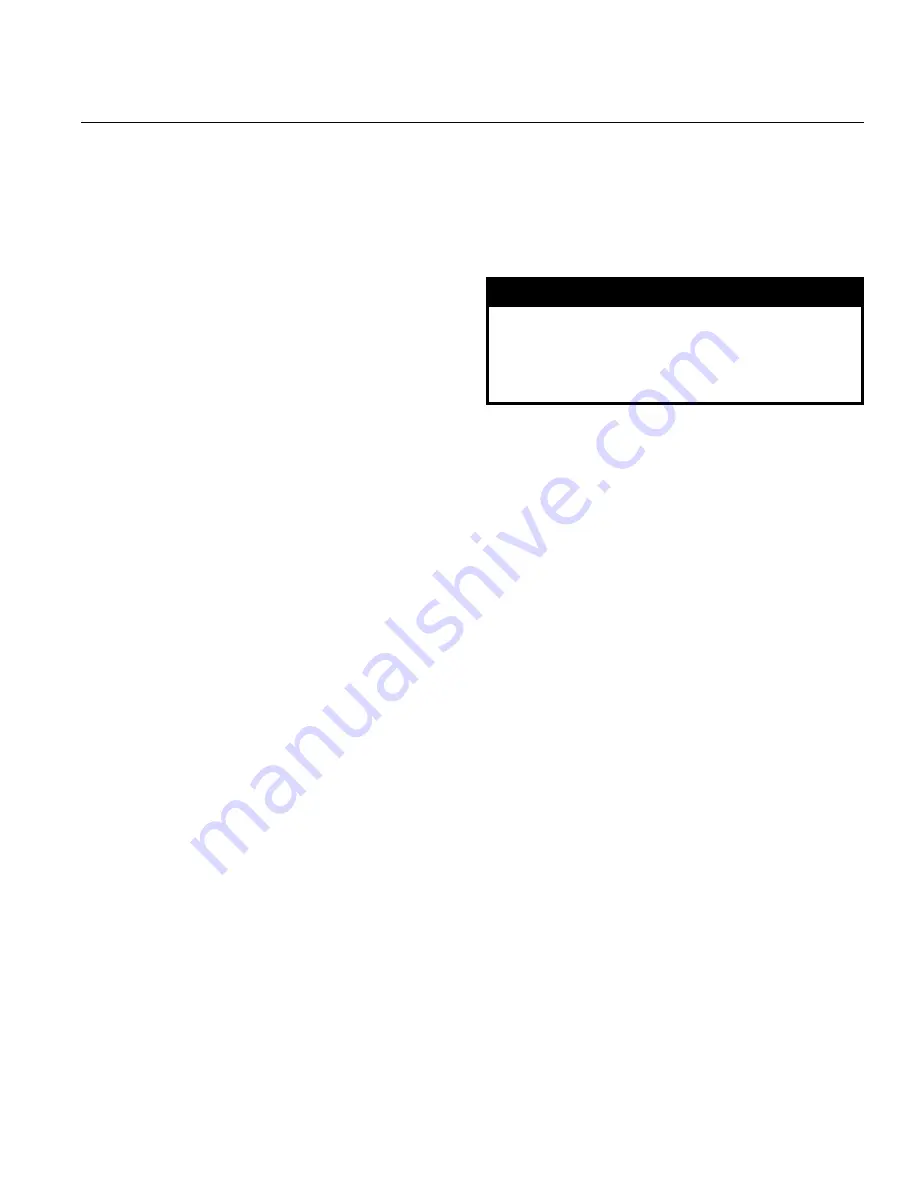
IB 6.2.11.1-2C
Page 11
ABB
5. With the local or remote close signal still applied, the
anti-pump feature of the SSCD “locks out” the close
coil. In doing so, the circuit breaker mechanism will not
pump should it close into a faulted circuit.
6. The circuit breaker can be tripped electrically by
operation of remote trip control or by operating the
optional local electric trip push button. When tripped in
this manner, the trip coil is energized through the
SSCD and the auxiliary switch "a" contact, which
releases the stored energy in the contact and opening
springs, thereby opening the breaker.
7. Tripping the circuit breaker opens the “a" contacts
and closes the “b” contacts of the auxiliary switch. At
that point, the motor circuit is once again complete and
the motor will charge the closing springs.
CLOSING SPRING OPERATION
The two closing springs supply the power that closes
the circuit breaker and also charge the two opening
springs during the closing operation. The closing
springs are charged by a motor in the electrically
operated breaker and charged by hand in the manually
operated breaker; however, in either type the springs
are charged the same amount and, when charged, the
spring energy is available to close the breaker, thus
referred to as "stored energy". In electrically operated
models, the closing springs are normally charged when
the breaker is opened. If charged after closing, (by
using the manual handle) the breaker may be opened
and then reclosed without recharging the springs. The
closing springs are automatically discharged when the
breaker is moved from the disconnected to the
withdrawn position. This prevents accidental discharge
and closing.
INSTALLATION, INITIAL TESTING, AND
REMOVAL
For initial installation of breakers in the "CONNECTED"
position, the supply for the primary circuit should be de-
energized. Testing of the breaker must be done in the
test position.
Installation (See Figure 1)
The circuit breaker must be in the “OPEN” position, the
racking crank (8, Figure 1) when inserted in opening is
rotated counterclockwise until the racking cam roller
(19) is rotated down into a 45" angle, and the motor
disconnect switch (14) for electrically operated circuit
breakers is in the "OFF” position. NOTE: Lever (11)
must be pushed down to permit the rotation of crank
(8).
Open compartment door and lower the right and left
hand track extensions to their fully extended position.
Use lifting yoke (9, Figure 1 ), which is inserted in holes
in the upper rear frame, and lower the circuit breaker
wheels (7) onto the track extensions. Remove lifting
yoke. Push circuit breaker into compartment until
racking cam rollers (19) stop against their guides.
If breaker will not insert fully, check to insure that the
breaker rating matches that of the intended cubicle.
Interference blocking is provided to prevent installation
of a breaker into an incorrectly rated cell.
CAUTION CAUTION CAUTION CAUTION
RAISE TRACK EXTENSIONS INTO COMPARTMENT
PRIOR TO RACKING THE CIRCUIT BREAKER.
Insert racking crank (8, Figure 1) into opening and
depress drawout lever (11). Turn crank clockwise until
automatically stopped. Breaker is now in
"DISCONNECT" position. If the cubicle door is closed
the label on the right side of the escutcheon (5) will
show “DISCONNECT".
Again depress drawout lever (11) and turn crank
clockwise until automatically stopped. Breaker is now
in “TEST” position.
Checking Circuit Breaker Operation in “TEST”
Position (Manually Operated Models) (See Figure 1)
a. Manually reset automatic trip indicator (15) if it
protrudes approximately 1/2 ". Push in to reset.
b. Charge and close circuit breaker; See “Manual
Closing Operation" below.
c. Trip by manual "TRIP" button (10).
d. Check each auxiliary device for proper operation.
Checking Circuit Breaker Operation in
"CONNECTED" Position
After completing check procedures in “TEST” position,
WARNING WARNING WARNING WARNING
DO NOT REMOVE THE INTERFERENCE
BLOCKING IN AN EFFORT TO ALLOW CIRCUIT
BREAKER RACKING. RISK TO PERSONNEL AND
SERIOUS DAMAGE TO THE CIRCUIT BREAKER
AND CUBICLE CAN RESULT.
Содержание K-Line Plus KP-32
Страница 20: ...IB 6 2 11 1 2C Page 20 ABB NOTES ...
Страница 21: ...IB 6 2 11 1 2C Page 21 ABB NOTES ...