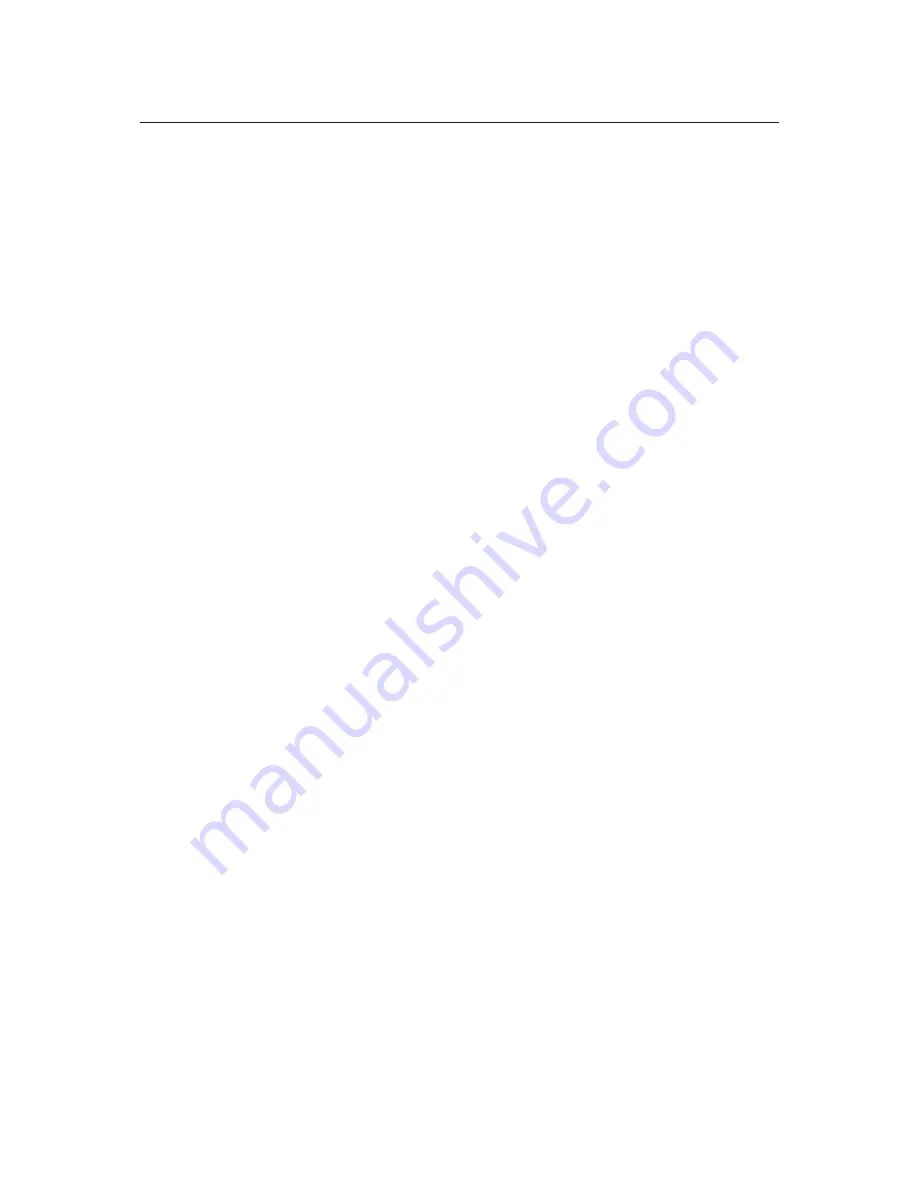
WARNINGS, CAUTIONS
AND NOTES
The terms WARNING, CAUTION and NOTE
have specific meanings in this manual.
A WARNING emphasizes areas where injury or
even death could result from negligence. Mechani-
cal damage may also occur. WARNINGS
should be
taken seriously
.
A CAUTION emphasizes areas where equipment
damage could result. Disregarding a CAUTION
could cause permanent mechanical damage, though
injury is unlikely.
A NOTE provides additional information to
make a step or procedure easier or clearer. Disre-
garding a NOTE could cause inconvenience but
would not cause equipment damage or personal
injury.
SAFETY
Professional mechanics can work for years and
never sustain a serious injury or mishap. Follow
these guidelines and practice common sense to
safely service the motorcycle.
1. Do not operate the vehicle in an enclosed area.
The exhaust gasses contain carbon monoxide, a poi-
sonous gas that is odorless, colorless, and tasteless.
Carbon monoxide levels build quickly in a small
enclosed area, and it can cause unconsciousness and
death in a short time. Make sure the work area is
properly ventilated or operate the vehicle outside.
2.
Never
use gasoline or any extremely flammable
liquid to clean parts. Refer to
Cleaning Parts
and
Handling Gasoline Safely
in this section.
3.
Never
smoke or use a torch in the vicinity of
flammable liquids, such as gasoline or cleaning sol-
vent.
4. When welding or brazing on the motorcycle, re-
move the fuel tank, carburetor and shocks to a safe
distance at least 50 ft. (15 m) away.
5. Use the correct type and size tool to avoid dam-
aging fasteners.
6. Keep tools clean and in good condition. Replace
or repair worn or damaged equipment.
7. When loosening a tight fastener, be guided by
what would happen if the tool slips.
8. When replacing fasteners, make sure the new
fasteners are of the same size and strength as the
original ones.
9. Keep the work area clean and organized.
10. Wear eye protection
any time
the safety of your
eyes is in question. This includes procedures in-
volving drilling, grinding, hammering, compressed
air and chemicals.
11. Wear the correct clothing for the job. Tie up or
cover long hair so it cannot be caught in moving
equipment.
12. Do not carry sharp tools in clothing pockets.
13. Always have an approved fire extinguisher
available. Make sure it is rated for gasoline (Class
B) and electrical (Class C) fires.
14. Do not use compressed air to clean clothes, the
motorcycle or the work area. Debris may be blown
into your eyes or skin.
Never
direct compressed air
at yourself or someone else. Do not allow children
to use or play with any compressed air equipment.
15. When using compressed air to dry rotating
parts, hold the part so it can not rotate. Do not allow
the force of the air to spin the part. The air jet is ca-
pable of rotating parts at extreme speed. The part
may be damaged or disintegrate, causing serious
injury.
16. Do not inhale the dust created by brake pad and
clutch wear. In most cases, these particles contain
asbestos. In addition, some types of insulating ma-
terials and gaskets may contain asbestos. Inhaling
asbestos particles is hazardous to health.
17. Never work on the vehicle while someone is
working under it.
18. When placing the vehicle on a stand, make sure
it is secure before walking away.
Handling Gasoline Safely
Gasoline is a volatile, flammable liquid and is one
of the most dangerous items in the shop.
Because gasoline is used so often, many people
forget that it is hazardous. Only use gasoline as fuel
for gasoline internal combustion engines. When
working on a vehicle, remember that gasoline is al-
ways present in the fuel tank, fuel lines and carbure-
tors. To avoid a disastrous accident when working
around the fuel system, observe the following
precautions:
1.
Never
use gasoline to clean parts. See
Cleaning
Parts
in this section.
2. When working on the fuel system, work outside
or in a well-ventilated area.
2
CHAPTER ONE