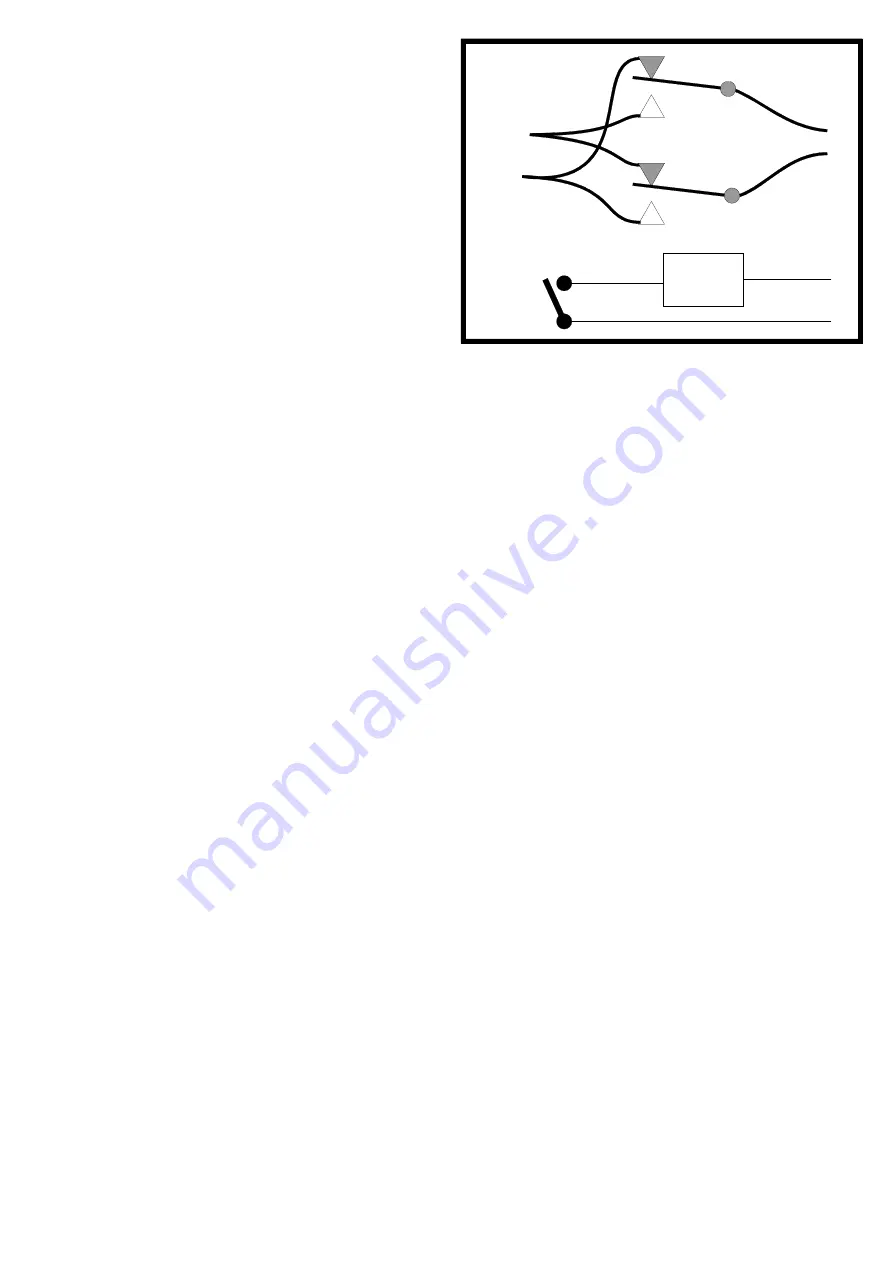
IMPORTANT: the switch or relay must not be
operated whilst the motor is running. To do so will
place great stress on the motor and mechanics. To
avoid this, put the reversing switch somewhere so
that it cannot easily be operated from the normal
driving position.
This is the main reason that reversing controllers are
available: they are configured so that reversing is safe
(to the controller) under all conditions, even when the
reversing switch is operated at full speed.
To motor
from Uni
n/c
n/o
n/c
n/o
c/o
c/o
Relay
coil
To
battery
Heat & Heatsinking
The rated current output of the controllers is with the
heatsink hot. When cold they will give considerably
more current. Thus the 35 amp version will in fact
give about 50 amps when cold. This is OK because
the MOSFETS used are rated at 60 amps continuous
with a case temperature of 25°C. As the MOSFETs
warm up their allowable current reduces so that at a
case temperature of 100 they can (only!) handle 45
amps continuous. The current limiting used in 4QD’s
controllers senses the MOSFET temperature and
automatically adjusts. However, running the
controllers at full current will cause speedy heating.
However, at some temperature (well above 100°C)
the MOSFETs will become unsafe, so we suggest
that, during initial use, you keep a note of the
heatsink temperature and, if it becomes much too hot
to touch, take appropriate steps, either by mounting
the Uni onto additional heatsinking or, better still, fit
a higher rated drive since heat is wasted battery
power and a larger drive will waste less. When using
an external heatsink remember that steel does not
conduct heat well: aluminium is far better.
For good heat conduction you must also use heatsink
compound between the Uni's on-board heatsink and
any external sink you fit.
I
nstead of a pot the input may be fed from a variable
voltage. 0v (common) to pin D, signal input (+ve) to
pin C.
Zero speed will be for zero voltage input and full
speed voltage may be adjusted (by the pre-set) to be
from 3v to above 20v.
If the input is a PWM signal, e.g. from a
microprocessor, and its amplitude may be above 5v,
then the pot fault protection circuit needs to be
deactivated. Two resistors are marked A and B on the
features diagram on page 3
To disable Pot fault, either disconnect A, or link out
(short circuit) resistor B.
Use as voltage follower