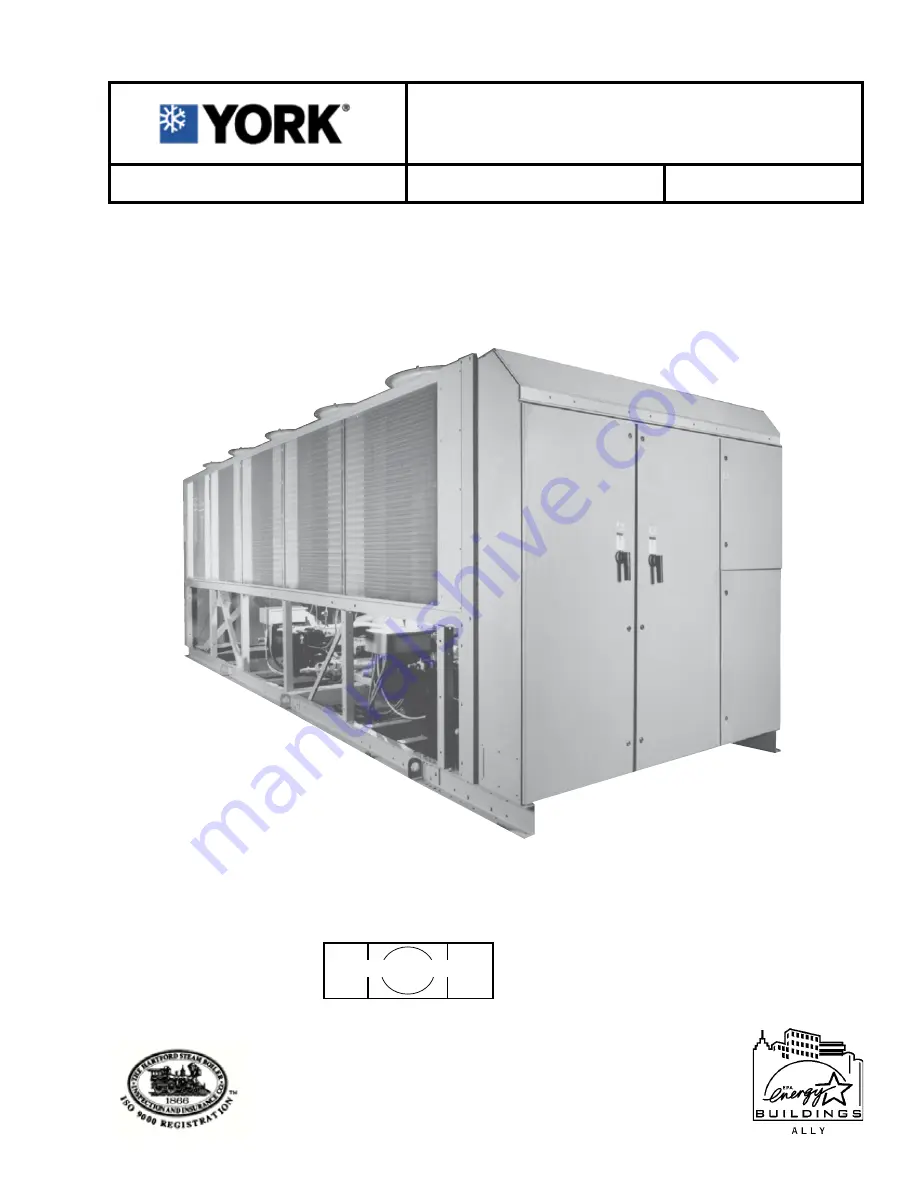
YCAS AIR-COOLED LIQUID CHILLERS
YCAS0098EB through YCAS0208EB
YCAS 2 SYSTEM EPROM
031-01798-001
(STANDARD, BRINE & METRIC MODELS COMBINED)
28971AR
60 Hz
AIR-COOLED SCREW LIQUID CHILLERS
INSTALLATION, OPERATION, MAINTENANCE
Supersedes: 201.18-NM7 (916)
Form 201.18-NM7 (1020)
Issue Date:
October 2, 2020
Summary of Contents for YCAS 0138EB
Page 50: ...50 JOHNSON CONTROLS This page intentionally left blank...
Page 61: ...61 JOHNSON CONTROLS FORM 201 18 NM7 This page intentionally left blank 7...
Page 70: ...70 JOHNSON CONTROLS Technical Data FIG 22A CONTROL PANEL COMPONENT LOCATIONS...
Page 71: ...71 JOHNSON CONTROLS FORM 201 18 NM7 LD03280 FIG 22B POWER PANEL COMPONENT LOCATION 7...
Page 72: ...72 JOHNSON CONTROLS Technical Data LEGEND LD03281...
Page 73: ...73 JOHNSON CONTROLS FORM 201 18 NM7 LD03282 LD03283 LD03284 7...
Page 74: ...74 JOHNSON CONTROLS Technical Data CONNECTION DIAGRAM SYSTEM WIRING LD06256 LD03231 LD03232...
Page 75: ...75 JOHNSON CONTROLS FORM 201 18 NM7 COMPRESSOR TERMINAL BOX LD03233 7...
Page 76: ...76 JOHNSON CONTROLS LD03285 Technical Data...
Page 77: ...77 JOHNSON CONTROLS FORM 201 18 NM7 3 4 5 6 3 4 5 6 7 8 5 6 3 4 7 8 9 10 LD06840A 7...
Page 181: ...181 JOHNSON CONTROLS FORM 201 18 NM7 NOTES...
Page 182: ...182 JOHNSON CONTROLS This page intentionally left blank...
Page 183: ...183 JOHNSON CONTROLS FORM 201 18 NM7 This page intentionally left blank...