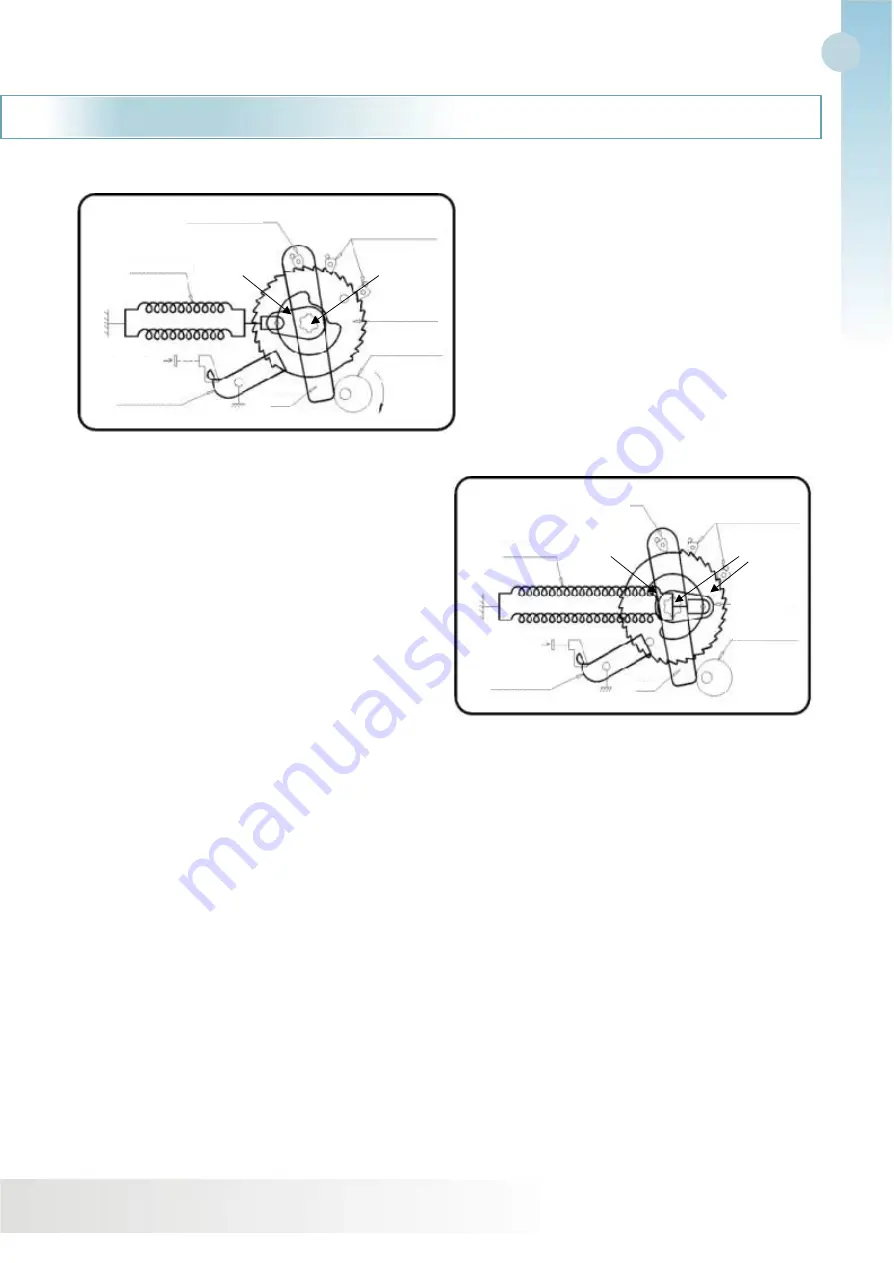
36
Initial stage
L1
Power Shaft
Fig C
Mechanism in open condition & both the springs in
discharged condition
DRIVING LATCH
LATCHES FOR HOLDING
CHARGING GEAR
SPRING CHARGING
DEVICE
ARM
CLOSING LEVER
CLOSING SPRING
CLOSING COMMAND
After Charging
L1
Fig D
Closing spring is charged, ready for closing operation
L1
DRIVING LATCH
LATCHES FOR HOLDING
CHARGING GEAR
ARM
CLOSING LEVER
CLOSING SPRING
CLOSING COMMAND
SPRING CHARGING
DEVICE
The spring charging motor charges the springs after
each closing operation until the spring-charged
indication appears. Should there be no voltage during
charging, the geared motor stops, and starts recharging
the springs automatically when the voltage is on again.
It is, however, always possible to complete the charging
operation manually. Motor supply gets cut-off
automatically as the spring gets completely charged.
1.3.2 Manual Spring Charging
For charging the Closing-springs manually, fully insert
the charging handle into the seat and rotate it clockwise
until you see the spring-charged indication.
Ensure the handle is engaged with the seat.
The force, which can normally be applied to the charging
handle, is 130 N. In any case, the maximum force
applied must not exceed 170 N. As the springs get
charged, a sound [internal latches getting engaged]
can be heard.
The arm won’t rotate the charging-gear further, since
the charging-gear has no teeth on remaining periphery.
1.4.1 Closing Operation:
Consider both the springs are in discharged condition
and breaker is open (Ref Fig. E, Page 37) In this
condition neither close nor open operation is possible
to perform on the breaker. Latch assembly (La) and
(Lb) are in released condition. The closing spring can
be charged either electrically or manually as explained
1.4 Breaker Operations:
in section1.3. During the process of charging pin
(P1) comes in contact with closing lever (Ref Fig F,
Page 37). Pin (P1) will creates pressure on closing
lever as closing spring is fully charged. Position of the
closing lever in this condition is retained by half shaft.
If close command is initiated now, it will rotate half shaft
(Ref Fig. G). Rotation of half shaft will release closing
lever and hence charging gear. Due to this spring
energy stored in closing spring acts on power shaft,
which will cause the rotation of the cam mounted on
the power shaft. Mechanism lever (Ref. Fig.G) is resting
on the outer periphery of this cam, which is directly
connected to charging shaft. Rotation of cam will push
this mechanism lever upwards, this will results in rotation
of the charging shaft. Tripping lever is mounted on
same charging shaft. One end of this tripping lever is
connected to common shaft of the breaker via link, and
another end is connected to tripping spring. Rotation of
around 90° will close the circuit breaker as well as
charging of the tripping spring.
PART C Operating Mechanism working principle & maintenance
Содержание VBF 36
Страница 1: ...Outdoor Vacuum Circuit Breaker Type VBF Instruction for Installation Service and Maintenance ...
Страница 51: ...FIG 3 TYPICAL SCHEMATIC DIAGRAM FOR VBF36 51 Drawings ...
Страница 53: ...53 Drawings Fig 4c View from Rear side Covers removed ...
Страница 58: ...58 Dismantling of Operating Coils Setup Disconnect the motor power supply 7 Fig 11 Fig 12 Motor ...