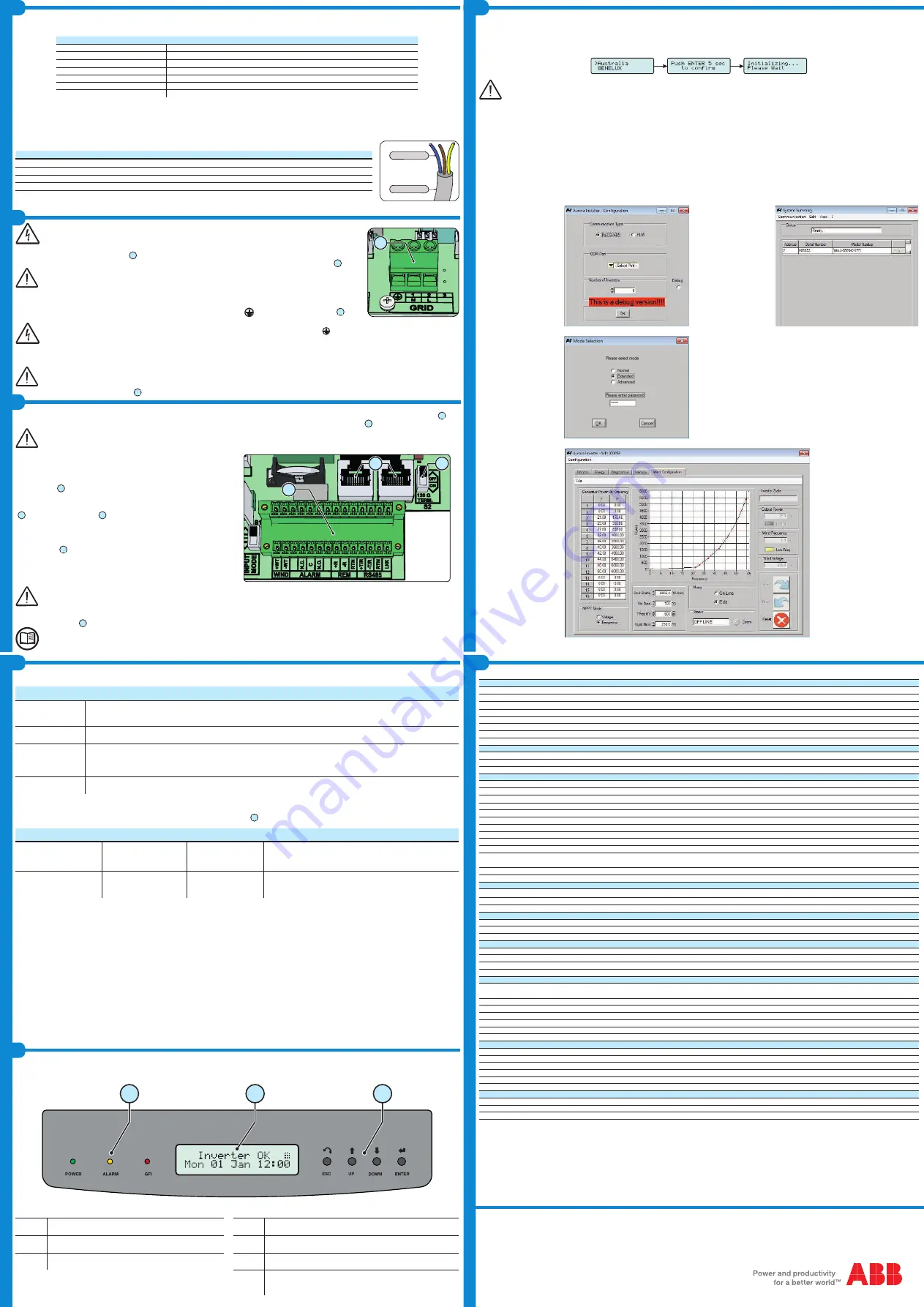
11.
Connection of the communication and control signals
12.
Commissioning
PVI-3.0_3.6_4.2-TL-OUTD-W-Quick Installation Guide EN-RevA
EFFECTIVE 2014-04-02
© Copyright 2014 ABB. All Rights Reserved.
Speciications subject to change without notice.
9.
Line cable and protection devices
10.
Output connection (AC)
14.
Instruments
15.
Characteristics and technical data
Coniguration parameter of power curve
13.
Load protection breaker (AC disconnect switch) and line cable sizing
To protect the AC connection line of the inverter, we recommend installing a device for protection against over current and leakage with the following characteristics:
PVI-3.0-TL-OUTD-W
PVI-3.6-TL-OUTD-W
PVI-4.2-TL-OUTD-W
Type
Automatic circuit breaker with differential thermal magnetic protection
Nominal Voltage
230 Vac
Nominal Current
20 A
25 A
Magnetic protection characteristic
B/C
Number of poles
2
Type of differential protection
A/AC
Differential sensitivity
300 mA
ABB declares that the ABB transformerless inverters, in terms of their construction, do not inject continuous ground fault currents and therefore there is no
requirement that the differential protection installed downstream of the inverter be type B in accordance with IEC 60755 / A 2.
Characteristics and sizing of the line cable
Three-pole cable required. The cross-section of the AC line conductor must be sized in order to prevent unwanted disconnections of the inverter from the grid
due to high impedance of the line that connects the inverter to the power supply point.
Cross-section of the line conductor (mm
2
)
Maximum length of the line conductor (mt)
PVI-3.0-TL-OUTD-W
PVI-3.6-TL-OUTD-W
PVI-4.2-TL-OUTD-W
4 mm²
19 m
16 m
14 m
6 mm²
29 m
24 m
21 m
10 mm²
48 m
41 m
35 m
16 mm²
77 m
65 m
56 m
The values are calculated in nominal power conditions, taking into account: 1. a power loss of not more than 1% along the line. 2. copper cable, with HEPR rubber insulation, laid in free air
Contact us
www.abb.com/converters-inverters
max 16 mm²
~13÷21 mm
Warning! Before performing any of the operations described below, ensure the AC line downstream the
inverter has been correctly disconnected
- Remove the protective cap on the hole
19
used to pass the AC cable into the inverter.
-
Insert an M32 cable gland (or compatible - hole diameter 33.8 mm) in the hole to be used for the AC output cable
19
Warning! To ensure environmental protection IP65 it is necessary to ix the cable gland to the inverter
chassis with the minimum tightening torque speciied in the cable gland manufacturer’s datasheet.
- Strip 10 mm of sheathing from the AC grid connection cables
- Plug the AC line cable into the inverter, passing it through the previously installed cable gland
- Connect the protective earth (yellow-green) cable to the contact labelled with the
symbol on the terminal block
10
Warning! ABB inverters should be earthed (PE) via the terminal with the protective earth label , using a cable with an appropriate cross-
section of the conductor for the maximum ground fault current that the generating system might experience
- Connect the neutral cable (normally blue) to the terminal labelled with the letter
N
- Connect the phase cable to the terminal labelled with the letter
L
Warning! The AC cables must be tightened on the terminal block with a minimum torque of 1.5 Nm
Once the connection to the terminal board
10
is complete, screw in the cable gland irmly and check the tightness.
10
Each cable which must be connected to the connectors of the communication and control signals must pass through one of the two service cable glands
20
.
An M20 cable gland (or compatible – hole diameter 20.3 mm) must be inserted in one of two of the service cable glands holes
20
.
Warning! To ensure environmental protection IP65 it is necessary to ix the cable gland to the inverter chassis with the minimum tighte-
ning torque speciied in the cable gland manufacturer’s datasheet.
Connection of the tachometer signal
The tachometer signal allows the 7200-WIND-INTERFACE-EU to drive the inver-
ter. It is therefore necessary to connect up the two cables from the 7200-WIND-
INTERFACE-EU (
WIND SPEED+
and
WIND SPEED-
) to the tachometer signal
terminal block
13
in correspondence with terminals
+WT
and
-WT
.
Connection to the RS485 communication line
The RS485 communication line (identiied by the pair of connectors RJ45
14
and by the terminal block
13
) must necessarily be connected to the
7200-WIND-INTERFACE-EU. For further details on connection of the RS485
line please see the 7200-WIND-INTERFACE-EU manual.
Using the ALARM terminal block
Terminal block
13
connecting to the conigurable relay that allows connection
of external devices which, according to the mode selected in the menu “
SET
-
TINGS > Alarm
” can, for example, signal malfunctions. The operating modes
that can be set are: Production and Alarm.
14
15
13
The ALARM contact can be used only with systems that ensure a safety isolating additional at least (supplementary insulation in relation
to the DC input voltage)
Using the REM terminal block
The REM terminal block
13
, if suitably conigured, allows the “Remote ON/OFF” function to be used: this function allows remote disconnection of the inverter from the grid
For further information regarding the coniguration and use of the communication and control signals terminal block, please see the
manual
The inverter commissioning procedure is as follows:
- Close the external switches: If the input voltage is greater than the minimum starting voltage, the inverter will start up.
-
When the inverter is turned on for the irst time you will be asked to select the “Nation” of installation. This selection allows the inverter to automatically coni
-
gure its parameters to ensure that compliance with local standards; the default language corresponding to the selected “Nation” will also be set.
Warning! After the grid standard was set you have 24 hours to make any changes to the grid standard value; 24 hours later the “Nation
Select.” functionality will be blocked, and any subsequent changes can only be made using a password provided on request by ABB
Loading the Power Curve of eolic generator
After you have set the “Nation” value, the error message “W009 Empty Table” will be displayed. This message indicates that the wind turbine power curve has
not yet been loaded into the inverter. Thus, before connecting the inverter into the power grid, you must load the curve using the Aurora Installer software.
Follow the following step-by-step procedure for upload the power curve:
-
Inverters can use a power curve deined either in terms of the input voltage to the inverter (P(Vin)) or as a function of the wind turbine frequency (P(f)). Where
a frequency power curve has been chosen (P(f)), ensure that the tachymetric signal has been correctly connected.
- Install the Aurora Installer application on your PC
-
Supply a limited input voltage to the inverter which is just suficient to start up the inverter (50V / 1A). The wind turbine itself can be used to supply this
voltage, provided it can produce at least 50V
- Connect the inverter to your PC using the PVI-USB-RS485_232 converter (for details of the connection, see the PVI-USB-RS485_232 converter manual)
- Launch the Aurora Installer application
1. In the
“Conigu-
ration”
window select
the COM port from the
pull-down menu, enter
the number of inverters
you have connected to
the PC and click OK.
2. The application will
scan the communica-
tion line looking for the
connected inverters. The
discovered inverters will
be displayed in a table.
Click
“-->”
to select the
inverter you want to
work with.
3. In the
“Mode Se-
lection”
window select
“Extended”
and enter
the following password:
05591
. Then click OK.
4. Go to the
“Wind
Coniguration”
tab: the
application will read the
power curve table in the
inverter (this will happen
even if no table has yet
been loaded, in which
case no curve will be
shown in the graph);
5. From
“Online”
mode
go to
“Edit”
mode to
compile the power curve
(see the “Parameters” ta
-
ble for information about
compiling the power
curve) Alternatively, to
load a ile in .mpp format
created previously, click
“File”
and select the
.mpp ile to load.
6. From
“Edit”
mode go to
“On Line”
mode again and click
“Send”
to send the table to the
inverter.
Note: If you want to apply the
same curve to more than one
inverter, click “File” and “Save
As” to export the curve to your
PC in .mpp format so that it is
available for other inverters.
The following parameters must be provided, with the power curve, by turbine’s manufacturer. See table below for more details about the parameters:
PARAMETERS
Output Power Ramp
(Pout Ramp)
This is the response speed of the inverter, i.e. how quickly the take-off point of the inverter follows the take-off point of the turbine.
The value must be between 275 W/sec and 10,000 W/sec. In the commissioning phase of the system, if an instability is detected, try
reducing the “Pout Ramp” value.
Inverter Activation
Voltage (Vin Start)
This is the input voltage above which the inverter connects to the grid. The value must be between 50V and 200V.
Undervoltage
protection time
(Tprot UV)
This is the length of time the inverter remains switched on after the voltage has dropped below the “Vin Start” value. This parameter
allows you to keep the inverter connected to the grid even if the input voltage drops below ”Vin Start”. It can then start exporting ener
-
gy again to the grid whenever the wind pickups, without having to repeat the inverter start-up process. The value must be between 1
sec and 3600 sec.
Nominal Grid Voltage
(Vgrid Nom)
Indicates the rated voltage of the grid to which the inverter is connected.
-
After having loaded the wind turbine power curve, the message “Inizializing...Please Wait” is displayed. Depending on the input voltage value, the inverter will
show various messages on the display and change the behaviour of the three LED
06
:
INPUT VOLTAGE
DISPLAY MESSAGE
LED STATUS
DESCRIPTION
Vin < Vstart
Waiting Wind
Green = FLASHING
Yellow = OFF
Red = OFF
The input voltage is not suficient to permit connection to the grid.
Vin > Vstart
Missing Grid
Green = FLASHING
Yellow = ON
Red = OFF
There is suficient input voltage to permit connection to the grid:
the inverter waits until there is grid voltage to carry out the parallel
connection.
The inverter is powered ONLY by the voltage coming from the wind power system: presence of grid voltage alone IS NOT SUFFICIENT to permit the
inverter to start up.
-
With the inverter in “Missing Grid” status, close the AC switch downstream the inverter so as to supply the grid voltage to the inverter: the inverter performs the
grid voltage check, measures the wind power system insulation resistance against earth and carries out other self-diagnosis checks. During the checks before
the parallel with the grid, the green LED keeps lashing, the others are off.
During the grid voltage check and measurement of the insulation resistance, the values for the grid voltage and frequency and the insulation resi
-
stance measured by the inverter are shown on the display. The inverter completes parallel connection with the grid SOLELY if the grid parameters
meet the ranges provided for by the regulations in force and if the insulation resistance is greater than 1Mohm.
- If the preliminary checks for parallel connection to the grid are successful, the inverter connects to the grid and begins to export power to the grid. At this stage,
the display shows the inverter’s parameters in cycles. The green LED stays lit whereas the others are off.
LEDs and BUTTONS
, in various combinations, can be used to view the status or carry out complex actions that are described more fully in the manual.
08
07
06
LED
POWER
GREEN
On if the inverter is working correctly. Flashes when
checking the grid or if there is insuficient wind.
ESC
It is used to access the main menu, to go back to the previous menu
or to go back to the previous digit to be edited
LED
ALARM
YELLOW
The inverter has detected an anomaly. The anomaly
is shown on the display.
UP
It is used to scroll up the menu options or to shift the numerical scale
in ascending order
LED
GFI
RED
Ground fault on the DC side of the PV generator. The
error is shown on the display.
DOWN
It is used to scroll down the menu options or to shift the numerical
scale in descending order
ENTER
It can be used to conirm an action, to access the submenu for the
selected option (indicated by the > symbol) or to switch to the next
digit to be edited
PVI-3.0-TL-OUTD-W
PVI-3.6-TL-OUTD-W
PVI-4.2-TL-OUTD-W
Input
Absolute Maximum Input Voltage (V
max,abs
)
600 V
Input Activation Voltage (V
start
)
50 V (adj. 50...350 V)
Input Operating Range (V
dcmin
...V
dcmax
)
50...580 V
Input DC Voltage Range (V
min
,f ... V
max
,f) at P
acr
160...530 V
120...530 V
140...530 V
Maximum DC Input Current (I
dc max
)
20.0 A
32.0 A
32.0 A
Maximum Input Short Circuit Current
25 A
40.0 A
40.0 A
Maximum Backfeed current (from AC to DC side)
Negligible
DC Connection Type
Screw terminal block
Input protection
Reverse Polarity Protection
Yes, from limited current source
Input Overvoltage Protection - Varistor
2
Photovoltaic Array Isolation Control
According to local standard
Output
AC Grid Connection Type
Monophase
Rated AC Power (P
acr
)
3000 W
3600 W
4200 W
Maximum AC Output Power (P
ac max
)
3300 W
(1)
4000 W
(2)
4600 W
(3)
Rated AC Grid Voltage (V
acr
)
230 V
AC Voltage Range
180...264 Vac
(4)
Maximum AC Output Current (I
ac max
)
14.5 A
17.2 A
(5)
20.0 A
Inrush Current
Negligible
Maximum Output Fault Current
<25 A rms (100mS)
Rated Output Frequency (f
r
)
50 Hz
Output Frequency Range (f
min
...f
max
)
47...53 / 57...63 Hz
(6)
Nominal Power Factor (Cosphi
acr
)
>0.995 adj. ± 0.9 with Pacr=
3.0 kW
>0.995 adj. ± 0.9 with Pacr=
3.6 kW
>0.995 adj. ± 0.9 with Pacr=
4.2 kW
Total Harmonic Distortion of Current
< 3.5%
AC Connection Type
Screw terminal block
Output protection
Anti-Islanding Protection
According to local standard
Maximum AC Overcurrent Protection
16.0 A
19.0 A
22.0 A
Output Overvoltage Protection - Varistor
2 (L - N / L - PE)
Operating performance
Maximum Eficiency (η
max
)
96.8%
Power Input Treshold
10.0 W
Stand-by Consumption
< 8.0 W
Communication
Wired Local Monitoring
PVI-USB-RS232_485 (opt.)
Remote Monitoring
WIFI LOGGER CARD (opt.), PVI-AEC-EVO (opt.), VSN700 Data Logger (opt.)
Wireless Local Monitoring
WIFI LOGGER CARD (opt.)
User Interface
LCD Display with 16 characters x 2 line
Environmental
Ambient Temperature Range
-25...+60°C /-13...140°F with
derating above 50°C/122°F
-25...+60°C /-13...140°F with
derating above 55°C/131°F
-25...+60°C /-13...140°F with
derating above 50°C/122°F
Storage Temperature
-40...80°C (-40...+176°F)
Relative Humidity
0...100% condensing
Environmental pollution classiication for external environment
3
Noise Emission
< 50 dB(A) @ 1 m
Maximum Operating Altitude without Derating
2000 m / 6560 ft
Environmental Category
External
Physical
Environmental Protection Rating
IP 65
Cooling
Natural
Dimension (H x W x D)
618 x 325 x 222 mm / 24.3 x 12.8 x 8.7 inch
Weight
17.5 kg / 38.6 lb
Mounting System
Wall bracket
Overvoltage Category in accordance with IEC 62109-1
II (DC input) III (AC output)
Safety
Isolation Level
Transformerless (TL)
Safety Class
I
Marking
CE (50Hz only)
1. Limited to 3000 W for Germany
2. Limited to 3600 W for Germany
3. Limited to 4200 W for Germany
4. The AC voltage range may vary depending on speciic country grid standard
5. Restricted to 16 A (up to the maximum output power of 3680 W) for the standard UK G83/1.
6. The Frequency range may vary depending on speciic country grid standard
Remark. Features not speciically listed in the present data sheet are not included in the product