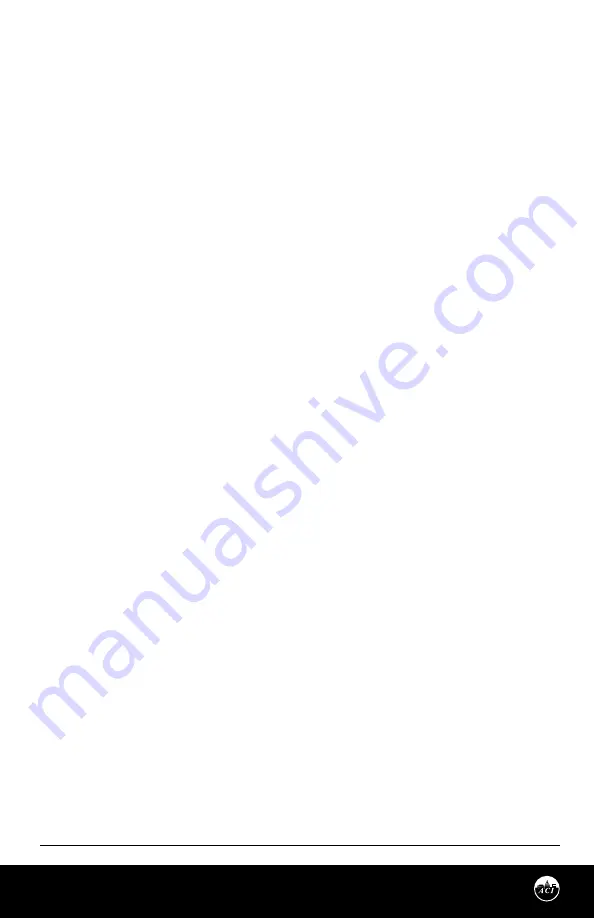
Automation Components, Inc.
2305 Pleasant View Road | Middleton, WI 53562
Phone:
1-888-967-5224 |
Website:
workaci.com
Page 5
Version: 6.0
I0000475
Pulse Width Modulated (or PWM) input
(Continued)
the COM terminal. Reference Figure #2. Count to 50% of timing range and remove. Verify the pulse UP LED
indication. Voltage can be measured across the input to verify proper voltages. Read the output. Has the
output changed? The output should be close to 50% of set output. If no, contact ACI Technical Support. If
yes, unit is functioning properly.
FLOATING POINT / TRI-STATE
Apply 24 VAC/VDC to the PWR terminals. Connect your meter to the Wiper and Minimum terminals on the
output terminal block. Set meter to resistance range of resistor network. Connect a jumper wire from UP
to the 24V “+” terminal (this is your jumper wire #1). Connect a jumper wire to the 24V “-“ only (this is your
jumper wire #2). You are now ready to simulate a timed Up signal. For testing purposes, select the 30 or 45
second range on version 2. Be sure to reset power to allow the DRN3.1 to recognize new settings. Take the
free end of jumper wire #2 and connect by holding wire to the Com terminal. Count to 50% of timing range
and remove. Verify the pulse UP LED indication. Voltage can be measured across the input to verify proper
voltages. Read the output. Has the output changed? The output should be close to 50% of the set output.
Moving jumper wire #1 from UP to DOWN, and repeating the same test, should decrease the output signal.
If no, contact ACI Technical Support. If yes, unit is functioning properly.
TESTING THE OUTPUT
Measured resistance from Wiper to Minimum terminal blocks will begin at the minimum signal, as
specified by your resistor network, and will increase proportionally to the commanded input value. To
reverse the output signal, measure resistance from Wiper to Maximum terminal blocks. This will begin at
the maximum signal, as specified by your resistor network, and will decrease proportionally to the
commanded input value. A clicking sound will occur when resistance is changed. Resistance changes in
steps and is divided into 256 equal steps. Exception is version 3 where step size is selected.
Command a change or simulate an input signal to change the output. Measure the resistance value. If the
resistance has not changed, check settings and reset power.
Verify the input is functional.
If yes, then contact ACI Technical Support.
MOST COMMON PROBLEM
The analog input from the controller can contain electrical noise. This noise is seen by the DRN3.1 as a
change in commanded input signal and quickly changes the output. The most common symptom is a
constant chatter of the relays. Standard precautions should be taken to prevent noise on the signal input
of the DRN3.1 (i.e.: Do not run signal wiring near line voltage wiring or florescent light fixtures). Versions 1
and 2 of the DRN3.1 were modified in 2001 to add extra filtering to the input. Time response full scale is
about 6 seconds. Check version number on your DRN3.1. If high speed response or extra filtered versions
is required contact ACI Sales Department.
TEST POINTS FOR RESISTOR NETWORK (RN) CARD
The Resistor Network card does not have to be attached to the DRN3.1 motherboard for this test, but if
attached to the DRN3.1, you must remove power before testing. Using an OHM meter, test the last resistor
as illustrated on page 1. The value indicated should be ½ the total resistance range of the Resistor Network
card.
Example:
A 500 Ohm reading indicates a 0 to 1000 Ohm Resistor Network card.
A 750 Ohm reading indicates a 0 to 1500 Ohm Resistor Network card.