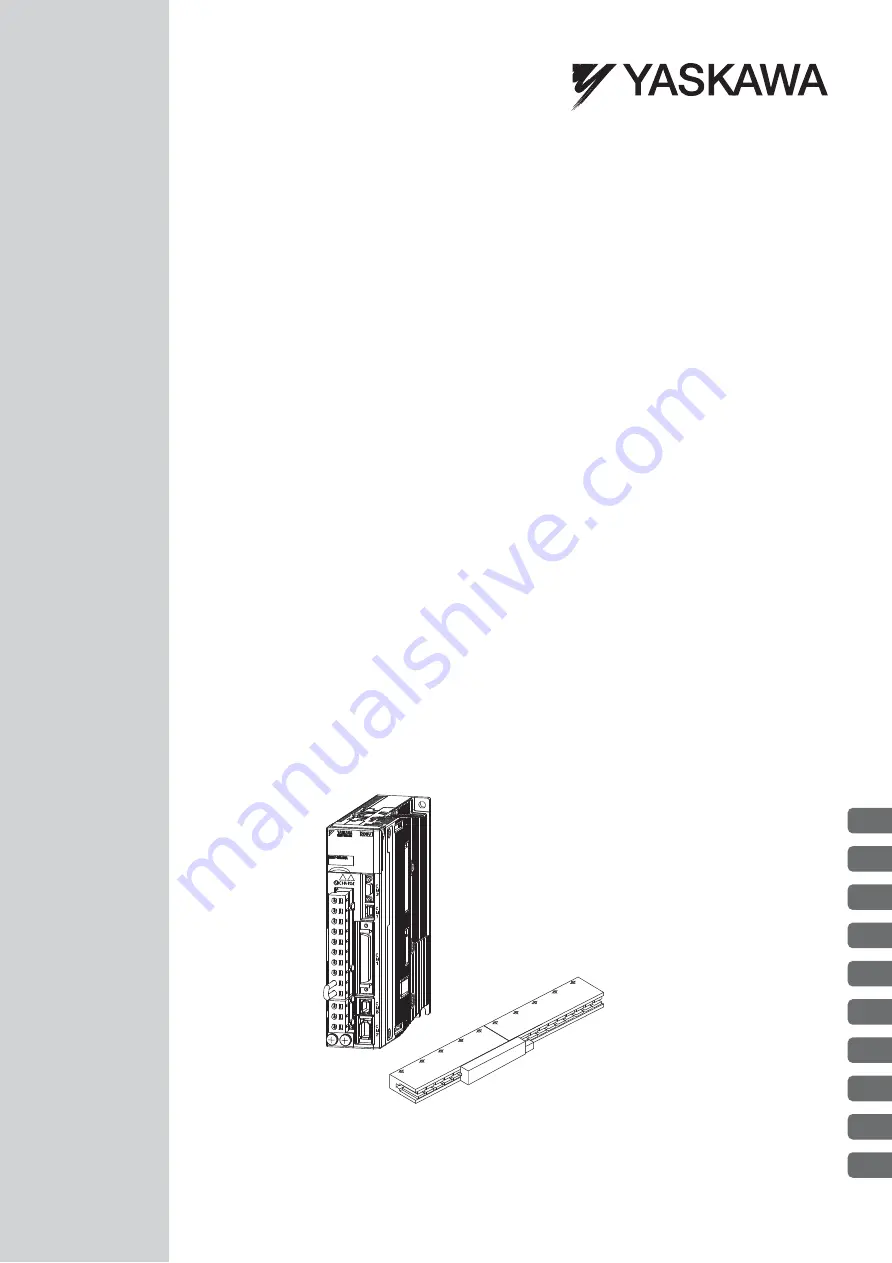
www.dadehpardazan.ir 88594014-15
SGDV SERVOPACK
SGLGW/SGLFW/SGLTW/SGLC/SGT Linear Servomotors
Linear Motor
Analog Voltage and Pulse Train Reference
-
V
Series
AC Servo Drives
USER'S MANUAL
Design and Maintenance
MANUAL NO. SIEP S800000 47G
1
2
3
4
5
6
7
8
9
10
Outline
Panel Operator
Wiring and Connection
Trial Operation
Operation
Adjustments
Utility Functions (Fn
)
Monitor Displays (Un
)
Troubleshooting
Appendix
Summary of Contents for SGDV SERVOPACK
Page 23: ...www dadehpardazan ir 88594014 15 xxii ...
Page 53: ...www dadehpardazan ir 88594014 15 2 Panel Operator 2 10 ...
Page 203: ...www dadehpardazan ir 88594014 15 5 Operation 5 11 5 Precautions for Safety Functions 5 86 ...
Page 275: ...www dadehpardazan ir 88594014 15 6 Adjustments 6 9 7 Position Integral 6 72 ...