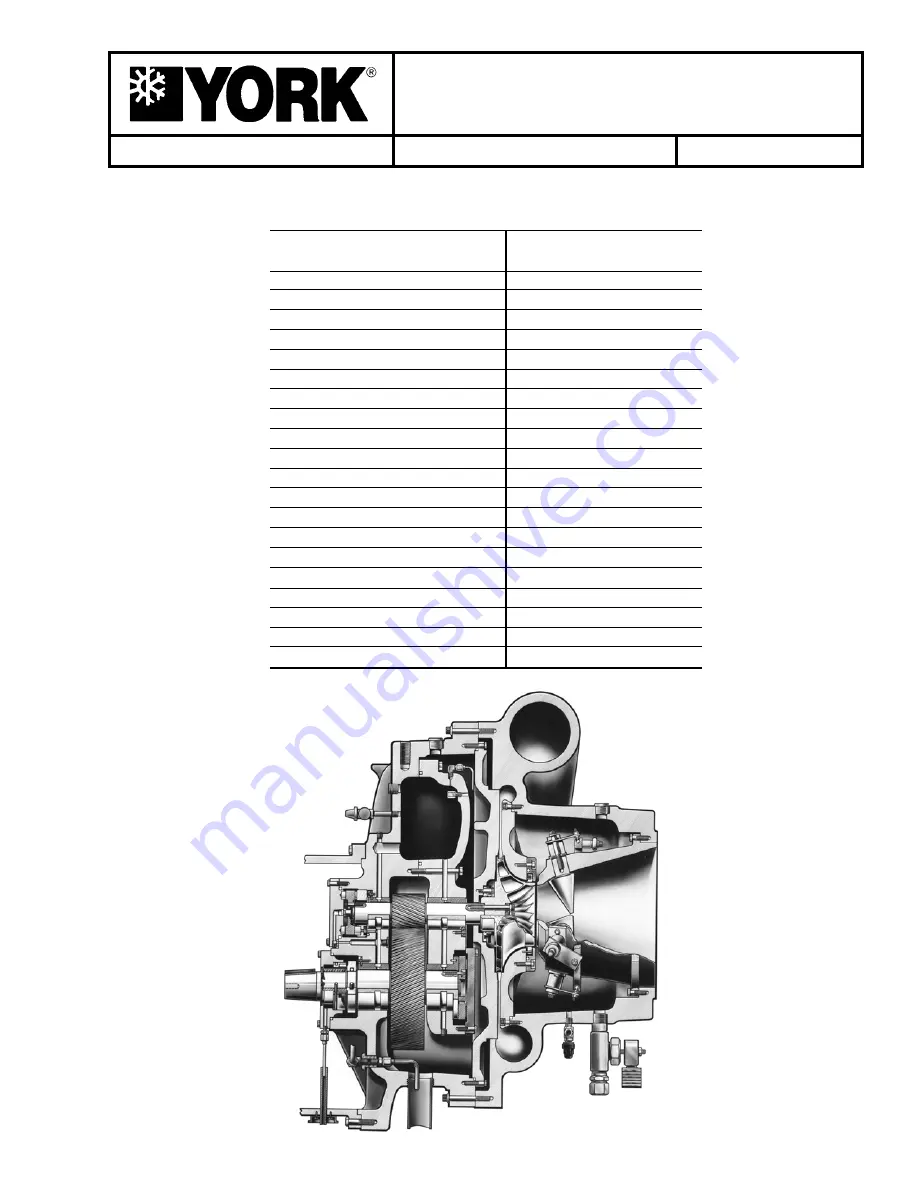
SERVICE INSTRUCTION
CENTRIFUGAL COMPRESSORS
Supersedes: 160.49-M1 (1292)
Form 160.49-M1 (601)
USED WITH YORK MODEL YK
CENTRIFUGAL LIQUID CHILLERS
26439A
COMPRESSOR
COMPRESSOR
MODEL
CODE
YDHF-39
P1
YDHF-40
P2
YDHF-42
P3
YDHF-44
P4
YDHA-36 & LHA-36
G3
YDHA-41 & LHA-41
G4
YDHA-46 & LHA-46
H0
YDHA-50N & LHA-50N
H1
YDHA-50W & LHA-50W
H1
YDHB-57, LHB-57, HA-57
H2
YDHB-61
H3
YDHD-46
H4
YDHD-50N & 50W
H5
YDHD-57
H6
YDHD-59
H7
YDHD-61
H8
YDHA-65 & LHA-65
J1
YDHA-73 & LHA-73
J2
YDHA-81 & LHA-81
J3
YDHA-90 & LHA-90
J4
(Also see NOMENCLATURE, page 5)