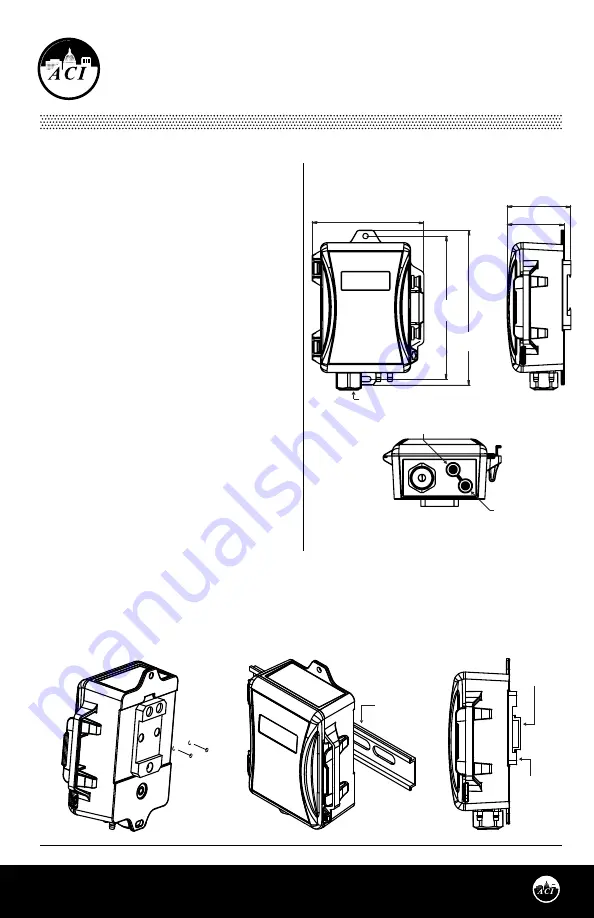
Automation Components, Inc.
2305 Pleasant View Road | Middleton, WI 53562
Phone:
1-888-967-5224 |
Website:
workaci.com
Page 1
Version: 15.0
I0000777
Version: 15.0
I0000777
FIGURE 1:
DLP DIMENSIONS
DLP SERIES
Installation & Operation Instructions
Phone:
1-888-967-5224
Website:
workaci.com
4.35"
(110.43 mm)
2.23"
(56.52 mm)
2.48"
(62.99 mm)
5.56"
(141.29 mm)
6.02"
(152.82 mm)
CORDGRIP /
1/2 “ CONDUIT FITTING
HIGH PRESSURE PORT
LOW PRESSURE PORT
-H
-L
PRECAUTIONS
• Do not switch pressure range and output
mode when power is on. Make sure to power off
the unit first, then set the DIP Switches to the
correct positions and then power on the
transmitter.
GENERAL INFORMATION
The DLP Series is based on a piezoresistive, silicon
sensing element which senses Differential Pressure
and provides an analog output. Field selectable
analog outputs include 0-5 and 0-10 VDC, or 4-20
mA which correlate to a uni or bi-directional
pressure range from 0-0.1” up to 0-40” of water
column, depending on your model selection. Each
unit has up to 8 field selectable, uni or bi-directional
ranges (see
Figure 6
p. 3).
MEDIA
The DLP can be used to monitor the differential
pressure in any application that uses dry air or inert
gas.
Mounting
Find a suitable location for the enclosure. The DLP
has 2 two mounting holes located on the top and
bottom flanges. Drill pilot holes for the (2) #8 x 3/4”
self-drilling screws(supplied). Use the enclosure flange as a guide, or use the dimensions listed in
Figure 1
.
Mount the unit vertically with the brass fittings pointing towards the ground. This ensures that any
condensation that may form in the tubing does not have an effect on the pressure sensor. If mounting the
unit horizontally, a slight zero shift may occur and care must be taken to prevent moisture from building
up in the sensor.
FIGURE 2:
DIN RAIL MOUNTING
DIN RAIL
DIN RAIL
DIN RAIL
CLIP
DIN RAIL MOUNTING
(Optional)
Attach the DIN Rail Mounting accessory to the
back of the enclosure using the two screws
provided. To mount the sensor on the DIN Rail,
place the bottom of the DIN Rail Clip into the
35mm DIN Rail and push the unit upward to
engage the spring clip. Now press the top of
the unit back until it locks into place - see
FIGURE 2
(p.1).
PITOT TUBE INSTALLATION
(Optional)
Slip the rubber washer over the threaded end
of the pitot tube, keeping the washer as close
to the threaded end as possible. Fasten the
pitot into the threaded insert on the back of
the enclosure. Press the rubber washer against
the enclosure - see
FIGURE 3
.
Tubing Setup When Pitot Tube is Installed
Units will be shipped with silicone tubing
attached to the high and low pressure barb
fittings. The silicone tubing will need to be
removed from the High Pressure (H) barb
fitting and secured onto the pitot tube barb
fitting. This will leave the high pressure barb
fitting open to atmosphere, and the Low
pressure barb fitting remaining at default
setup.
Pressure Connections
The recommended connection tubing is ¼”
O.D push-on tubing (1/8” to 3/16” I.D.). For best
results, all tubing lengths should be limited to
a maximum length of 75 feet (23 meters).
Longer runs will affect the response time.
WIRING
PRECAUTIONS
• Remove power before wiring. Never
connect or disconnect wiring with
power applied.
• When using a shielded cable, ground the
shield only at the controller end.
Grounding both ends can cause a ground
loop.
• It is recommended you use an isolated
UL-listed class 2 transformer when
powering the unit with 24 VAC. Failure to
wire the devices with the correct polarity
when sharing transformers may result in
damage to any device powered by the
shared transformer.
• If the 24 VDC or 24VAC power is shared with devices that have coils such as relays, solenoids, or
other inductors, each coil must have an MOV, DC/AC Transorb, Transient Voltage Suppressor (ACI
Part: 142583), or diode placed across the coil or inductor. The cathode, or banded side of the DC
Transorb or diode, connects to the positive side of the power supply. Without these snubbers,
coils produce very large voltage spikes when de-energizing that can cause malfunction or
destruction of electronic circuits.
Open the cover of the enclosure. ACI recommends 16 to 26 AWG twisted pair wires or shielded cable for
all transmitters. Twisted pair may be used for 2-wire current output transmitters or 3-wire for voltage
output. Connect the wires to the unit’s finger push-button terminal blocks. Each DLP unit can be
configured to three output signals: 4-20 mA, 0-5 V or 0-10 V. Use the Wiring Connections and diagrams
to determine the proper wiring for your application. See
TABLE 1
(p.3) for Output Mode and Output
Signal switch positions.
Note:
When using 1/2” conduit, the strain relief fitting must be removed from the enclosure.
Note:
Make sure that any conduit or metal fittings do not come in contact with the circuit board.
ZERO FUNCTION
The DLP unit should be “ZEROED” before
pressure is applied to the unit. The zero button
is used to cancel out any offsets caused by
installation and sensor drift. The Zero
adjustment must be performed with NO
pressure applied to either side of the sensor.
Remove the tubing connected to the H(High)
and/or L(Low) pressure fittings. Push “ZERO”
button for more than three seconds before installation or whenever necessary.
For units with LCD display, “AUTOZERO” icon will be on when the unit enters zero mode. If zeroing
process is successful, the “AUTOZERO” icon will flash twice.
PRESSURE RANGE SELECTION
If a custom calibrated pressure range is ordered, DO NOT change the Pressure Range Selection DIP switch
settings.
Table 2
lists ACI’s 12 standard model #’s.
UNIDIRECTIONAL AND BIDIRECTIONAL
MODE
The DLP can operate in either unidirectional mode (0 – X
inWC) or bidirectional mode (± X inWC). Each unit could have
up to eight field selectable, uni or bidirectional ranges.
CAUTION
•
See TABLE 3 for your DLP model’s maximum pressure.
•
DO NOT switch pressure range or output mode when POWER is ON. Make sure POWER to the
unit is OFF. Failure to do so WILL NOT ALLOW any new switch settings to take place.
•
Choose differential pressure range based on the expected differential pressure in your
application. Move switches to the correct positions and THEN POWER ON the transmitter.
Unidirectional Mode
•
DIP switch SW3 position five set at UNI side.
•
DIP switch SW3 positions one and two are for Pressure Range Selection
Bidrectional Mode
•
DIP switch SW3 position five set at BI side.
•
DIP switch SW3 positions one and two are for Pressure Range Selection.
Note:
In Bidirectional mode, a value of 0 inWC will have an output equal to 50% of the output signal range
(12mA, 2.5V, 5V).
ADDITIONAL LCD FEATURES
LCD Engineering Units Adjustment
This option is ONLY for units with LCD display. Switch DIP switch SW3 position three to select Pa or inWC.
If switched with power on, unit change will not take place until power is cycled.
“Out Of Range”
“OUT OF RANGE” icon will be on when differential pressure is over or under the minimum or maximum
pressure range selected. If a DLP unit is outputting “OUT OF RANGE”, please turn off the unit immediately,
and check the pressure input with a gauge or other test instrument. Once the pressure has been verified,
set the Pressure Range Selection DIP switch to the proper positions based upon your maximum expected
differential pressure.
CALIBRATION
DLP utilizes a digital pot for Span calibration and is factory set. There is no Span potentiometer for
adjustment. In the event you require Span calibration, the unit must be sent back to ACI.
The Offset can be adjusted using the Auto Zero function discussed on pg 4. Drift is a function of stress
relaxation over time and this results in the offset shifting, and not the span . Periodically re-zeroing the
device will eliminate the effect of drift.