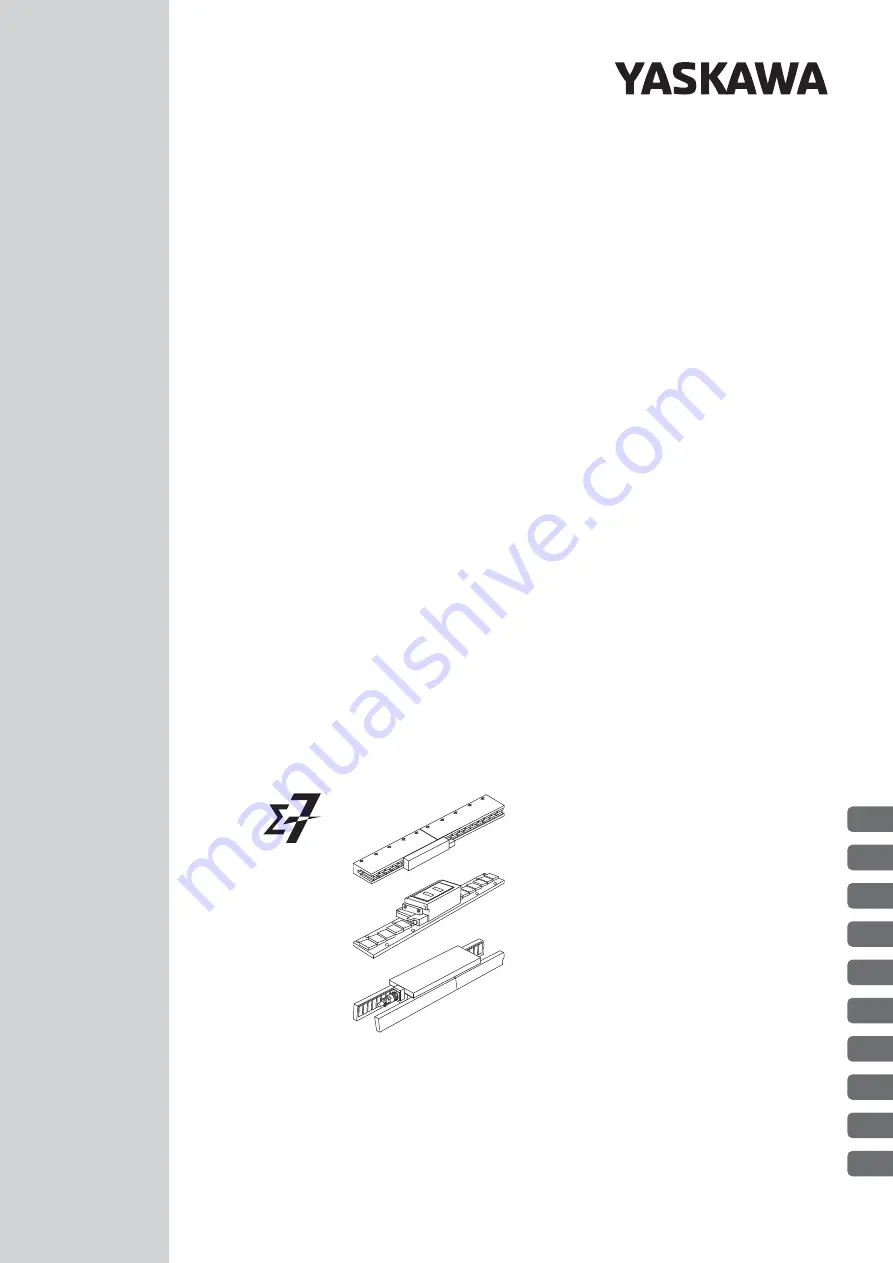
Model: SGLG/SGLF/SGLT
Linear Servomotor
-7-Series AC Servo Drive
Product Manual
MANUAL NO. SIEP S800001 37D
Basic Information on Servomotors
Capacity Selection
Equipment Design Precautions
Servomotor Installation
Connecting Linear Encoders
Maintenance and Inspection
Specifications, Ratings, and
External Dimensions of SGLG Servomotors
Connections between
Servomotors and SERVOPACKs
1
2
3
4
5
6
7
8
9
10
Specifications, Ratings, and
External Dimensions of SGLF Servomotors
Specifications, Ratings, and
External Dimensions of SGLT Servomotors