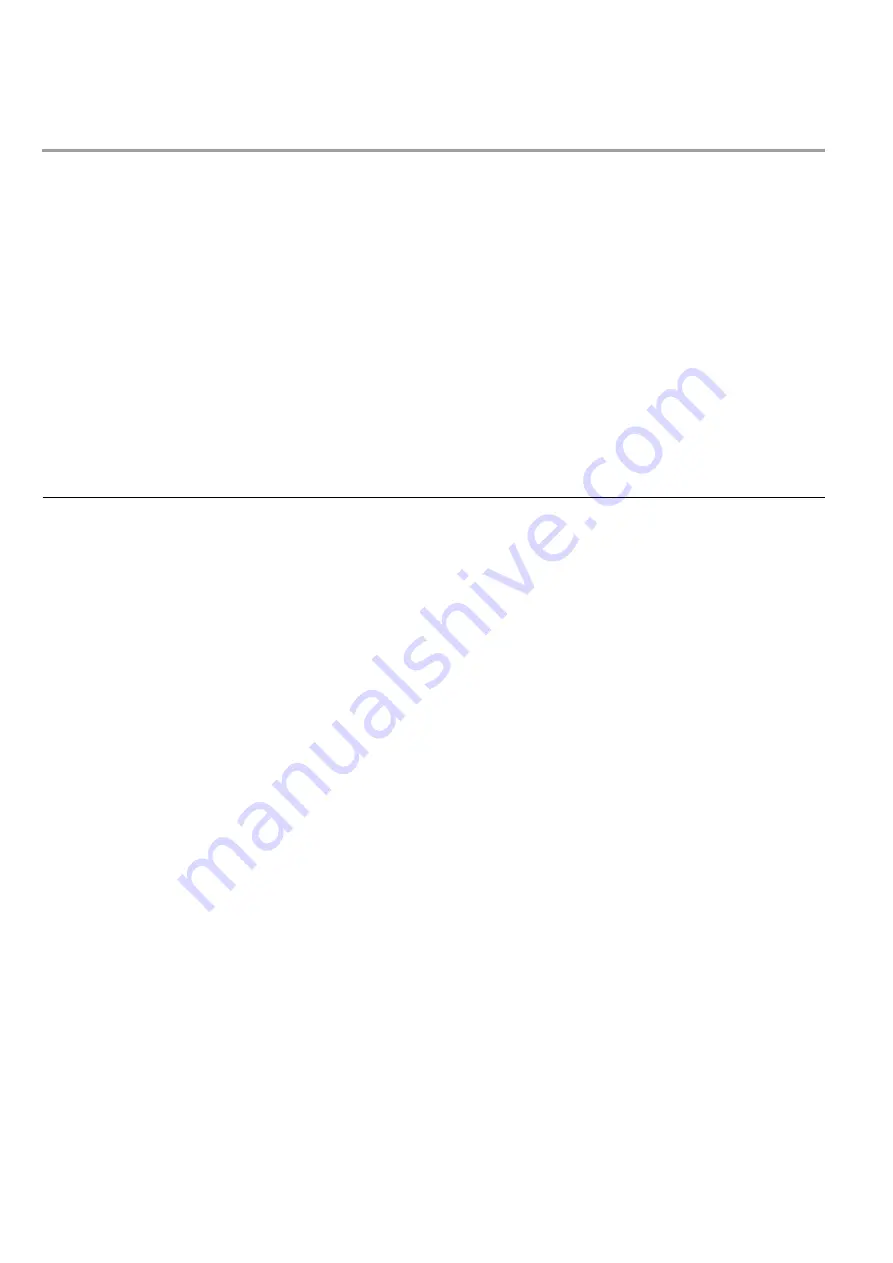
0
Heat exchangers
In addition to the usual maintenance operations
for standard motors which have been previously
described, the totally-enclosed motors need a
supplementary maintenance program, due to
their special construction and operation: Sug-
gested activities are given below:
Check the housing (Figure 24, item 9) for paint
damage. Repair paint damage to protect
against corrosion. For information regarding
paint contact ABB.
Check fan motor (Figure 24, item 10) for unusual
noise and replace bearings if necessary. (The
fan motor is normally fitted with permanently
greased bearings free of maintenance). Keep
the motor clean and ensure free ventilation air-
flow.
Check gaskets for leakage monthly. Gaskets
need to be replaced every 2 years.
Change the air filter of the cooling air circuit
every time DC-motor brushes are changed.
If the heat exchanger is provided with a filter
monitoring device, normal pressure drop when
the filter must be changed is 200 Pa (normal set
point for filter monitor higher due to measuring
over the cooling coil and the filter). Use filter
type EU3 according to Eurovent 4/5 or similar
filter with efficiency 85% according to Ashrae
52-76. Do not use a filter with higher efficiency
due to its higher pressure drop.
Remark
Note that the filter material has a different struc-
ture on each side. The side with the coarser
structure is to be placed outward.
Check leakage air filter every month during first
time of operation and change if clogged.
Due to its position, where pressure in the in-
ner air circuit is lowest, the leakage air filter will
provide substitute air if an unwanted leak has
occurred somewhere else in the air circuit.
Rapid clogging of the leakage air filter indicates
that an unwanted leak is present. If so, do the
necessary tightening and change the filter. Nor-
mally use the same filter as above.
In environments with harmful contaminations,
use filter EU5 according to Eurovent 4/5 or simi-
lar filters with efficiency 90-95% according to
Ashrae 52-76.
In DC-motor heat exchangers with internal air
circuit protected by leakage air filter, the outer
surface of the cooling coil normally does not
have to be cleaned. If exceptional cases, dry
deposits can be cleaned by cautious use of
compressed air. For greasy deposits use a de-
tergent and rinse with water.
Normally cleaning the inside of tubes in the
water flow circuit is not necessary but in areas
with heavy polluted water, use a filter in the
water distribution system is recommended. If,
after long service, the heat exchanger appears
to have decreased capacity, the tubes can be
cleaned inside by re-circulation of water with
the appropriate cleaning compound. Knowledge
about type of contamination and appropriate
cleaning compound will highly benefit efficiency
of such cleaning procedure. For most deposits
use of warm water is to be preferred.
Note:
• The tubes in the standard heat exchanger
cannot be mechanically cleaned on the
inside.
• To avoid corrosion, choose a cleaning agent
that does not harm the tube material.
• The standard tube material is copper.
When the cooling coil is not in operation, pro-
tect it from damage due to corrosion or freezing
in sub-zero temperatures by draining it off.
Maintenance of
motors with heat
exchangers
Special main-
tenance of air-
water heat
exchangers
Содержание DC Machines DMI
Страница 1: ...DC Machines DMI Operating and Maintenance Instructions ...
Страница 2: ... ...
Страница 9: ... Machine description ...
Страница 46: ...46 EC Directives Declaration of Incorporation ...
Страница 47: ...47 EC Directives EC Declaration of Conformity ...