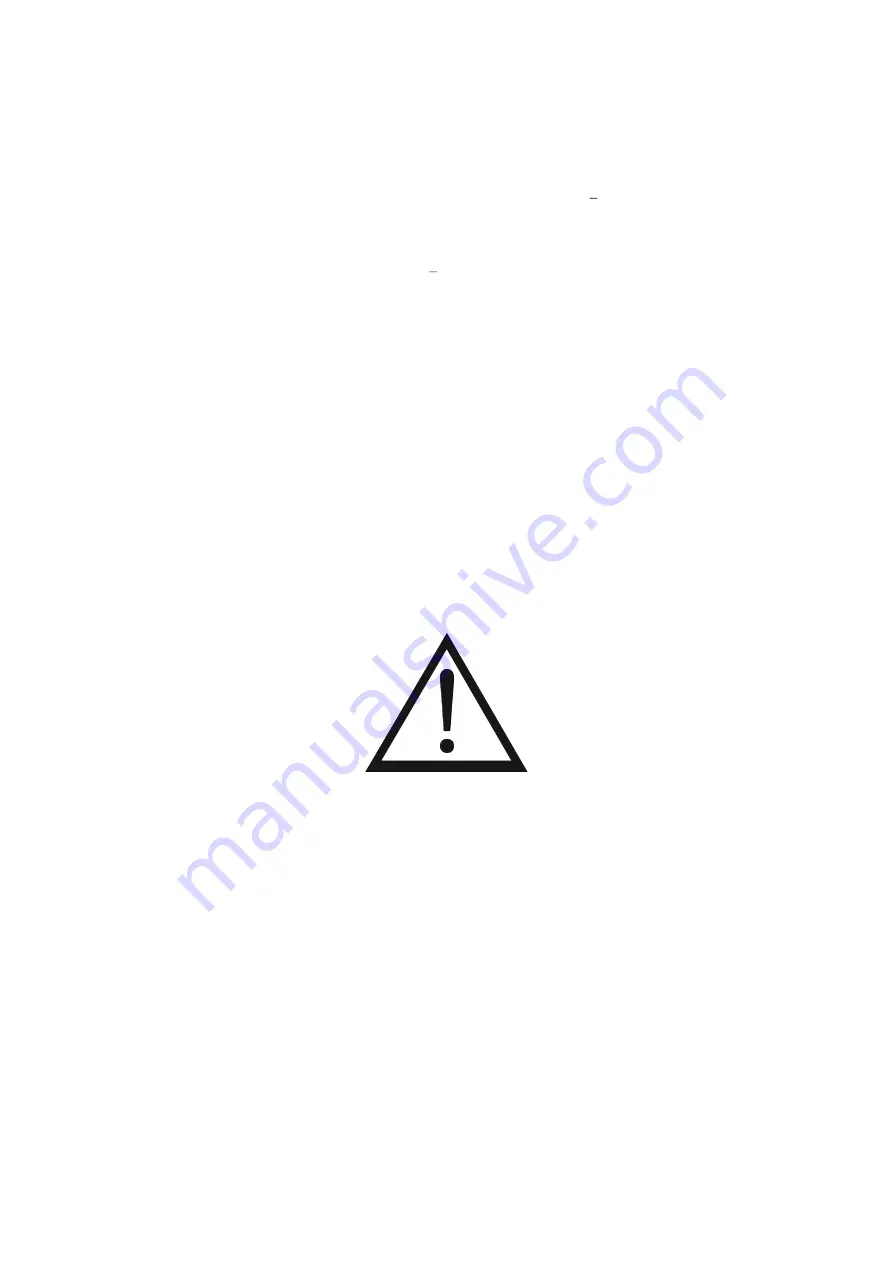
CAUTION: REFER TO MANUAL
THE INTERNATIONAL HAZARD SYMBOL IS INSCRIBED ADJACENT TO
THE REAR CONNECTION TERMINALS. IT IS IMPORTANT TO READ THE
MANUAL BEFORE INSTALLING OR COMMISSIONING THE UNIT.
PREFACE
This manual comprises two volumes:
Volume I:
This supports normal operation of the
1
8
-DIN
Digital Indicator. In normal operation, all actions
taken by the user are to be in front of the panel.
Volume II:
This supports the installation, commissioning and
configuring of the
1
8
-DIN Digital Indicator.
It is
intended for use only by personnel who are trained,
equipped and authorised to carry out these functions.