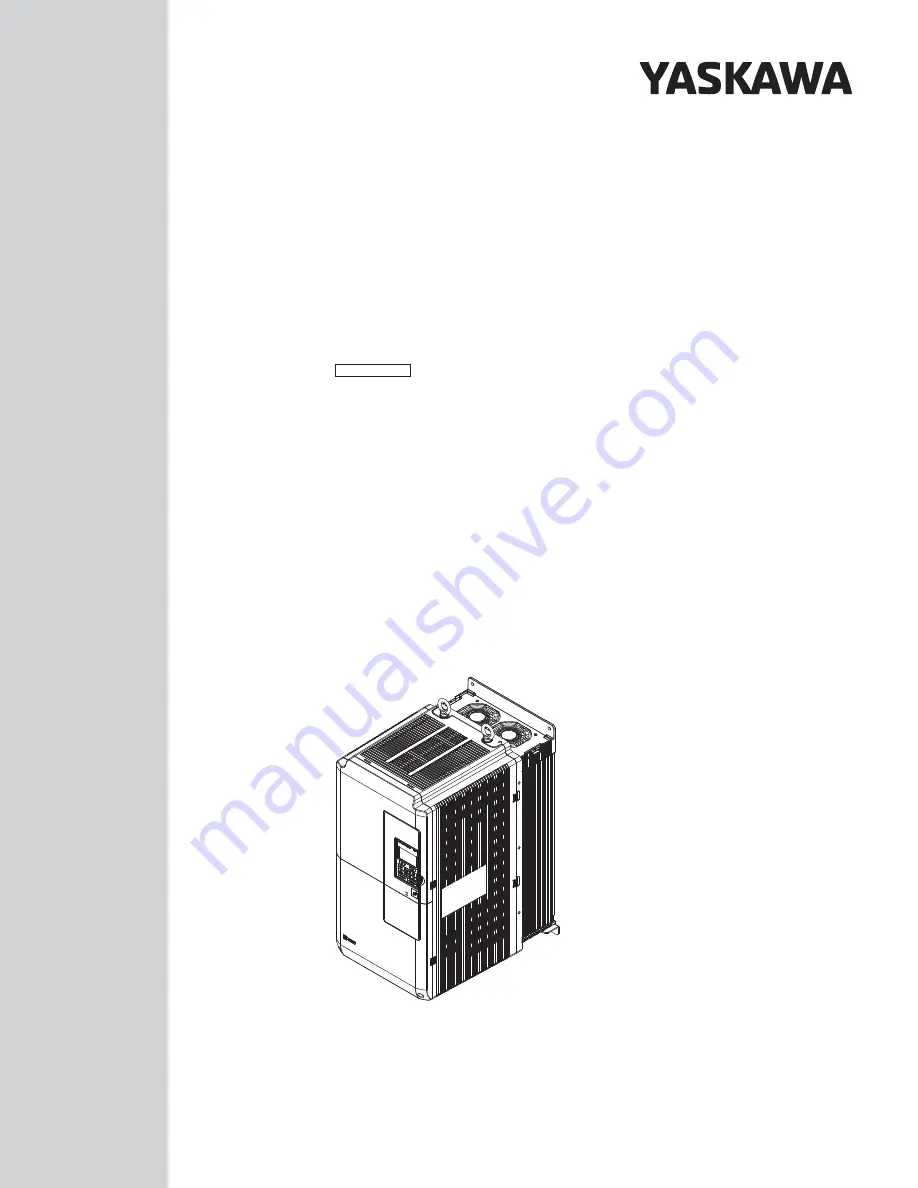
U1000 Industrial MATRIX Drive
Low Harmonic Regenerative Drive for Industrial Applications
Quick Start Guide
MANUAL NO. TOEP C710636 04D
To properly use the product, read this manual thoroughly and retain
for easy reference, inspection, and maintenance. Ensure the end user
receives this manual.
Type: CIMR-UU
Models: 200 V Class: 7.5 to 75 kW (10 to 100 HP ND)
400 V Class: 5.5 to 580 kW (7.5 to 775 HP ND)
Summary of Contents for U1000 iQpump Drive
Page 117: ......