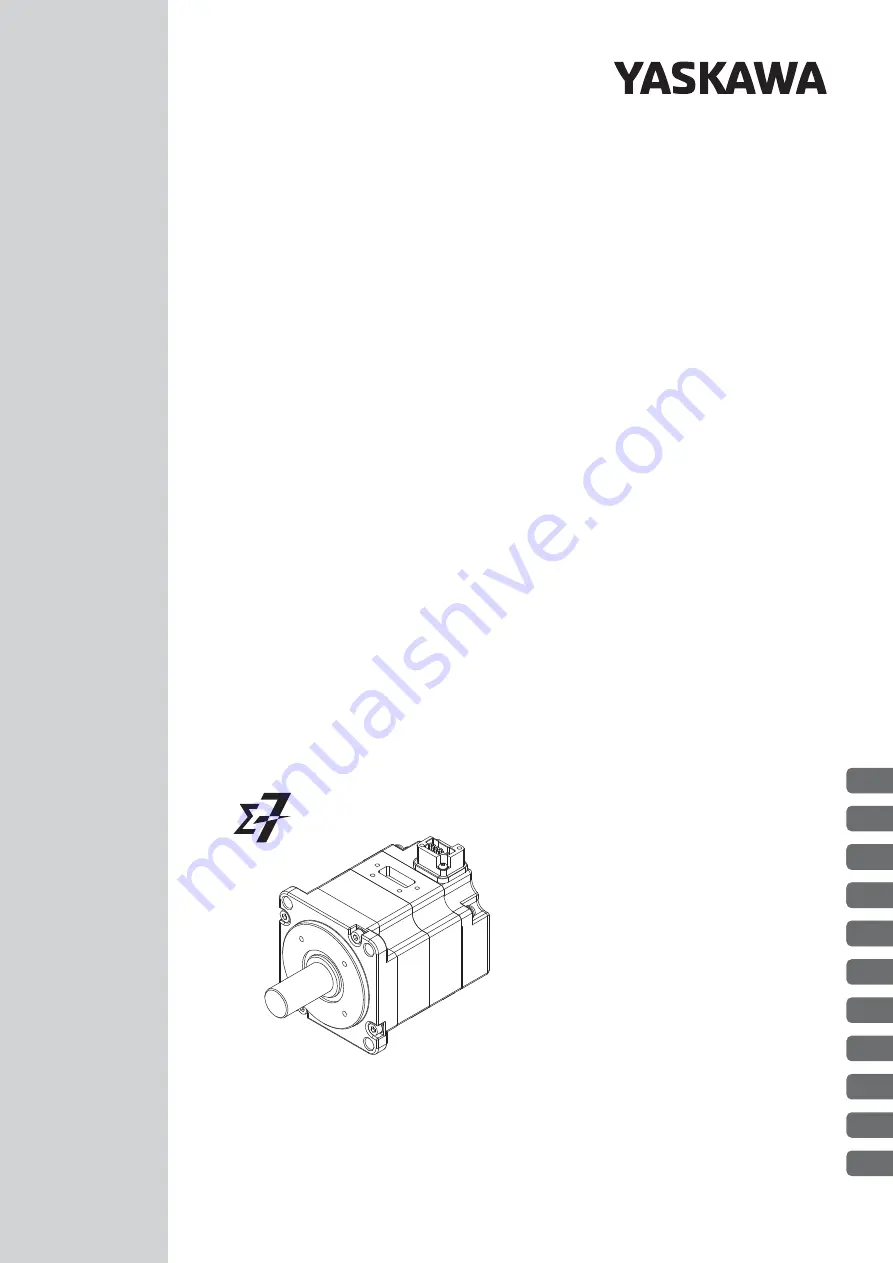
Model: SGMMV/SGM7J/SGM7A/SGM7P/SGM7G
Rotary Servomotor
-7-Series AC Servo Drive
Product Manual
MANUAL NO. SIEP S800001 36D
Basic Information on Servomotors
Capacity Selection
Servomotor Installation
Maintenance and Inspection
Appendices
Specifications, Ratings, and
External Dimensions of SGMMV Servomotors
Connections between
Servomotors and SERVOPACKs
Specifications, Ratings, and
External Dimensions of SGM7G Servomotors
Specifications, Ratings, and
External Dimensions of SGM7A Servomotors
Specifications, Ratings, and
External Dimensions of SGM7P Servomotors
1
2
3
4
5
6
7
8
9
10
11
Specifications, Ratings, and
External Dimensions of SGM7J Servomotors