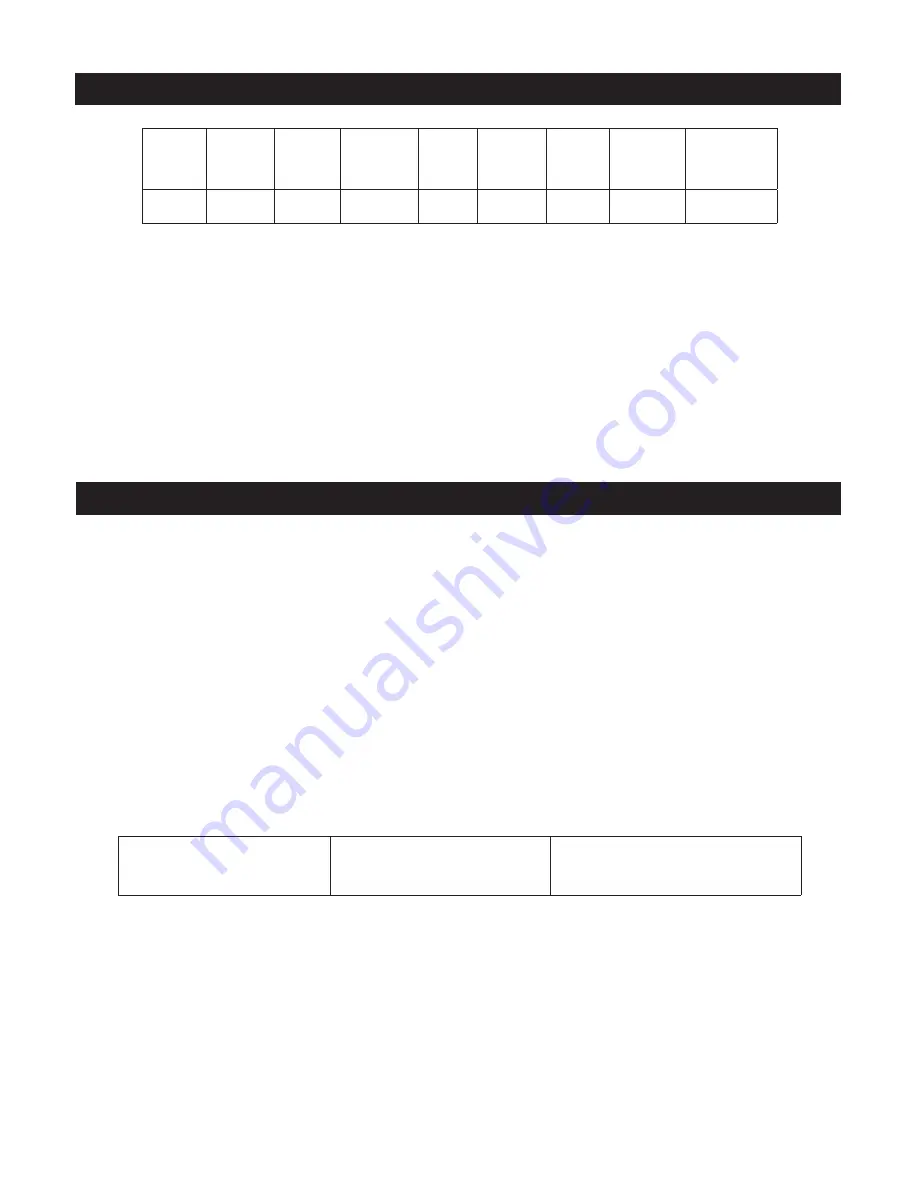
3M 3 in. Random Orbital Polisher
3
Revision 102309
3M 3 in. Random Orbital Polisher
3
Revision 102309
3M 3 in. Random Orbital Polisher
4
Revision 102309
Operating / Maintenance Instructions
Product Configuration/Specifications: 11,000 RPM Random Orbital Polisher
PRIOR TO THE OPERATION
The tool is intended to be operated as a hand held tool. It is always recommended that while using the tool, operators stand on a solid
floor, in a secure position with a firm grip and footing. Be aware that the tool can develop a torque reaction. See the section “SAFETY
PRECAUTIONS”.
Use a clean lubricated air supply that will give a measured air pressure at the tool of 6.2 bar (90 psig) when the tool is running with
the lever fully depressed. It is recommended to use an approved 10 mm (3/8 in) x 8 m (25 ft) maximum length airline. Connect the tool
to the air supply as shown in Figure 1. Do not connect the tool to the airline system without an easily accessible air shut off valve. It is
strongly recommended that an air filter, regulator and lubricator (FRL) be used as shown in Figure 1 as this will supply clean, lubricated
air at the correct pressure to the tool. In any case appropriate air pressure regulators shall be used at all times while operating this tool
where the supply pressure exceeds the marked maximum of the tool. Details of such equipment can be obtained for your tool distributor.
If such equipment is not used, the tool should be manually lubricated. To manually lubricate the tool, disconnect the airline and put
2 to 3 drops of suitable pneumatic motor lubricating oil such as 3M™ Air Tool Lubricant PN 20451, Fuji Kosan FK-20, Mobil ALMO 525
into the hose end (inlet) of the tool. Reconnect tool to the air supply and run tool slowly for a few seconds to allow air to circulate the oil.
If the tool is used frequently, lubricate it on a daily basis or lubricate it if the tool starts to slow or lose power. It is recommended that the
air pressure at the tool be 6.2 bar (90 psig) while the tool is running so the maximum RPM is not exceeded. The tool can be run at lower
pressures but should never be run higher than 6.2 bar (90 psig). If run at lower pressure the performance of the tool is reduced.
* Declared noise levels; measurements carried out in accordance with standard EN ISO 11203:1997 and EN ISO 3744:1997.
** Declared vibration levels in accordance with EN12096; measurements carried out in accordance with standard EN ISO 8662-8:1997.
IMPORTANT NOTE:
The noise and vibration values stated in the table are from laboratory testing in conformity with stated codes and
standards and are not sufficient risk evaluation for all exposure scenarios. The actual exposure values and amount of risk or harm expe-
rienced to an individual is unique to each situation and depends upon the surrounding environment, the way in which the individual
works, the particular material being worked, work station design, as well as upon the exposure time and the physical condition of
the user. 3M™ cannot be held responsible for the consequences of using declared values instead of actual exposure values for any
individual risk assessment.
Model
Number
Pad Size
mm (in.)
Replace-
ment Disc
Pad Part
Number
Spindle
Thread
Product
Net Wt
kg (lb)
Length
mm (in.)
*Noise
Level dBA
Pressure
(Power)
**Vibration
Level m/s
2
(ft/s
2
)
**Uncertainty
K
m/s
2
28363
76 (3)
07652
5/16 in.-24 T
0.81
(1.79)
132 (5.20)
77 (82)
8.85 (29.0)
1.5
Recommended Airline
Size - Minimum
10 mm
3/8 in
Recommended Maximum
Hose Length
8 meters
25 feet
Air Pressure
Maximum Working Pressure 6.2 bar 90 psig
Recommended Minimum
NA
NA