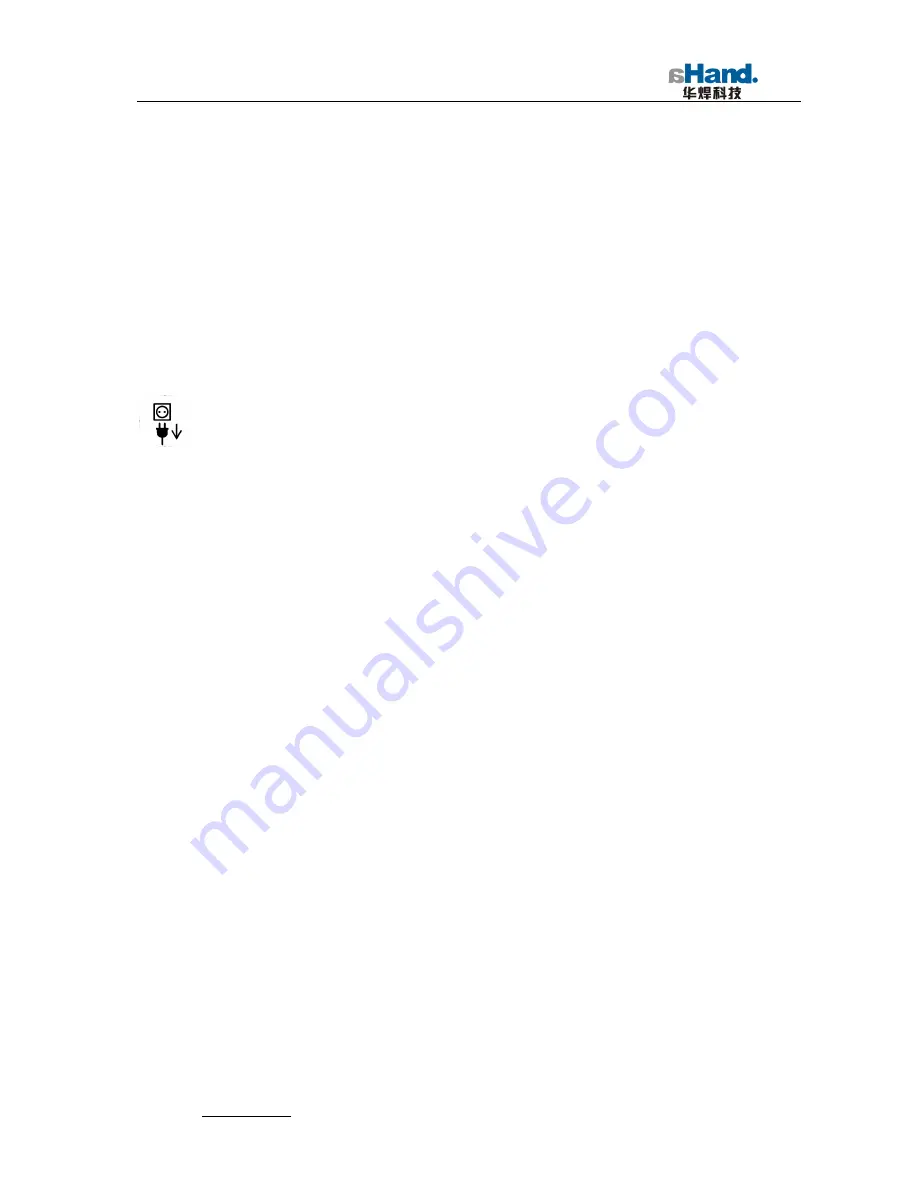
A-hand Technology Co., Ltd of Suzhou Industrial Park(215021) Operation instructions
Address: NO.88 Tangzhuang Road Suzhou-Singapore Industrial Park China
Tel: +86-512-6252-9140 Fax: +86-512-6252-2140
URL:http:// www.a-hand.com
issues must be paid attention to, which includes regular cleaning and inspection. Of course,
as described below, it depends on the amount of pollutants in the surrounding environment
and the welder‘s using hours.
The cleaning, inspection and maintenance of the welder must all be carried out by
professionals. If you do not follow the requirements of operation and result in failures,
please don‘t operate the welder again until the error is corrected.
4.1 Cleaning
Before cleaning, make sure that he welding power is away from the electric
fence.
Pull out the power plug!
(Cut or remove the fuse does not guarantee absolute insulation) pull out all the
connecting plugs of the welder head to power.
Welder head should be operated as follows:
If there is much dust, clean with dry compressed air.
The outer surface of welder head should be wiped with a piece of dry cloth.
The attached dirt of electrodes, welding torch head and other parts can be cleaned
after sand papering.
4.2 Maintenance
Cooling system
Regularly check the cooling system of the head to ensure that there is no leakage under
the pressure of 0.5mpa and check it every month to ensure that the normal flow is no less than
450ml/min. The proposed replacement of the coolant is once every quarter and distilled water
or deionized pure water if available can be used to replace the ordinary coolant. In cold
district
the coolant should be added a certain amount of alcohol (concentration 75%) in winter.
Rotary system
Rotation system should be kept in smooth operation state, no abnormal sound
in rotating. Regularly clean dirt produced by wear between the two bearings and
gear inside the head, and adds an appropriate amount of molybdenum disulphide
grease yearly.
Arc length control device