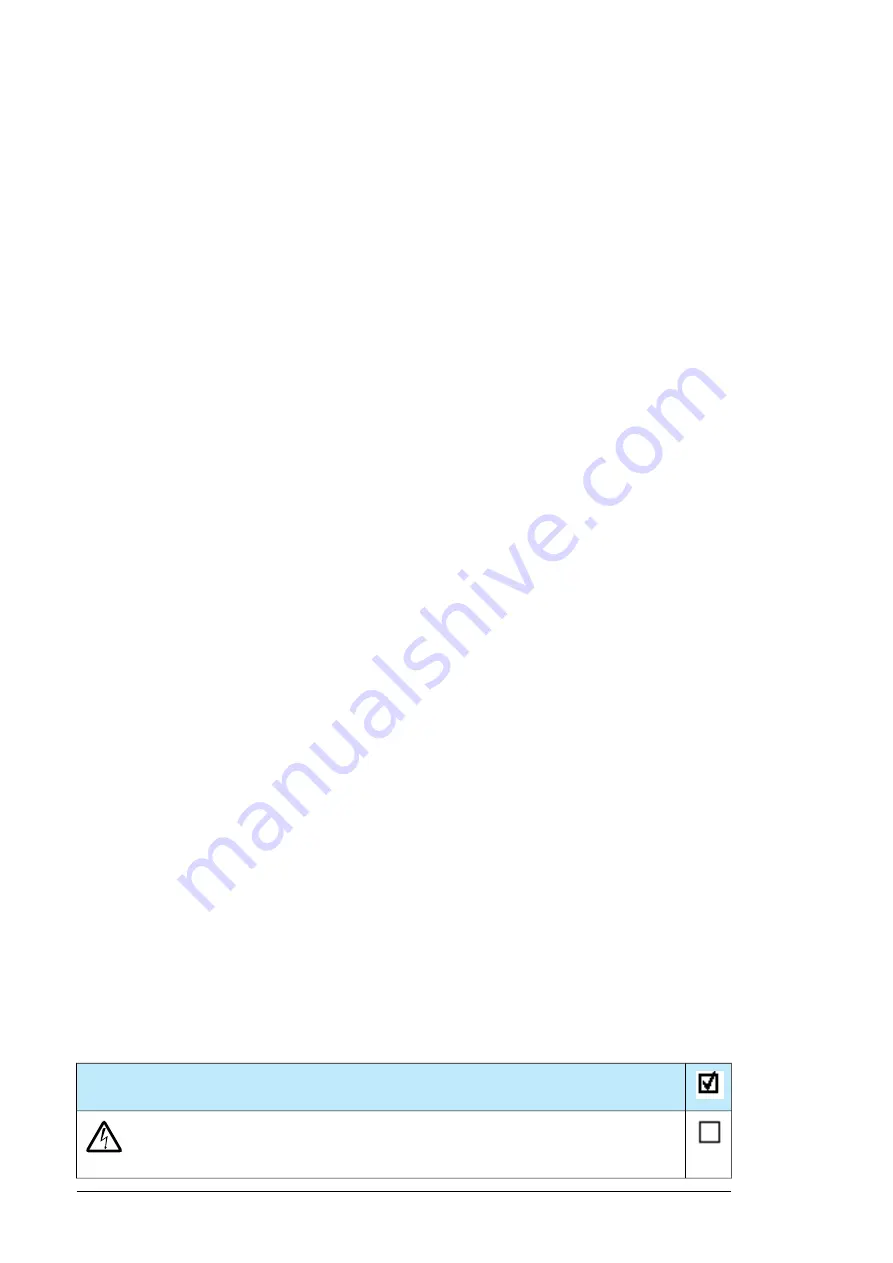
Operation principle
1.
The Safe torque off activates (the activation switch is opened, or safety relay contacts
open).
2.
The STO inputs on the inverter control unit de-energize.
3.
The control unit cuts off the control voltage from the inverter IGBTs.
4.
The control program generates an indication as defined by parameter
31.22
(refer to
the firmware manual of the inverter).
5.
Motor coasts to a stop (if running). The inverter cannot restart while the activation switch
or safety relay contacts are open. After the contacts close, a new start command is
required to start the drive.
Start-up including acceptance test
To ensure the safe operation of a safety function, validation is required. The final assembler
of the machine must validate the function by performing an acceptance test. The acceptance
test must be performed
•
at initial start-up of the safety function
•
after any changes related to the safety function (circuit boards, wiring, components,
settings, etc.)
•
after any maintenance work related to the safety function.
■
Competence
The acceptance test of the safety function must be carried out by a competent person with
adequate expertise and knowledge of the safety function as well as functional safety, as
required by IEC 61508-1 clause 6. The test procedures and report must be documented
and signed by this person.
■
Acceptance test reports
Signed acceptance test reports must be stored in the logbook of the machine. The report
shall include documentation of start-up activities and test results, references to failure reports
and resolution of failures. Any new acceptance tests performed due to changes or
maintenance shall be logged into the logbook.
■
Acceptance test procedure
After wiring the Safe torque off function, validate its operation as follows.
Note:
If the drive is equipped with safety Q951, do the procedure shown in the
documentation of the option.
Note:
All inverter modules of the inverter unit must be powered and connected to the STO circuit
during the acceptance test.
Action
WARNING!
Follow the safety instructions given in
. Ignoring the instructions can cause
physical injury or death, or damage to the equipment.
196 The Safe torque off function
Содержание ACS880-07CLC
Страница 1: ...ABB industrial drives Hardware manual ACS880 07CLC drives ...
Страница 2: ......
Страница 4: ......
Страница 64: ...64 ...
Страница 82: ...82 ...
Страница 91: ...PE PE 10 13 12 22 Electrical installation 91 ...
Страница 122: ...122 ...
Страница 124: ...124 ...
Страница 132: ...5 4 11 7 6 8 132 Maintenance ...
Страница 133: ...14 15 16 12 13 17 Maintenance 133 ...
Страница 141: ...5 Set the real time clock Maintenance 141 ...
Страница 142: ...142 ...
Страница 150: ...150 ...
Страница 176: ...ACS880 07CLC 0390A 7 C121 marine construction 176 Dimensions ...
Страница 177: ...ACS880 07CLC 1310A 7 Dimensions 177 ...
Страница 178: ...ACS880 07CLC 2180A 7 C121 marine construction 178 Dimensions ...
Страница 179: ...ACS880 07CLC 3260A 7 C121 marine construction Dimensions 179 ...
Страница 181: ... 2 D8D Dimensions 181 ...
Страница 182: ... 3 D8D 182 Dimensions ...
Страница 183: ... 4 D8D Dimensions 183 ...
Страница 185: ...Inverter module cubicle with two R8i modules bottom cable exit Dimensions 185 ...
Страница 186: ...Inverter module cubicle with three R8i modules bottom cable exit 186 Dimensions ...
Страница 187: ...Brake chopper cubicle D150 Dimensions 187 ...
Страница 188: ...188 ...
Страница 202: ...202 ...
Страница 211: ......
Страница 212: ......
Страница 214: ...Contact us www abb com drives 3AXD50000131457 Rev A EN EFFECTIVE 2018 03 09 3AXD50000131457A ...