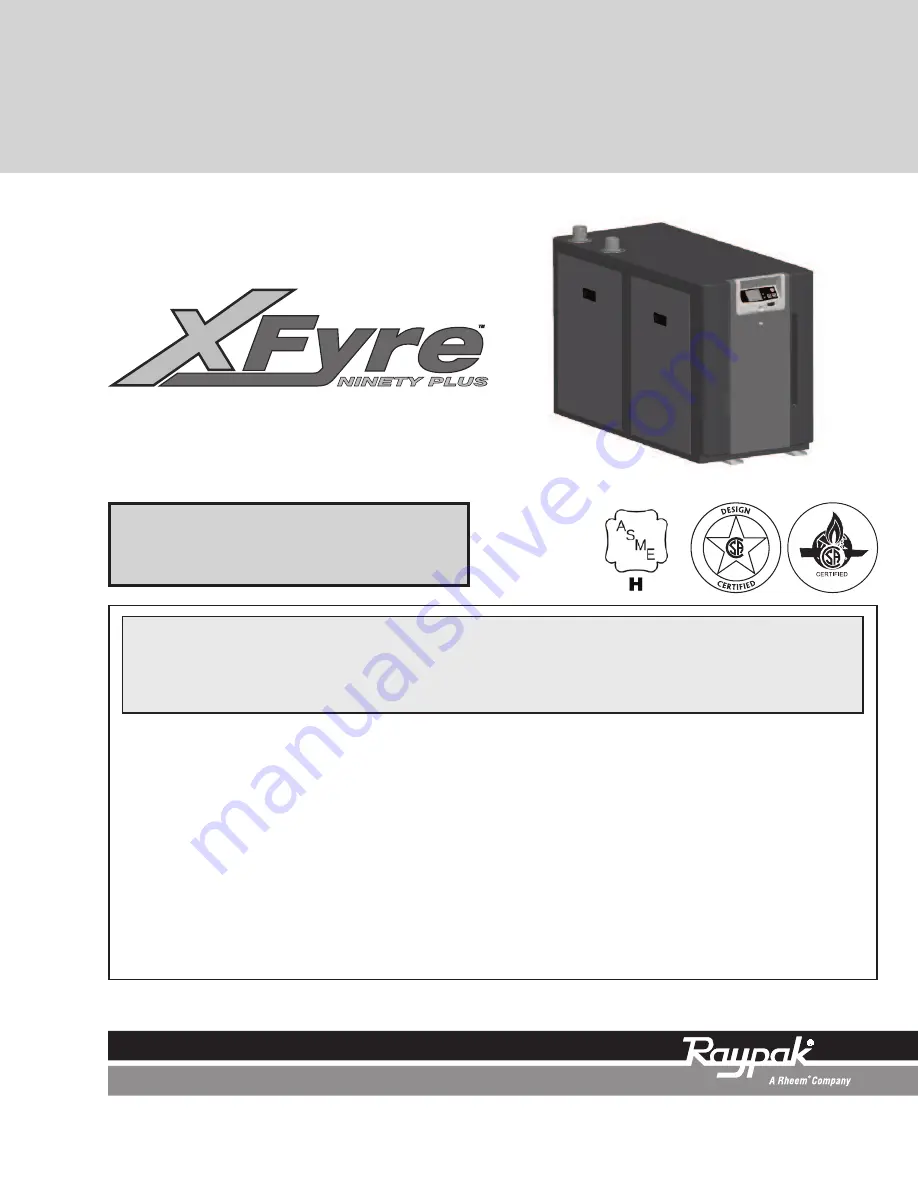
INSTALLATION & OPERATING
INSTRUCTIONS
Catalog No. 1000.65.2B
Effective: 08-02-13
Replaces: 06-10-13
P/N 241480 Rev. 3
WARNING:
Improper installation, adjustment, alteration, service or maintenance can
cause property damage, personal injury, exposure to hazardous materials* or loss of
life. Review the information in this manual carefully. *This unit contains materials that
have been identified as carcinogenic, or possibly carcinogenic, to humans.
FOR YOUR SAFETY:
Do not store or use gasoline or other flammable vapors and
liquids or other combustible materials in the vicinity of this or any other appliance. To
do so may result in an explosion or fire.
WHAT TO DO IF YOU SMELL GAS:
• Do not try to light any appliance.
• Do not touch any electrical switch; do not use any phone in your building.
• Immediately call your gas supplier from a neighbor's phone. Follow the gas
supplier's instructions.
• If you cannot reach your gas supplier, call the fire department.
Installation and service must be performed by a qualified installer, service agency or
the gas supplier.
This manual should be maintained in legible condition and kept adjacent to the heater or in a safe place for future
reference.
Models
300A–850A
Types H & WH
Summary of Contents for 300A
Page 44: ...WIRING DIAGRAM 44...