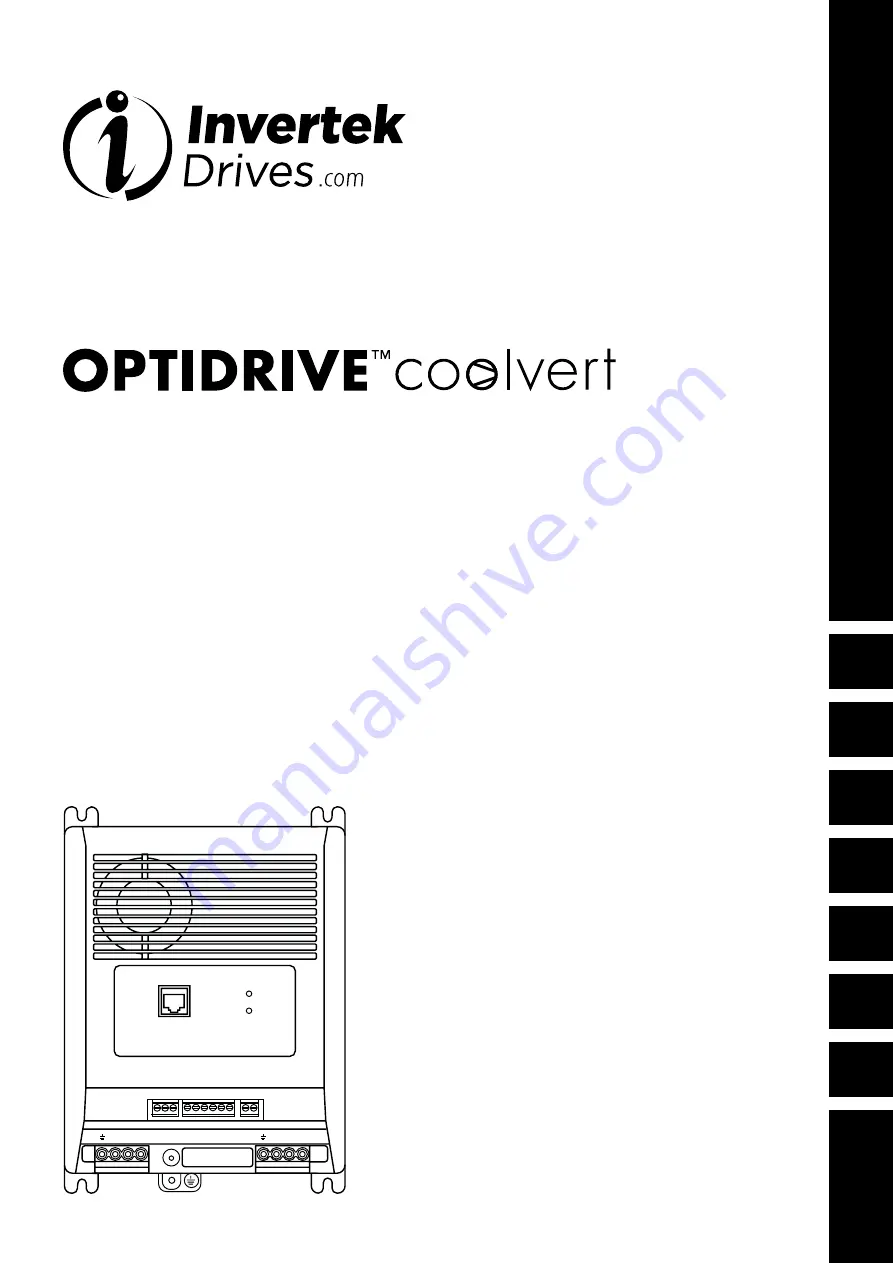
User Guide
AC Variable Speed Drive
1.5 - 3kW 200V Single Phase Input
5.5 - 11kW 400V Three Phase Input
2
Product Introduction
1
Important Safety Information
3
Installation
4
Set-up and Operation
5
Diagnostics
6
Technical
Specification
7
Useful Conversions
and Formulae
1 2 3 4 5 6 7 8 9 10 11
STATUS 1
STATUS 2
L1 L2 L3
U V W
EMC