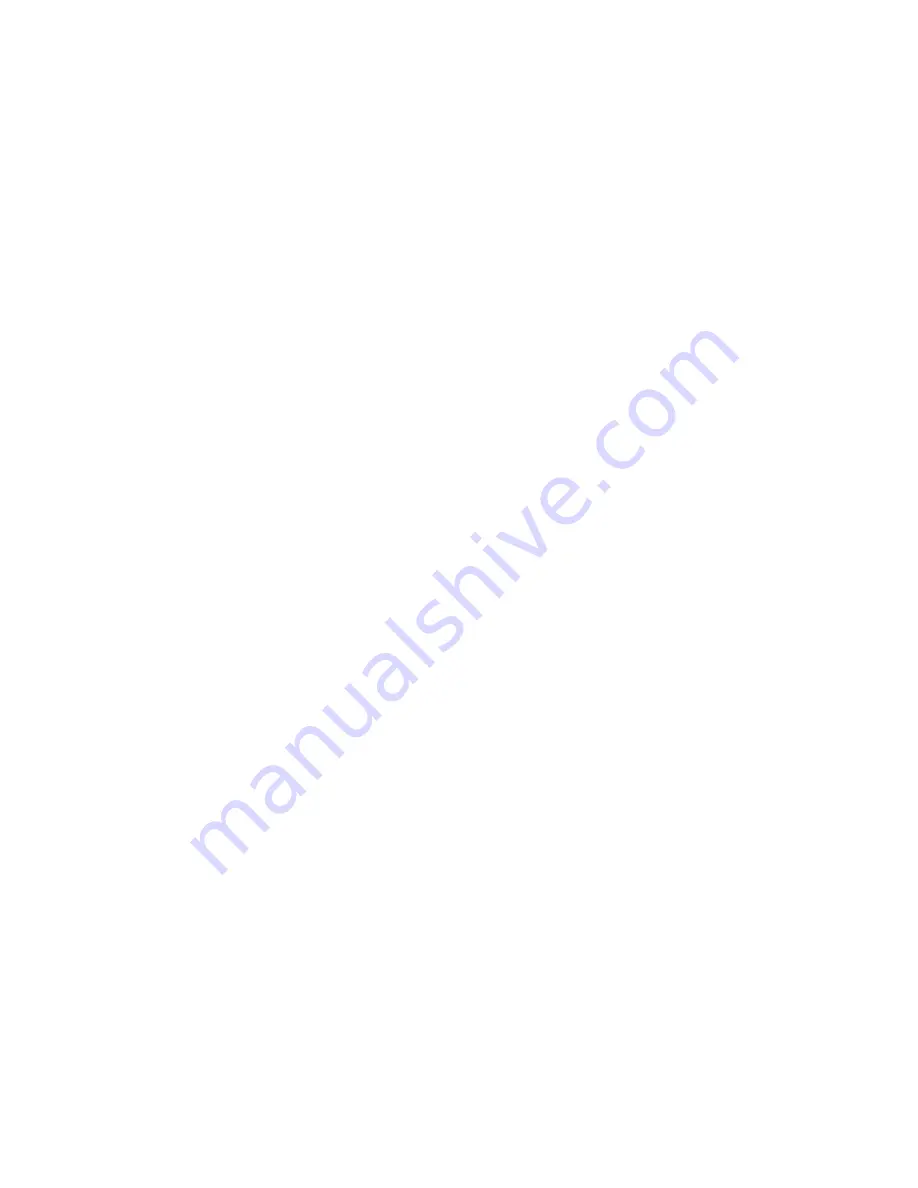
Activ
Media Robotics
The Gripper is connected electronically to the H8S-controller through digital input and
output ports of the User I/O connector. AROS Gripper servers interface with the device
and manage the low-level details of its operation. Upon startup or reset, the
microcontroller automatically deploys the lift to its lowest position, gripper paddles
closed.
See the AROS chapters for additional operating and programming details.
S
AFETY
W
ATCHDOGS
Besides the protective fixed-range and breakbeam IRs, and the protective bumpers fore
and aft described earlier in this chapter, your Performance PeopleBot’s AROS also
contains a client-server communication
watchdog
that will halt the robot’s motion if the
connection between your PC client and the robot server is disrupted for a set time
interval, nominally two seconds (
watchdog
FLASH
parameter). The robot will
automatically resume activity, including motion, as soon as communications are
restored.
AROS also contains a stall monitor. If the drive exerts a PWM control signal that equals or
exceeds a configurable level and the wheels fail to turn (
stallval
), motor power is cut
off for a configurable amount of time (
stallwait
). The server software also notifies the
client through the standard Server Information Packet which motor is stalled. When the
stallwait
time elapses, motor power automatically switches back on and motion
continues under server control.
There also is the
LowBattery
FLASH parameter that sets off an audible warning when the
batteries fall below that safe charge level. To avoid systems corruptions, the AROS
servers also force a soft system shutdown when the batteries fall below approximately 11
volts. The soft shutdown includes disconnection from a connected client. The Linux
genpowerd
daemon or Windows’
ups.exe
program monitor the
RI
signal on the
HOST
serial port and shutdown the onboard PC, too.
All these “failsafe” mechanisms help ensure that your robot will not cause damage or be
damaged during operation. You may reconfigure the various FLASH-based parameter
values to suit your application. See Chapter 7,
Updating & Reconfiguring AROS
, for
details.
23