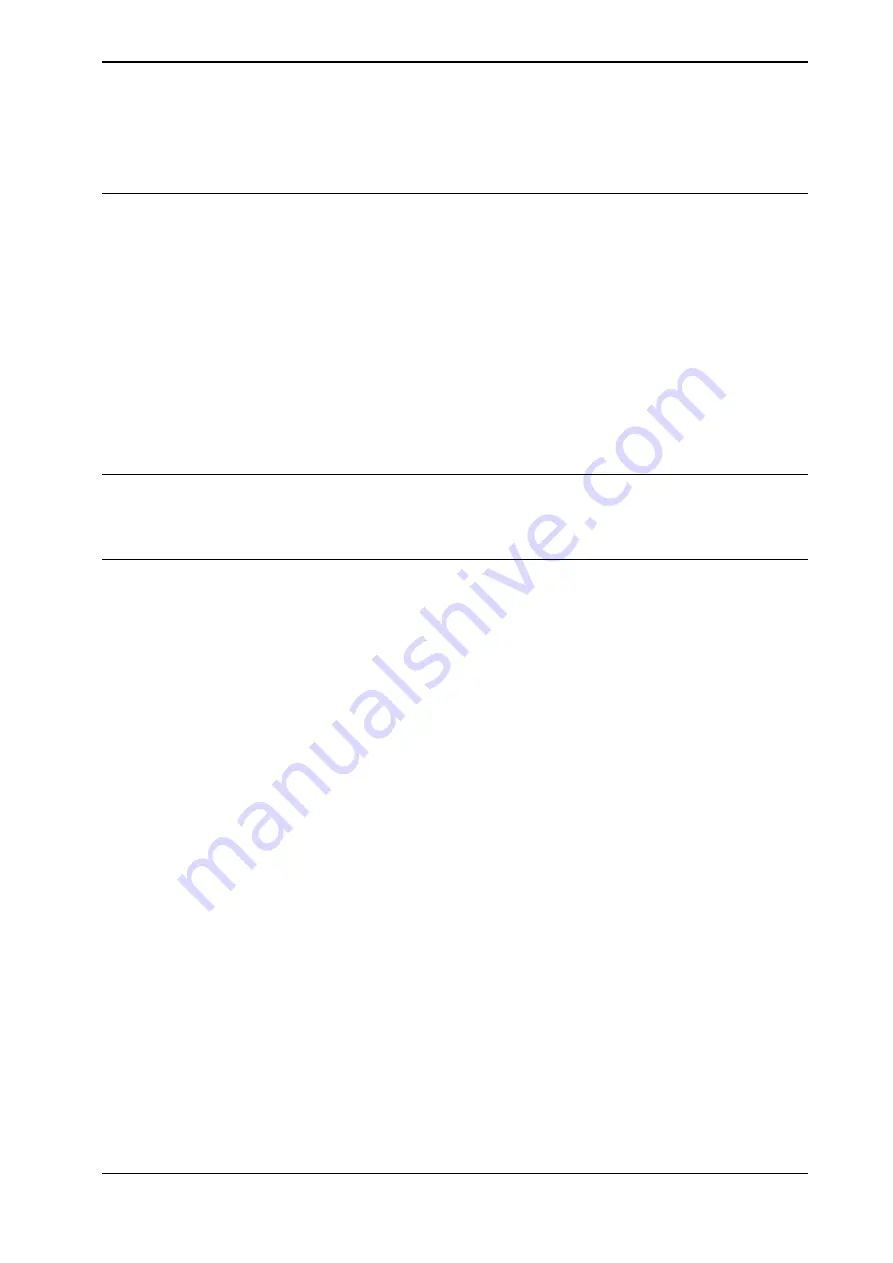
5.5 Frequently asked questions
How do I configure the digital input signal?
BullsEye scanning devices use a single digital input signal. The digital input must
be defined on an I/O board. The signal is commonly given the name
diBE_SENSE1
.
CONST be_device devYokeUp:=["diBE_SENSE1",TRUE,…
CONST be_device devYokeUp:=["diMyNewSense",TRUE,…
BullsEye must be informed of the name of the digital input. The name of the signal
is defined in the
be_device
data instance that is passed into the
BESetupToolJ
instruction. See
be_device
in
, and
BESetupToolJ
in
If the signal name is different from the default names provided, new BullsEye device
data must be created. For more information about this, see section
.
How do I implement multiple tools?
BullsEye can handle up to five different tools at a time by simply calling
BESetupToolJ
with five different tools.
How should robot carriers be configured?
Robots moved by carriers, such as tracks, must have the user frame coordination
defined for the carrier.
Example, the following definition will not work with BullsEye:
MECHANICAL_UNIT:
#
-name "TRACK" -use_run_enable "" -use_activation_relay "" \
-use_brake_relay "" -use_single_0 "TRACK" \
-stand_by_state -activate_at_start_up
-deactivation_forbidden
It should look like this:
MECHANICAL_UNIT:
#
-name "TRACK" -use_run_enable "" -use_activation_relay "" \
-use_brake_relay "" -use_single_0 "TRACK"
-allow_move_of_user_frame \
-stand_by_state -activate_at_start_up
-deactivation_forbidden
This is addition is needed to support coordinated work objects that have the user
frame moved by the track. It is always recommended to define tracks and other
robot carriers this way. Doing so also improves the usability of the system for other
reasons beyond the BullsEye requirements.
In addition to these mechanical unit settings, we also recommend that the BullsEye
sensor yoke be mounted to move with the robot. Doing so ensures that vibrations
in the robot carrier do not affect the relationship between the BullsEye sensor yoke
and the robot arm. Vibrations can yield poor TCP quality. Mounting the sensor with
Continues on next page
Application manual - BullsEye
51
3HAC050989-001 Revision: C
© Copyright 2004-2018 ABB. All rights reserved.
5 User guide
5.5 Frequently asked questions
Содержание 0503060880
Страница 1: ...ROBOTICS Application manual BullsEye ...
Страница 2: ...Trace back information Workspace R18 2 version a11 Checked in 2018 10 11 Skribenta version 5 3 008 ...
Страница 6: ...This page is intentionally left blank ...
Страница 22: ...This page is intentionally left blank ...
Страница 28: ...This page is intentionally left blank ...
Страница 84: ...This page is intentionally left blank ...
Страница 88: ......
Страница 89: ......