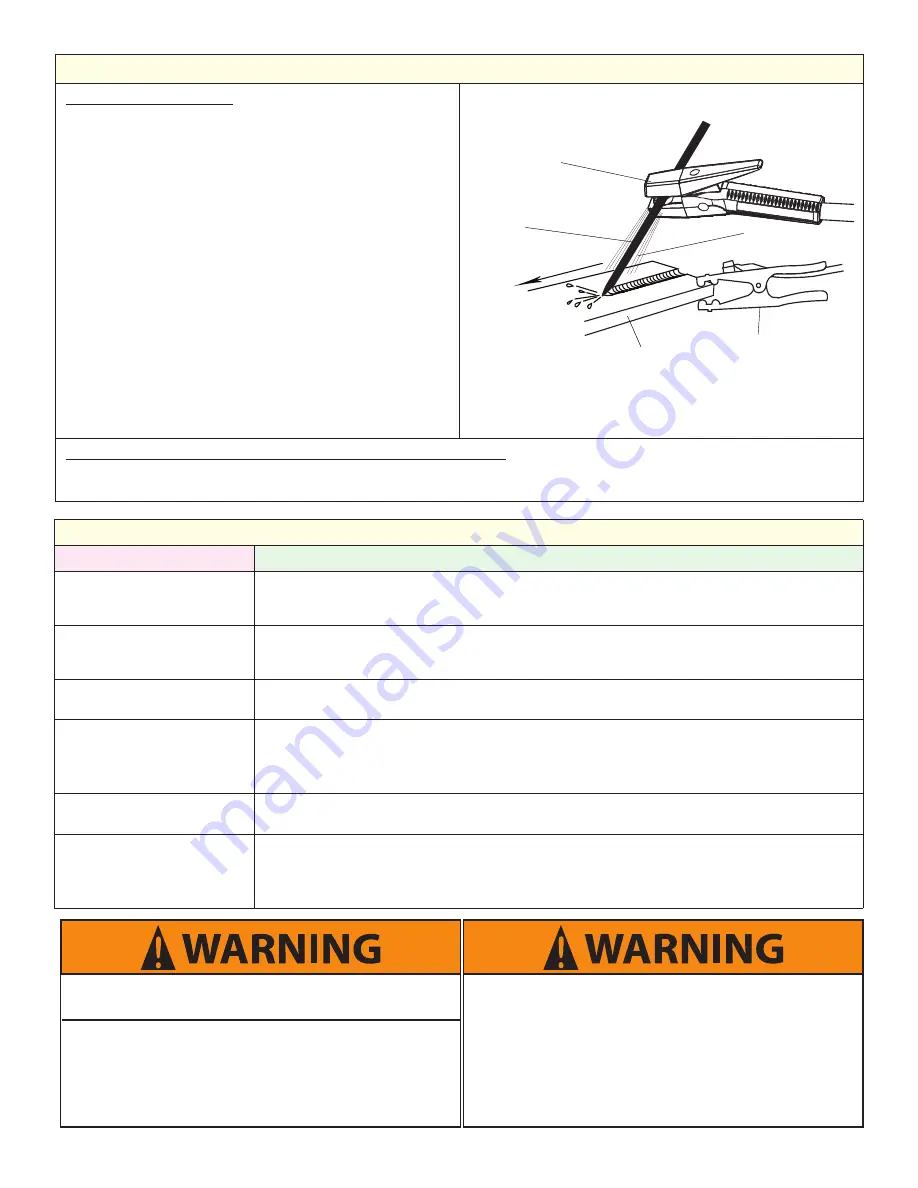
BASICS OF OPERATION
ARC GOUGING BASICS:
Read all warning and safety informa-
tion prior to operation. The torch must be installed as indicated in
(Figure 1) hook-up & installation procedure. Install the desired carbon
electrode (max stick-out 6” (152.4mm) - min stick-out 3” (76.2mm) )
in the jaws of the arc gouging torch, with the head air-jet holes facing
in the direction of the arc.
Secure the torch comfortable in your hand with the carbon rod angled
15° - 70° from the base material (see figure 2). The compressed air
supply must be on prior to gouging. When gouging on flat base material,
strike an arc by placing the electrode in contact with the base material.
Once the arc is established, maintain a short arc while moving in the
direction of travel (shown in figure 2) and don’t pull away from the
base material. Continue to steadily move forward (pushing the puddle
- not pulling), while maintaining a smooth electrical arc. The depth of
the gouge is controlled by the travel speed. If your application requires
a deep groove, use a slow travel speed. To obtain a shallow groove, a
faster travel speed can be used. Molten metal is removed with the com-
pressed air leaving a clean groove. Smooth and steady speed and feed
will result in a more uniform groove. Always be aware of the direction
of the molten metal to prevent potential contact with the operator and
or the surrounding areas.
HORIZONTAL, VERTICAL & OVERHEAD GOUGING POSITIONS:
Horizontal, vertical and overhead positions all use the same
procedures listed in the basic operations. Position the torch in an angle to prevent molten metal to contact the operator and be aware of your
surrounding environment. Take special care to the direction of the molten metal removed in all positions.
TROUBLE SHOOTING
PROBLEM
CAUSE / SOLUTION
Arc is unsteady… forcing the use
of a slower travel speed on shallow
grooves.
Amperage too low for the electrode diameter being used. In most cases the lowest recommended amperage is
enough, however, this requires greater operator skill. Choose mid-range amperage to improve arc stability. Use
the next smaller diameter electrode if the desired amperage cannot be obtained from the power source.
Electrode heating up rapidly, arc
jumping from side to side… er-
ratic groove.
The polarity of the torch hook-up is incorrect…most applications use DCEP (electrode positive). Check your
hook-up and installation for proper connections. There are very few metals that require a DCEN (electrode
negative).
Intermittent arc with noticeably
irreg ular groove surface.
Manual gouging travel speed is too slow. The operator should position the torch to produce a smooth forward
motion without resistance of the gloved hand to base material.
Carbon deposits at various spots
in groove or surface.
Shorted out carbon electrode on base metal. The travel speed may have been too fast compared to the amper-
age. Increase amperage or use a slower travel speed. Sometimes the pushing angle may be too small. Increase
or decrease the electrode-to-base material angle which adjusts arc area. Using a steady arc gap will reduce
the potential of short-outs.
Groove is too shallow... too deep…
and/or irregular.
The torch was not steadily operated. Torch must be operated with a steady and smooth feed to produce a
consistent groove.
Excessive slag adhesion to groove
edge.
Inadequate slag ejection. Maintain proper air pressure and flow. Air pressure should be set between 80 to
100psi in order to properly remove slag. It is important there is a sufficient volume of air (21cfm – 30cfm).
Sometimes it maybe necessary to select an air supply hose with an increased inside diameter to provide ad-
equate air volume. When gouging, keep the air stream parallel to the base material.
Gouging Torch
Air Stream
Ground Clamp
Base Material
Directio
n Of Tra
vel
Carbon Electrode
Figure 2: Gouging Basic Operation
Wear proper eye, ear, and body protection.
Shut off all power before repairing or disconnecting torch.
ELECTRIC SHOCK CAN KILL!!
Arc gouging can burn eyes and skin, avoid smoke inhalation.
It is dangerous to your health. Noise can be harmful to your hearing.
USE WITH COMPRESSED AIR ONLY, NEVER USE OXYGEN.
This product, when used for welding or cutting,
produces fumes or gases which contain
chemicals known to the State of California
to cause birth defects and, in some cases, cancer.
(California Health & Safety Code 25249.5 et. seq.)
LIT.9206 (5-09)
ABICOR BINZEL CORP. • 650 Medimmune Ct., Suite 110, Frederick, MD 21703 • 301-846-4196 • FAX: 301-846-4407 • 800-542-4867 • www.abicorusa.com