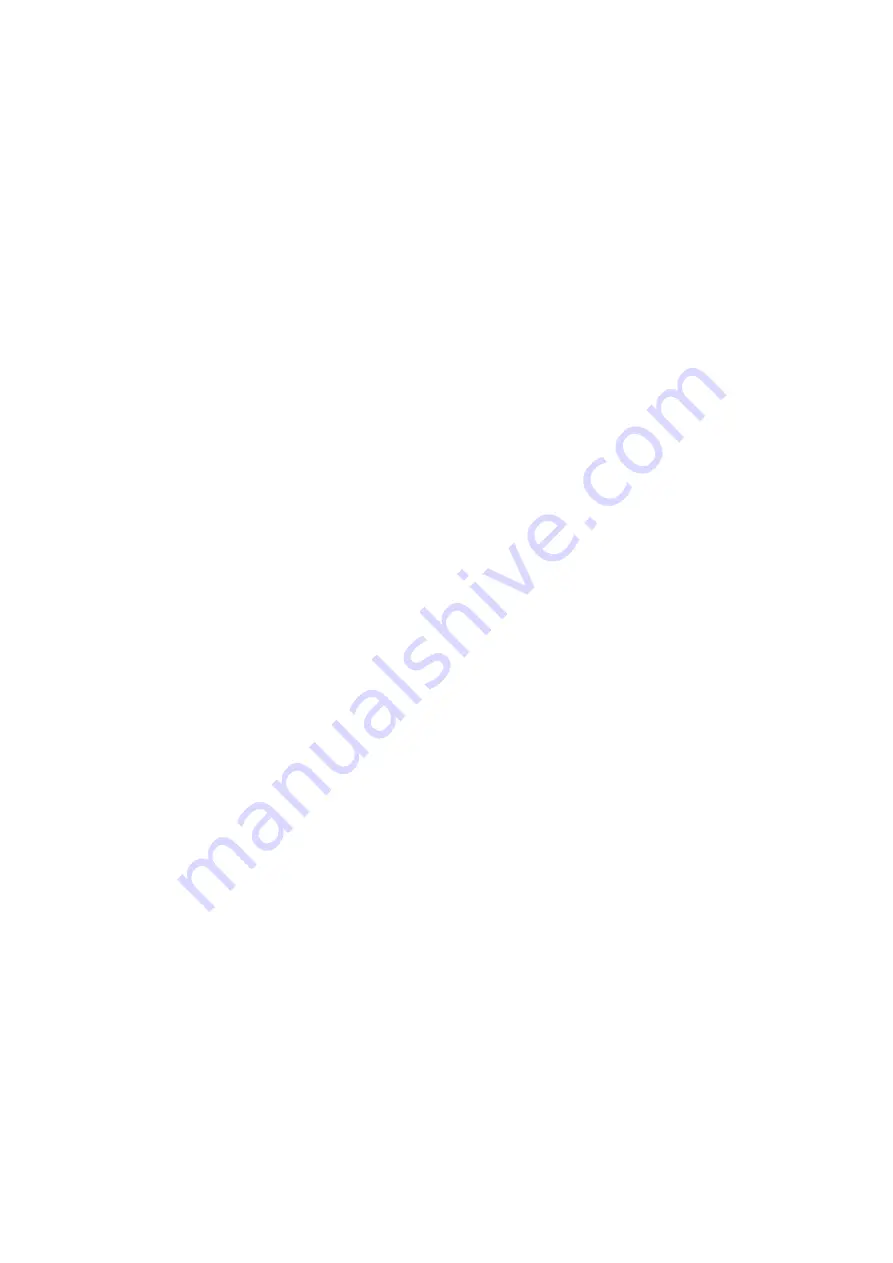
Operation
21
Configuration Instructions
A description which specifies the size of the required storage
areas is required for error-free cyclic data transmission to/from the
devices, in addition to the slave-specific parameter information. --
This slave-specific description is called PROFIBUS configuration.
- -
When the slave is changed over to cyclic data transmission, the
data blocks defined in the slave-specific configuration are
transmitted as input and output data bytes on the bus. ---This
means that the size of the data blocks is an important factor -
besides the transmission rate - which determines how often data
exchange with all bus stations is performed. - The smaller the
transported data packages are, the more often a station can be
contacted. -
The data blocks are built up from the modules specified in the
device database file (GSD file). These modules are split up in
three groups: - The first group contains all modules defining the
size of the input data blocks, the second group is made up of all
modules specifying the size of the output data blocks, and the
third groups comprises the modules for acyclic transmission. -
It is recommended to calculate the required sizes for the input and
the output data from the data types of the cyclically read or written
variables when combining the necessary modules. -- -
The configuration data can then be derived from the individual
modules. - It is recommended to calculate a reserve for the input
data, since it may turn out in the commissioning phase that more
data is needed from the connected devices. -
The modules for the input and output data blocks can be
combined in an arbitrary order when selecting them using the
device database and a configuration tool. -- Therefore, it is
recommended to select first all modules for the input data block
and then all modules for the output data block, to obtain an open
structure. The configuration can then be extended at a later time
by simply adding modules. The configuration tool used
determines the efforts required for this task.
If the configuration consists of an arbitrary combination of input
and output data blocks, the DP master and the DP slaves form
input and output groups of them. - ----- From this result the sizes
of the individual input or output data blocks.
When the configured data blocks are bigger than defined by the
indices in the parameter definitions for a slave, the connected
device will nevertheless accept this constellation. -
However, data blocks that are too small and insufficient for data
exchange with the configured variables are considered as
erroneous and will be rejected. -- In the commissioning phase, no
cyclic data transmission will be performed. Instead, the
PROFIBUS-DP master receives the respective diagnostic data.
No change-over to cyclic data transmission takes place. ----
Example
Cyclic transmission between a master and a slave is to be
established. For this purpose, 26 bytes are transmitted from a
slave to a master (input data), and the master cyclically returns 1
byte to the slave (output data). The necessary storage areas for
one read service and one write service are reserved. -----
The sizes of 26 bytes (input data) and 1 byte (output data) would
have resulted from the slave-specific parameter definitions. -
In reality, 48 bytes are given for the input data (can be extended at
a later time by setting the parameters accordingly), and 2 bytes
are given for the output data.
These data blocks are written in the configuration, in the order
read service, write service, output data, and input data. -
Usually, a byte-by-byte definition is used for slave-specific
PROFIBUS-DP configuration data. --
A possible configuration would be:
Cfg_Data = 0xC1, 0x03, 0x09, 0x03, 0xC1, 0x07, 0x05, 0x01,
0x60, 0x5F, 0x57
This configuration is built up from the following modules:
Module Data bytes
Read service
0xC1, 0x03, 0x09, 0x03
Gives a storage area of 4 bytes for the acyclic read
service as request and 10 bytes as response.
Write service
0xC1, 0x07, 0x05, 0x01
Gives a storage area of 8 bytes for the acyclic write
service as a request and 6 bytes as the response.
Output
data
0x60
Gives a storage area of 1 word or 2 bytes .
Input
data
0x5F, 0x57
Gives a storage area of 16 words or 32 bytes (0x5F) and
an area of 8 words or 16 bytes (0x57). Since the
PROFIBUS-DP module sums up these parts, a
total of 48 bytes is available for input data. ----
Refer to DIN 19245 Part 3 for the exact meaning and function of
the individual bytes.
Peculiarities
Some configuration tools for PROFIBUS-DP systems do not
permit the definition of slave-specific configuration data as
described above. -- Systems using such tools derive the
necessary configuration data from the data of the connected
controllers. - The respective setting for the size of the input and
output data blocks is read from the configuration in this case. -- -
When the DP master integrates a new station in the DP
communication system, first the configuration data is read, then
the slave-specific parameters are defined, and then the
configuration data is returned to the station. ---