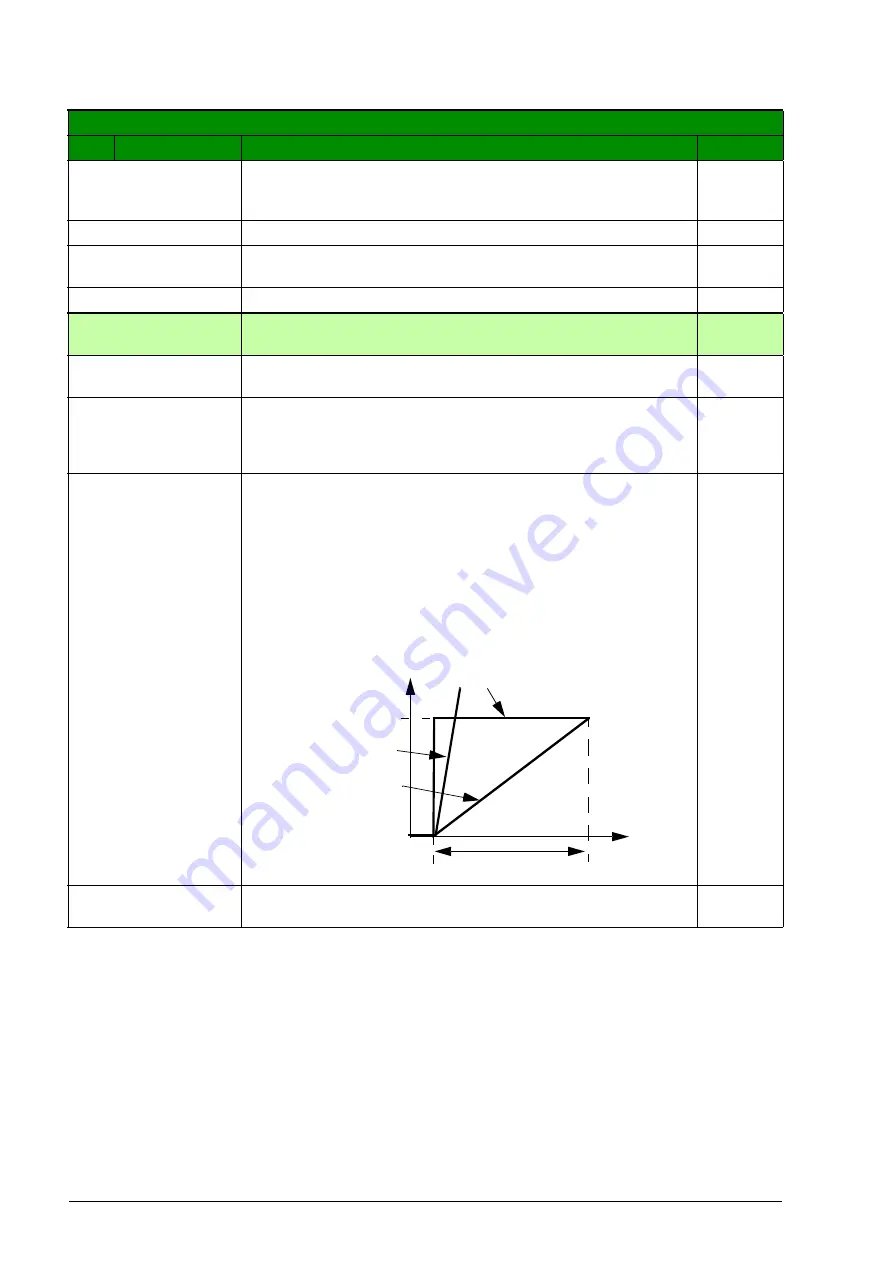
236 Actual signals and parameters
3717 LOAD TORQ
LOW 5
Defines the torque value of the fifth underload curve
definition point. Must be smaller than
.
30%
0…600%
Torque
1 = 1%
3718 LOAD TORQ
HIGH 5
Defines the torque value of the fifth overload curve definition
point
300%
0…600%
Torque
1 = 1%
40 PROCESS PID
SET 1
Process PID (PID1) control parameter set 1. See section
on page
.
4001 GAIN
Defines the gain for the process PID controller. High gain
may cause speed oscillation.
1.0
0.1…100.0
Gain. When value is set to 0.1, the PID controller output
changes one-tenth as much as the error value. When value
is set to 100, the PID controller output changes one hundred
times as much as the error value.
1 = 0.1
4002 INTEGRATION
TIME
Defines the integration time for the process PID1 controller.
The integration time defines the rate at which the controller
output changes when the error value is constant. The
shorter the integration time, the faster the continuous error
value is corrected. Too short an integration time makes the
control unstable.
60.0 s
0.0 = NOT SEL
0.1…3600.0 s
Integration time. If parameter value is set to zero, integration
(I-part of the PID controller) is disabled.
1 = 0.1 s
All parameters
No.
Name/Value
Description
Def/FbEq
t
A = Error
B = Error value step
C = Controller output with gain = 1
D = Controller output with gain = 10
D (
= 10)
= 1)
B
A
Aotewell Ltd
www.aotewell.com
Industry Automation
HongKong|UK|China
+86-755-8660-6182