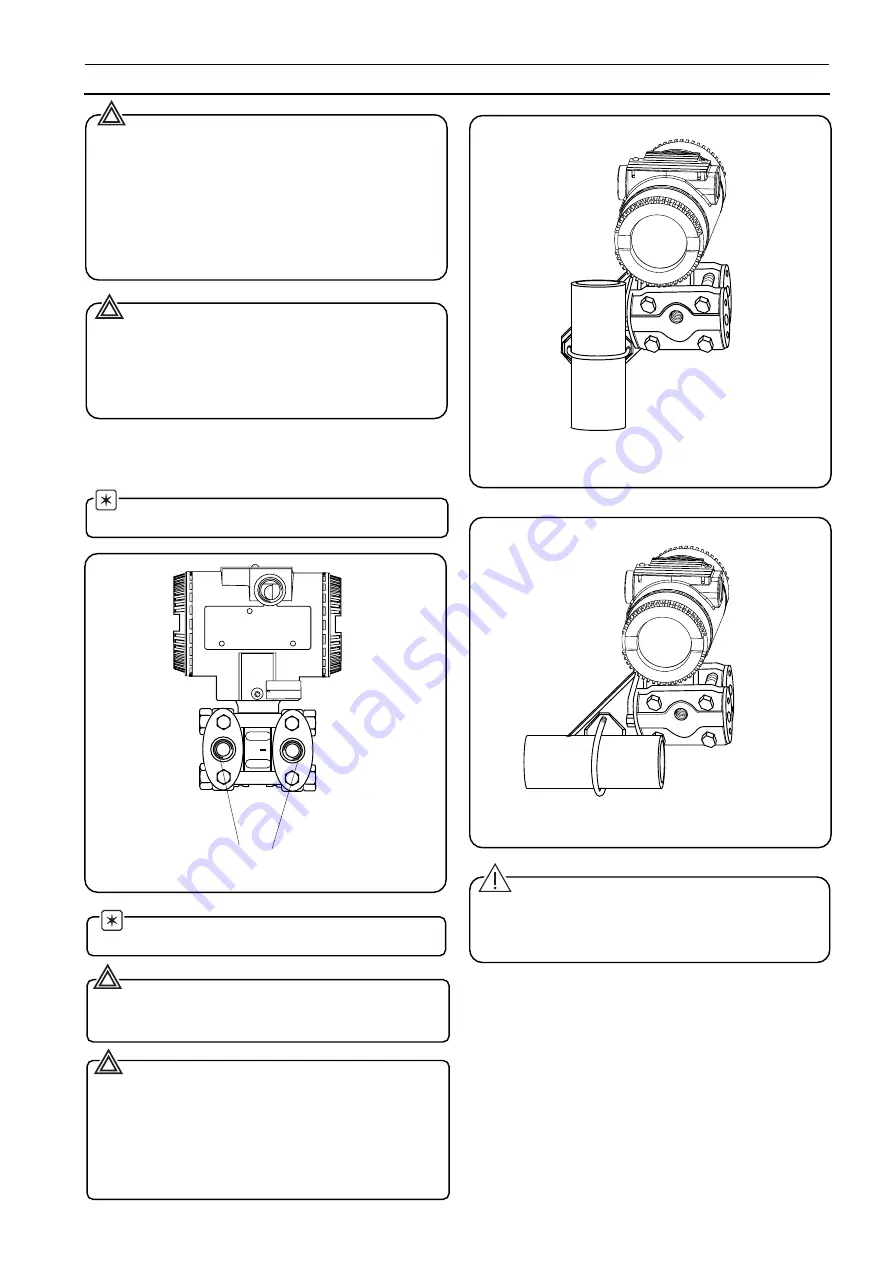
- 3 -
INSTALLATION
Fig. 6 - Mounting on 2" horizontal pipe
CAUTION - Proper location of the transmitter
with respect to the process pipe will depend upon the
service for which the instrument is used. Care should be
exercised to identify correct process connections.
The secondary unit of the transmitter may be rotated through
360
°
approx. with respect to the primary unit without
degrading performance or damaging the internal wiring. Do
not force the primary unit to rotate; use the 2 mm Allen key
supplied to unlock and lock the tang grub screw (see Fig. 7).
This feature, obtained by unscrewing (one turn is sufficient)
the Allen screw, is particularly useful for reaching optimum
access to the electrical connections and visibility of the output
indicator.
Fig. 4 - Process Connections
(Diff. Press. Transmitter)
WARNING
In order to ensure operator safety and plant safety it is
essential that installation is carried out by suitably
trained personnel according to the technical data
provided in the "Operative Limits" section in the
following of the document.
The transmitter may be mounted on a vertical or horizontal 2-
inch pipe (figg. 5 and 6) by means of the same mounting
bracket.
Note: for other installation details see the relevant
Addendum.
Fig. 5 - Mounting on 2" vertical pipe
Note:
High side may be marked H or +
Low side may be marked L or -
WARNING - For installation in Hazardous Areas,
i.e. areas with dangerous concentrations of e.g. gases or
dusts that may explode if ignited, the installation must be
carried out in accordance with relative standards either
EN 60079-14 or IEC 79-14 and/or with local authority
regulations, for the relevant type of protection adopted.
Together with safety information here and after enclosed
see also the Addendum for "Ex Safety" aspects which is
part of this instruction manual.
WARNING: The transmitter when installed in
accordance with this instruction manual will not be
subjected to mechanical stresses.
WARNING: the transmitter should not be installed
where it may be subjected to mechanical and thermal
stresses or where it may be attached by existing or
foreseable aggressive substances.
ABB cannot guarantee that a construction material is
suited to a particular process fluid under all possible
process conditions. See also the paragraph on "Operati-
ve limits".
+
Содержание 6X1ED
Страница 6: ... 6 CORROSION TABLE ...
Страница 7: ... 7 CORROSION TABLE ...
Страница 8: ... 8 CORROSION TABLE ...
Страница 9: ... 9 CORROSION TABLE ...
Страница 14: ... 14 ...
Страница 16: ... 16 PED600TEN Rev 1 ...