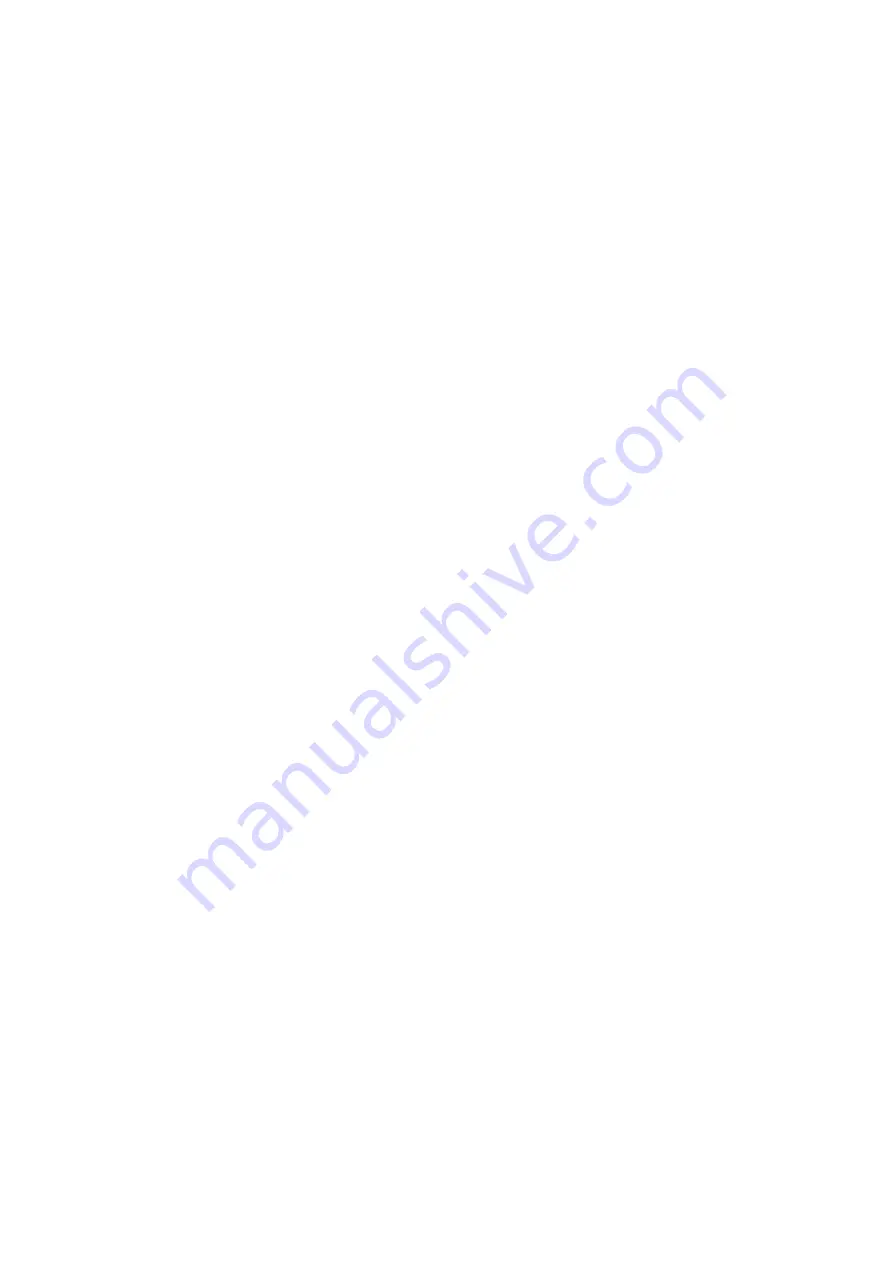
15
15. MAINTAINING
That's easier to keep machine in good condition or best performance by means of maintaining it at any
time than remedy it after it is out of order.
(1) Daily Maintenance (by operator)
(a) Fill the lubricant before starting machine everyday.
(b) If the temperature of spindle caused over-heating or strange noise, stop machine immediately to
cheek it for keeping accurate performance.
(c) Keep work area clean; release vise, cutter, work-piece from table; switch off power source; take
chip or dust away from machine and follow instructions lubrication or coating rust proof oil
before leaving.
(2) Weekly Maintenance
(a) Clean and coat the cross leading screw with oil.
(b) Check to see if sliding surface and turning parts lack of lubricant. If the lubricant is insufficant,
fill it.
(3) Monthly Maintenance
(a) Adjust the accurate gap of slide both on cross and longitudinal feed.
(b) Lubricate bearing, worm, and worm shaft to avoid wear.
(4) Yearly Maintenance
(a) Adjust table to horizontal position for maintenance of accuracy.
(b) Check electric cord, plugs, switches at least once a year to avoid loosening or wearing.
16. CLEANING & LUBRICATING
CLEANING
(1)
Your machine has been coated with a heavy grease to protect it in shipping. This coating should be
completely removed before operating the machine. Commercial degreaser, kerosene or similar
solvent may be used to remove the grease from the machine, but avoid getting solvent on belts or
other rubber parts.
(2) After cleaning, coat all possible rusted surface with a light lubricant. Lubricate all points with a
medium consistency machine oil.
LUBRICATION:
All ball bearings in your mill/drill are sealed for life, requiring no lubrication. Points requiring
lubrication are:
(1) Internal spline drive assembly. Keep this area well lubricated with a good grade non-hardening
grease, such as Fiske Company "Lubriplate". Insert grease in the hole at the top of spindle pulley
spline driver. Lube twice yearly.
Содержание 46SF
Страница 1: ...COMPLEX MACHINE MODEL 46SF INSTRUCTION MANUAL 46SF 080911 R3...
Страница 10: ...8 4 MINIMUM ROOM SPACE FOR MACHINE OPERATION...
Страница 21: ...19 CIRCUIT DIAGRAM...
Страница 23: ...21...
Страница 24: ...22...
Страница 25: ...23...
Страница 26: ...24...
Страница 27: ...25...