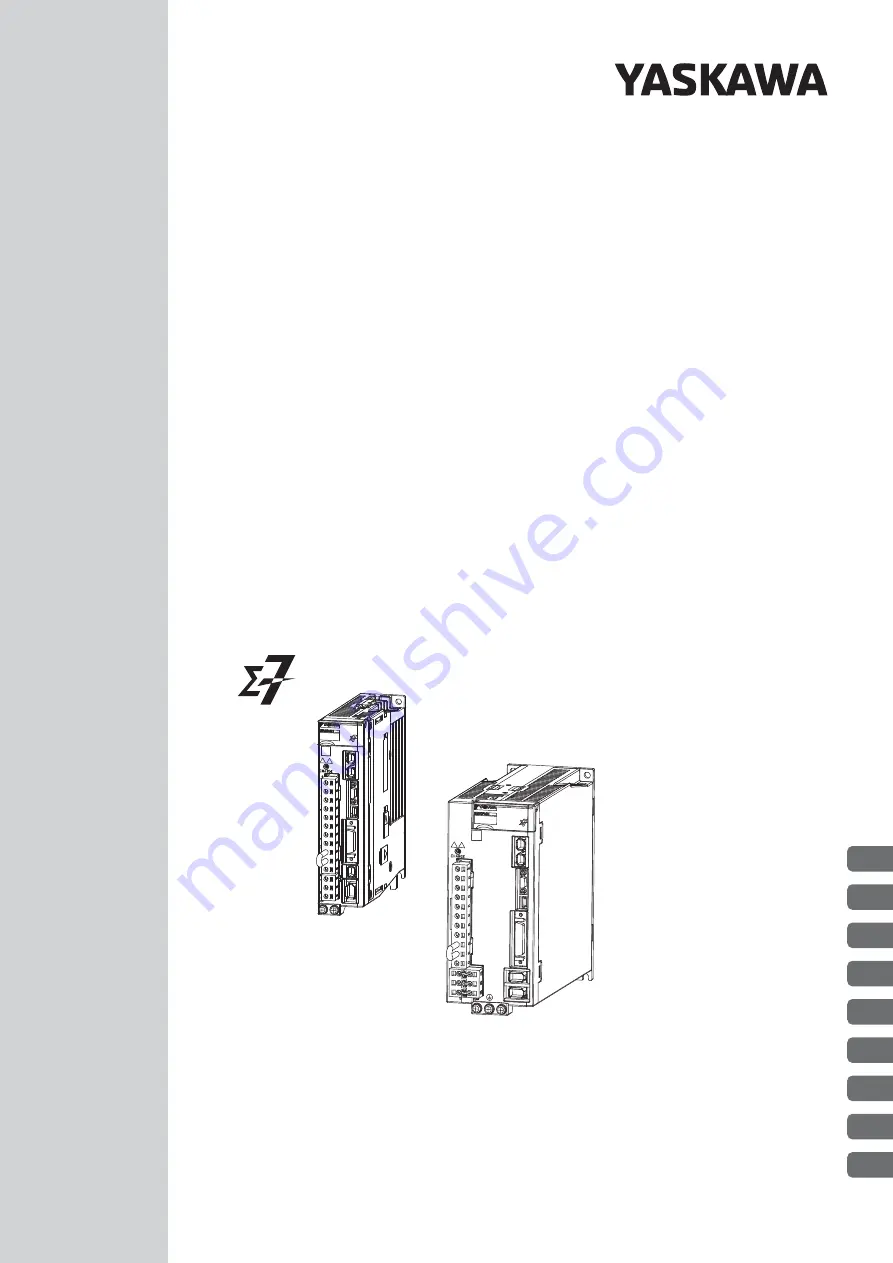
MECHATROLINK-III Communications
Standard Servo Profile
-7-Series AC Servo Drive
Command Manual
MANUAL NO. SIEP S800001 31C
1
2
3
4
5
6
7
8
9
Command Format
Main Commands
Subcommands
Operation Sequence
Function/Command Related Parameters
Common Parameters
Virtual Memory Space
MECHATROLINK-III
Communication Settings
Detecting Alarms/Warnings Related to
Communications or Commands