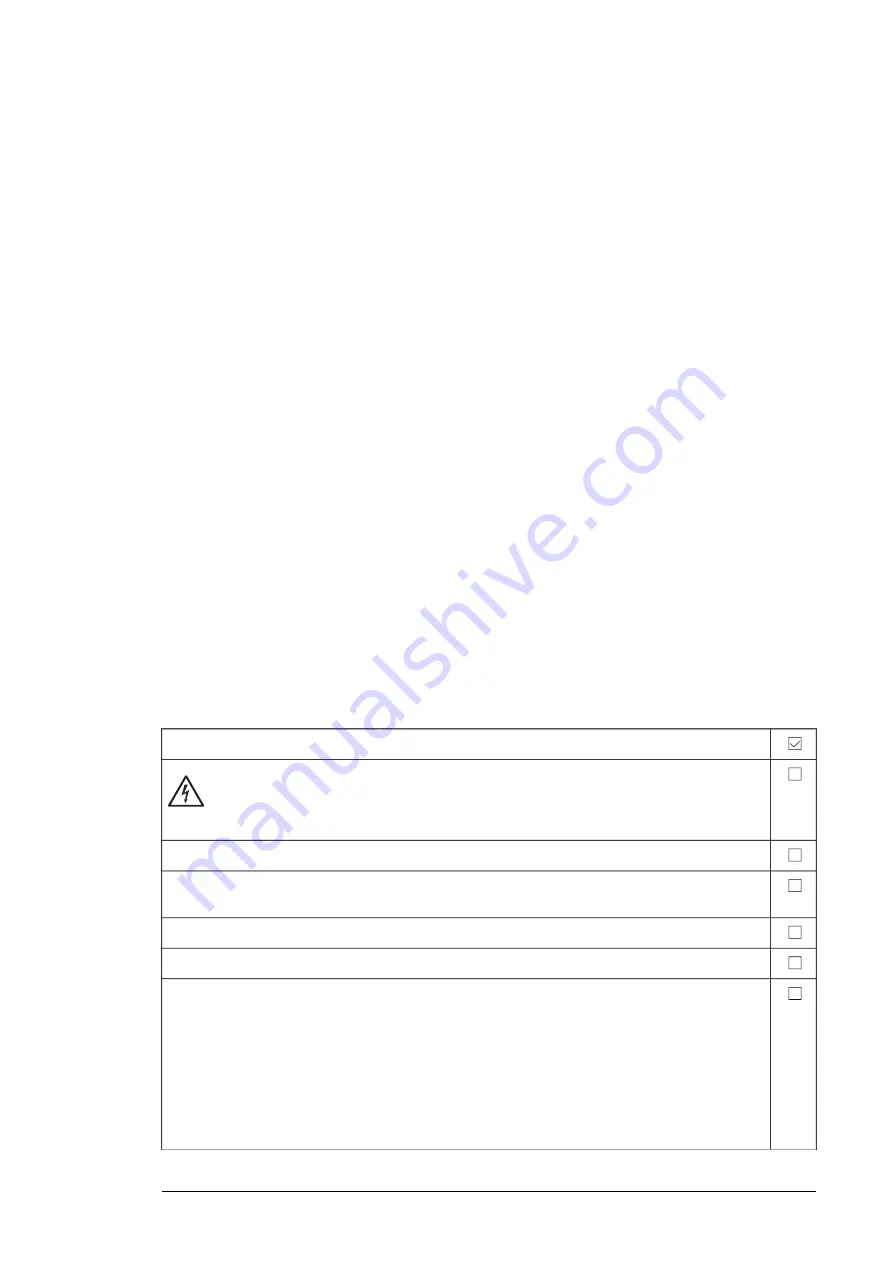
Start-up including validation test
To ensure the safe operation of a safety function, validation is required. The final assembler
of the machine must validate the function by performing a validation test. The test must be
performed
• at initial start-up of the safety function
• after any changes related to the safety function (circuit boards, wiring, components,
settings, etc.)
• after any maintenance work related to the safety function
• after a drive firmware update.
■
Competence
The validation test of the safety function must be carried out by a competent person with
adequate expertise and knowledge of the safety function as well as functional safety, as
required by IEC 61508-1 clause 6. The test procedures and report must be documented
and signed by this person.
■
Validation test reports
Signed validation test reports must be stored in the logbook of the machine. The report shall
include documentation of start-up activities and test results, references to failure reports
and resolution of failures. Any new validation tests performed due to changes or maintenance
shall be logged into the logbook.
■
Validation test procedure
After wiring the Safe torque off function, validate its operation as follows.
Note:
If the drive is equipped with safety Q972, +Q973 or +Q982, also do the
procedure shown in the FSO-xx module documentation.
Action
WARNING!
Obey the safety instructions. If you ignore them, injury or death, or damage to the equipment
can occur.
Make sure that the drive can be run and stopped freely during start-up.
Stop the drive (if running), switch the input power off and isolate the drive from the power line using a
disconnector.
Check the STO circuit connections against the wiring diagram.
Close the disconnector and switch the power on.
Test the operation of the STO function when the motor is stopped.
•Give a stop command for the drive (if running) and wait until the motor shaft is at a standstill.
Make sure that the drive operates as follows:
•Open the STO circuit. The drive generates an indication if one is defined for the 'stopped' state in
parameter
31.22
(see the firmware manual).
•Give a start command to verify that the STO function blocks the drive's operation. The drive generates
a warning. The motor should not start.
•Close the STO circuit.
•Reset any active faults. Restart the drive and check that the motor runs normally.
The Safe torque off function 223
Содержание ACS880-14
Страница 1: ...ABB INDUSTRIAL DRIVES ACS880 14 drive modules 132 400 kW 200 400 hp Hardware manual...
Страница 2: ......
Страница 4: ......
Страница 14: ...14...
Страница 24: ...24...
Страница 30: ...30...
Страница 54: ...54...
Страница 64: ...64...
Страница 98: ...98...
Страница 114: ...With twin connectors in the control panel holder 1 2 3 1 114 Electrical installation...
Страница 115: ...With FDPI 02 modules OPEN TERMIN ATED 1 1 2 2 OPEN TERMINATED 3 Electrical installation 115 11...
Страница 142: ...4 5 6 3 3 1 1 1 1 2 142 Installation example with full cabling panels option H381...
Страница 150: ...150 Installation example with full cabling panels option H381...
Страница 156: ...156...
Страница 204: ...Standard configuration 204 Dimension drawings...
Страница 205: ...Location of power cable connection terminals with options H370 H356 3AXD50000038012 Dimension drawings 205...
Страница 206: ...Drive module with options 0B051 H356 0H371 206 Dimension drawings...
Страница 207: ...Configuration with option H381 3AXD50000323210 Dimension drawings 207...
Страница 208: ...LCL filter module 208 Dimension drawings...
Страница 212: ...External control unit 3AXD50000011687 212 Dimension drawings...
Страница 230: ...Declaration of conformity 230 The Safe torque off function...
Страница 236: ...Combi screw M8 30 Hex 20 N m 14 75 lbf ft Tapping screw M6 12 Torx T30 Hex 8 N m 71 lbf in 8 10 9 11 12 236...
Страница 241: ...241...
Страница 246: ...246...