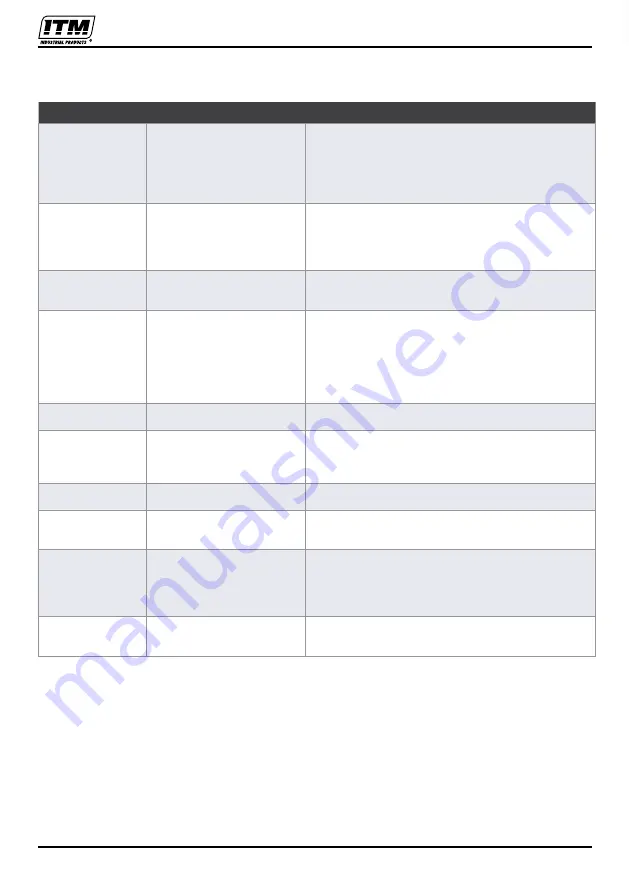
TM402-200 OPERATOR’S MANUAL
SYMPTOM
CAUSE
CORRECTIVE ACTION
Motor will not start.
1. Low Voltage.
2. Open circuit in motor or loose
connections.
3. Blown fuse or breaker.
4. Not plugged in or switched on
at wall
1. Check power source for proper voltage.
2. Inspect all lead connection on motor for loose or open
connections. (Send for Servicing.)
3. Short circuit. (Send for Servicing.)
4. Improper match between tool and circuit, fuse or breaker.
Motor will not start –
fuses or circuit
breakers tripping or
blowing.
1. Short circuit in line, cord or plug.
2. Short circuit in motor or loose
connections.
3. Incorrect fuses or circuit breakers
in power line
1. Inspect cord or plug for damaged insulation and shorted wires.
2. Inspect all connections on motor for loose or shorted terminals
and/or worn insulation.
3. Install correct fuses or circuit breakers or
switch tool to an appropriately sized circuit.
Motor overheats.
1. Motor overloaded.
2. Extension cord too long and
insufficient gauge (weight).
1. Reduce load on motor.
2. Utilize an extension cord of appropriate gauge and length or plug
tool directly into outlet.
Motor stalls (resulting
in blown fuses or
tripped circuit).
1. Short circuit in motor or loose
connections.
2. Low voltage.
3. Incorrect fuses or circuit breakers
in power line.
4. Motor overload.
1. Inspect connections on motor for loose or shorted terminals or
worn insulation. (Send for Servicing.)
2. Correct low voltage conditions (for example: improper extension
cord length and/or gauge).
3. Install correct fuses or circuit breakers or plug tool into an
appropriate circuit, matched to an appropriate fuse or breaker.
4. Reduce the load on the motor.
Machine slows when
operating.
1. Feed rate too great.
1. Reduce the rate at which the workpiece is fed into the working
area of the tool
Wavy condition on
surface of workpiece
1. Machine vibrating.
2. Workpiece is not being held firmly
3. Wheel face uneven.
4. Wheel is too hard.
1. Ensure machine is securely mounted on a solid surface.
2. Use a holding device to firmly retain the workpiece.
3. Dress the grinding wheel.
4. Use softer wheel, or reduce the feed rate.
Lines on surface of
workpiece.
1. Impurity on surface of wheel.
2. Workpiece not being held tightly
1. Dress the grinding wheel.
2. Try holding the device to more firmly retain
Burning spots or
cracks in the
workpiece.
1. Improper type of grinding wheel.
2. Improper feed rate.
1. Try wheels with softer bond or coarser grit.
2. Slow down the rate at which the workpiece is fed into the wheel.
Wheel dulls quickly, grit
falls off
1. Feed rate is too aggressive.
2. Wheel is soft.
3. Wheel diameter too small.
4. Bad wheel dressing.
5. Defective wheel bonding.
1. Decrease feed rate of workpiece into grinding wheel.
2. Select a grinding wheel with a harder bond of material.
3. Replace wheel.
4. Dress the wheel.
5. DO NOT USE – return wheel to point of purchase
Wheel clogs and
workpiece shows
burn marks.
1. Wheel is too hard.
2. Feed rate is too slow.
3. Bad wheel dressing.
1. Select a grinding wheel with a softer bond of material.
2. Increase the feed rate of the workpiece into the grinding wheel.
3. Dress the wheel.
TROUBLESHOOTING
10
www.itmtools.com.au